Increasing Weld Speeds in GTAW
By Edit Team | March 14, 2019 8:53 am SHARE
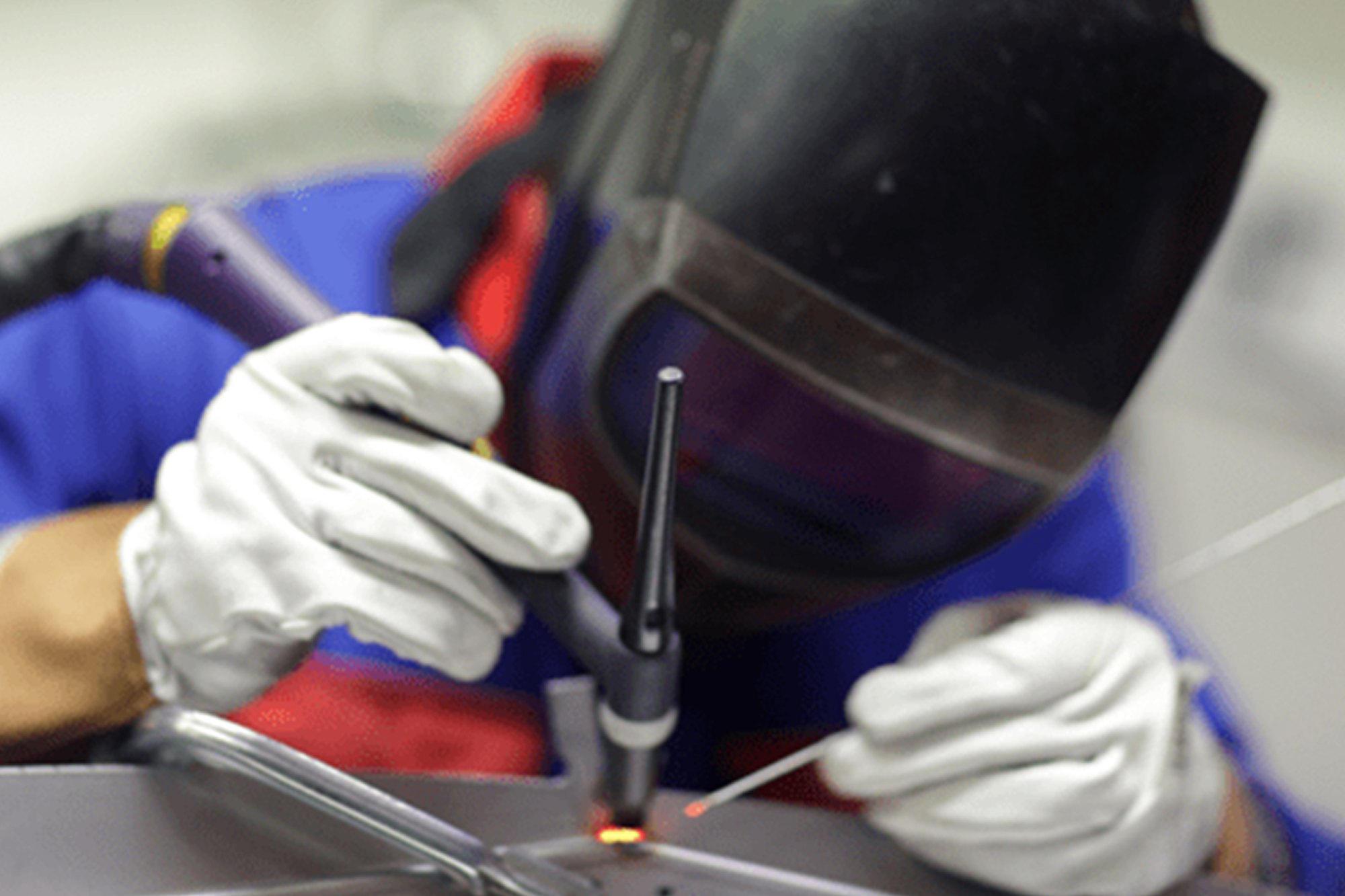
Gas Tungsten Arc Welding (GTAW) or Tungsten Inert Gas (TIG): The GTAW process is a versatile, all-position welding process that is widely used to join Ni-/Co-base alloys. In GTAW, the heat for welding is generated from an electric arc established between a non-consumable tungsten electrode and the work-piece.
The welding quality and appearance makes it the preferred method for most of the critical and many non-critical applications. Also, for code requirements such as pressure parts welding is needed usually the root runs are specified with TIG. Applications such as cladding and critical welding in nuclear and aerospace applications where high quality bonding and precision welding are required, the process is recommended over other faster processes such as GMAW, SAW or FCAW.
GTAW is considered as the best welding process for quality, superior joint appearance and bead formation, and possibility to use in all position welds; still it is avoided as it is considered a slow process. The energy efficiency of the process is poor. The skill level required for the welding is relatively high, as well.
GTAW has one basic advantage that it can be automated. There are now productivity enhancement tools available which help make the process faster. Such as cold wire feeder, weavers, oscillators, fully automated systems using AVC (automatic voltage correctors), hot wire GTAW, keyhole GTAW.
Cold wire feeders
Traditional manual welding includes fusion and addition of filler material by hand into the weld pool. During welding, the welder needs to stop when the filler length left to feed is too low (2 to 3 inches) and replaces it with the next filler wire. The stub end which is too short to be used is discarded. This can be typically 2 to 3 inches per metre amounting to 5 per cent of consumable costs which is wasted.
Cold wire feeders help feed the wire directly to the weld pool using a pen or special torch. A typical setup is shown in Figure 2. This helps makes the process semi-automatic as the wire feeding is taken care by the motorised wire feeder while the hand movement and other aspects of the GTAW are still taken care by the welder. This helps increase weld speeds as the welder doesn’t need to stop often for change of filler wire, the wire feed rate can be adjusted and increased for higher deposition rates. To increase deposition rate, feed rate needs to be increased, this reduces the inventory of varied sizes of filler wires required. The stub end losses are also negligible leading to saving of consumable cost.
This can also be clubbed with a hotwire power source, which helps bring up the temperature of the filler wire before entering in the weld pool. So the arc energy used to melt the wire in the pool is less and deposition rate are increased significantly. With the help of cold or hot wire feeder the semi-automatic solutions can double the speed of GTAW as compared to manual welding process.
Author details:
Nimesh Chinoy
Marketing Director – SigmaWeld
Electronics Devices Worldwide Pvt Ltd
Web – www.sigmaweld.com
Cookie Consent
We use cookies to personalize your experience. By continuing to visit this website you agree to our Terms & Conditions, Privacy Policy and Cookie Policy.