Integrate digital welding technologies to minimise downtime
By Edit Team | May 13, 2024 1:50 pm SHARE
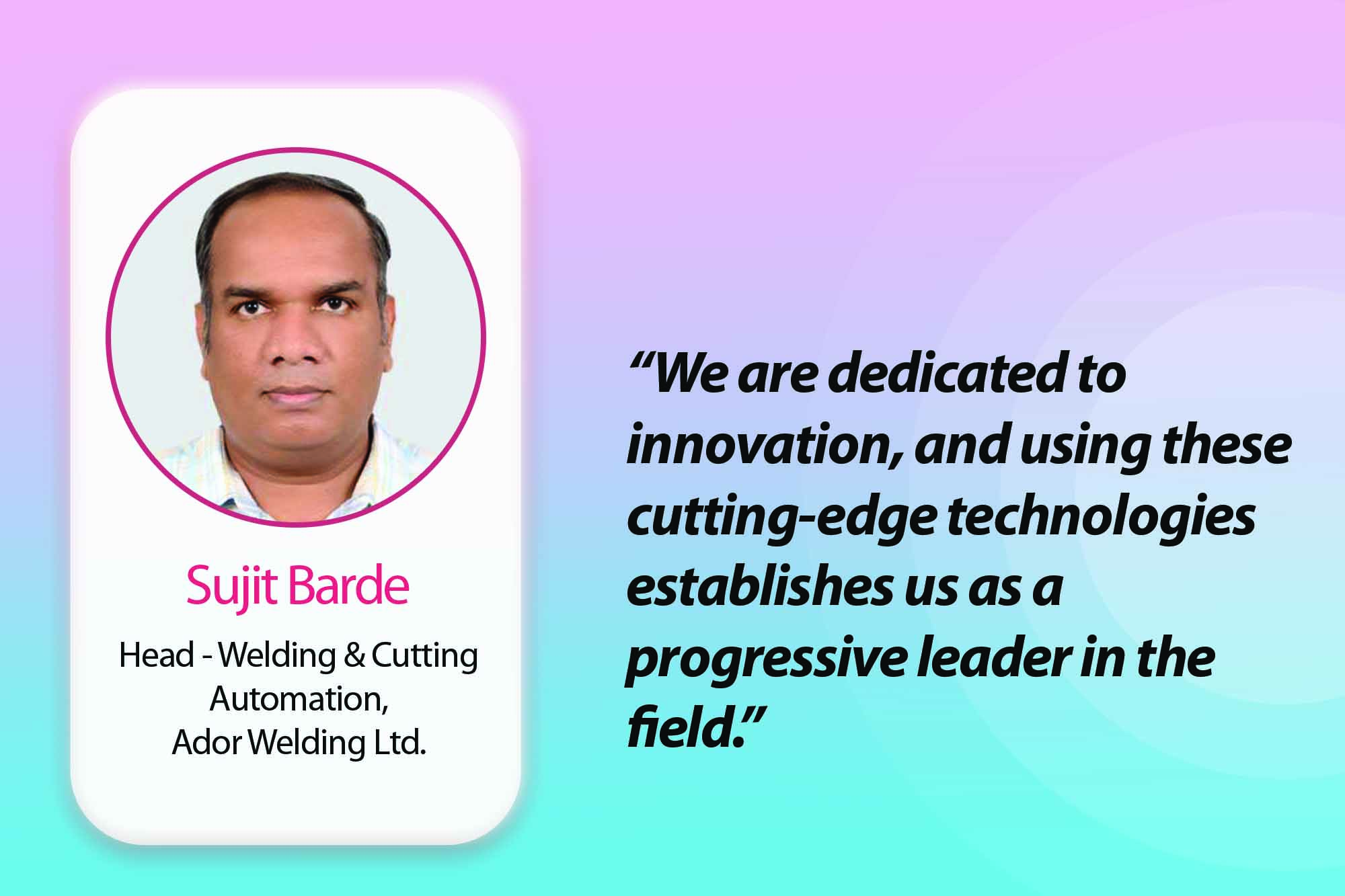
With its dedicated Technological Development Centre, Ador Welding is pioneering groundbreaking solutions to tackle the unique challenges encountered in construction and infrastructure projects.
Could you discuss some recent innovative products or technologies introduced by Ador Welding?
Our approach to addressing the dynamic challenges in welding across diverse sectors revolves around innovation. To achieve this, our Technological Development Centre plays a major role with its team of Engineers in multiple disciplines and state-of-the-art Design, Validation and Testing facilities as per International Standards, focusing on continuous improvements to existing products and the development of innovations.
One notable recent advancement is the Rhino E Electric Welder. Rhino E represents a remarkable leap forward in welding technology, designed with a strong emphasis on reducing carbon emissions and noise levels. Notably, this marks the introduction of the first battery-powered electric welder in India.
In addition to these innovations, integrating digital welding technologies is crucial for minimising downtime and enhancing efficiency. These technologies offer real-time insights, control, monitoring, and predictive maintenance. Through R&D initiatives, we remain at the forefront of technical progress. Hence, we are dedicated to innovation, and the use of these cutting-edge technologies establishes us as a progressive leader in the field who can satisfy our clients’ constantly changing needs.
With Industry 4.0 driving digitalisation and data-driven processes, how has Ador Welding integrated digital technologies into its welding solutions?
Ador has introduced IoT-enabled welders with wireless communication protocols for robotic applications and remote data monitoring. It is possible to view and monitor the operation of multiple equipment units at the same location through a central monitoring system, with HI-LO alarm indications during equipment operation. This ensures the repeatability of welding parameters and the consistent quality of the end product.
Additionally, predictive maintenance of parts nearing the end of their working life is now feasible through intelligent sensing and monitoring temperature, bearing noise (in the case of rotary welders), and continuous monitoring of multiple engine parameters for engine-driven welders.
With over five decades of experience in Welding & Cutting Automation, how has your WCA division evolved to meet the changing demands?
At Ador, we continually embrace new technologies and foster partnerships with innovative brands that help us meet the challenging demands of the industry and stay ahead of the curve.
One of the critical advancements in our automation portfolio is introducing the TIPTIG process. The TIG process is slow and requires highly skilled operators, demanding intense concentration as they engage in significant manual labour. By introducing the TIPTIG process, we’ve minimised elements of operator involvement, reduced stress levels, and enhanced efficiency. One key advantage is the decreased reliance on skilled labour and reduced manual intervention, leading to improved productivity.
We also leverage our partnership with innovative global brands like Inrotech (whom we exclusively represent in India). The previously tedious process of creating CAD drawings, uploading them, and running offline robot programming processes before welding has been revolutionised with the automation solutions offered by Infotech. The workflow has been streamlined by employing a method where the system autonomously scans the entire weld area using scanners and sensors. This process generates its map, establishes the structure, and determines the welding requirements based on predefined programs. Consequently, this eliminates the need for a programmer, enabling the system to perform its tasks efficiently. This technology is predominantly utilised in shipbuilding due to the necessity for lengthy welds and various weld structures. The ease of use is evident as the dependency on skilled labour diminishes, resulting in fewer defects and consistent weld quality.
Can you provide an overview of the CNC Cutting Machine product line, including the different types of machines available?
Ador specialises in offering a diverse range of CNC Cutting Machines tailored to meet the specific demands within the construction sector. Our product line comprises three primary categories, each catering to distinct requirements:
Our CNC Cutting Machines are available in oxyfuel and plasma cutting variants. The selection between the two depends on factors such as desired finish, fitment, and cutting precision, ensuring optimal outcomes for our customers.
We provide CNC Drilling Machines, which are essential for drilling various types of holes, catering to different diameters and fitment needs. These machines are critical in facilitating mechanical fitment assembly within construction projects.
Our End Face Milling Machines play a critical role in end face milling applications for H Beams. These beams are fundamental components utilised in erecting structures during bridge construction, emphasising the significance of this machinery in such projects.
In addition to these offerings, we present the King Cut Smarty—a user-friendly, portable, and automated cutting solution. This versatile system can seamlessly integrate with oxyfuel or plasma setups, making it ideal for smaller-scale applications.
Our products’ utility extends across diverse construction projects, including railways. In this sector, our machines are instrumental in building railway bridges over canyons, facilitating the efficient completion of such endeavors.
How does your range of Personal Protective Equipment (PPE) address the safety needs of workers in the construction and infrastructure sectors?
Ador has all the PPE required for all welding applications and processes, particularly at construction sites where SMAW and FCAW processes are utilised. Specific gloves suitable for these processes are employed. TIG Gloves with more flexibility are utilised at project sites where the GTAW process is used. Other protections such as aprons, sleeves, leg guards, and welding shields/welding helmets are necessary for all welding processes as common protection requirements.
Ador offers gloves that can be used for multipurpose tasks, including handling workpieces and providing protection against the heat generated by welding arcs.
Ador Welding has emphasised sustainability in its product development, such as the Rhino E Electric Welder. How do these environmentally friendly solutions contribute to the sustainability goals of construction and infrastructure projects?
Normally, electricity is not available at construction and infrastructure project sites. In that case, welding is done by machines connected to power generators or engine-driven welding machines, which adds to carbon emissions in the environment.
Ador is continuously working on reducing carbon emissions by developing new products. We have developed a battery-operated welding machine called the E-Welder, with the brand name RHINO-E, for work sites where electricity is unavailable. With zero carbon emissions, this machine provides an environmentally friendly solution at such sites.
Cookie Consent
We use cookies to personalize your experience. By continuing to visit this website you agree to our Terms & Conditions, Privacy Policy and Cookie Policy.