Industry 4.0: Digitizing the universe of welding
By Edit Team | October 31, 2019 12:39 pm SHARE
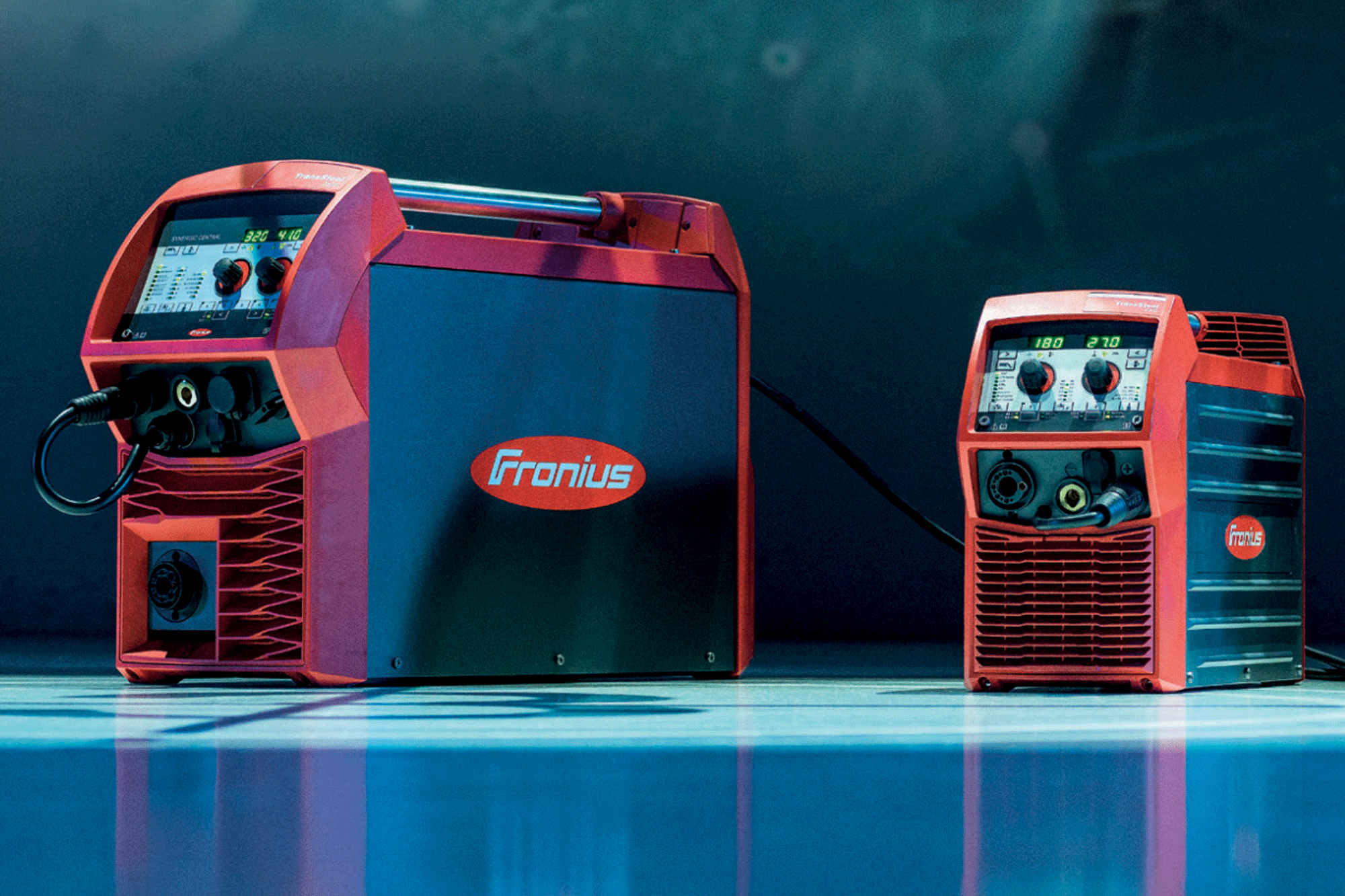
Since 1990s the full digitisation of the welding process and its digital control, have become the main topic of innovations.
The consistent implementation of Industry 4.0 also has a decisive influence on the factory of the future which will develop into a smart factory. For a smart factory« to work more or less autonomously without human interaction, some criteria must be met for welding applications: The welding know-how has to be digitized and prepared in such a way that a computer can make similarly correct decisions as an experienced welding technologist.
The welding equipment must be equipped with high-performance information and communication technology and customized sensors so that all production-relevant information can be digitized and given the necessary real-time behaviour of the system. The need to transfer and store large amounts of data requires powerful network infrastructures and sufficient storage capacity.
Concepts for data and communication security must be created and implemented. This will change the core business of a welding power source manufacturer:
In the early stages of welding technology the development was focused on the intensive examination of the direct conversion of electrical energy from the grid into suitable welding currents and voltages. In the 1990s, the full digitisation of the welding process and its digital control became the main topic of innovations.
Current welding systems have ultra-fast machine-internal and external data communication channels, high-resolution real- time control, the ability to store large amounts of data, IT security and intelligent human to machine or machine to machine communication.
In future fully automatic welding systems will independently and without human intervention organize the production of new parts and access the wide experience in the central storage systems. However, as long as the digitisation process in welding technology is not completely completed, humans will continue to play a central role in determining welding solutions. Accordingly, the communication channel between human / welding machine will continue to be one of the most important success factors.
Digitalized Welding Knowledge
A networked, modular welding cell must be equipped with the right welding parameters and welding consumable, depending on the task assigned by the production control. Nowadays the welding technologist holds responsibility for the right choice of welding parameters. If these tasks are to be supported by intelligent software systems in the future, it is necessary to digitize existing knowledge and make it automatically retrievable. This is probably the most difficult challenge of Industry 4.0 in welding technology, as all the existing knowledge is very difficult to quantify and therefore hardly comprehensible to digitisation . For autonomous cells, however, digitized knowledge is a prerequisite. In addition, digital information about the component, the filler metal, the protective gas, etc. is necessary in order to be able to determine an optimal set of welding parameters automatically. At this point, the integrated networking of the »smart factory must be effective and all information has to be available at the right time.
Cookie Consent
We use cookies to personalize your experience. By continuing to visit this website you agree to our Terms & Conditions, Privacy Policy and Cookie Policy.