Intelligent welding
By Staff Report | August 13, 2024 6:52 pm SHARE
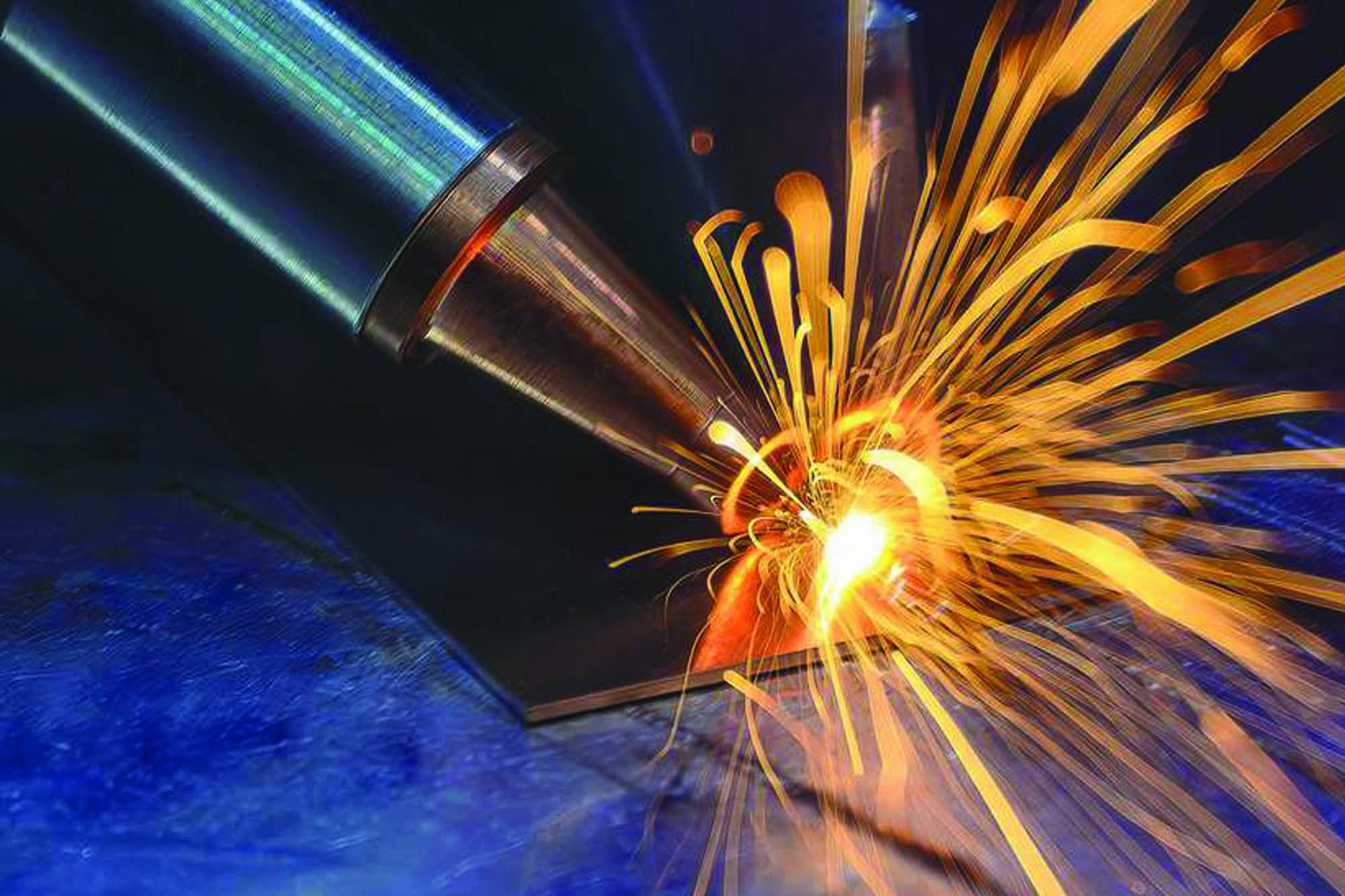
Intelligent welding systems are transforming global manufacturing by harnessing AI and robotics to boost precision, efficiency, and safety. This story offers a glimpse into the latest industry innovations and trends, featuring insights from leading experts driving these advancements.
The welding industry, a linchpin in modern manufacturing, faces an evolving landscape of challenges and opportunities. From overcoming skill shortages to adopting advanced technologies, professionals across the sector are pushing the boundaries of what’s possible. Insights from leading experts reveal a dynamic shift toward intelligent systems, fibre laser welding, robotic advancements, and green practices. This comprehensive overview explores how these innovations reshape the welding world, ensuring greater precision, efficiency, and sustainability.
Overcoming welding challenges
Essential yet complex welding poses significant challenges, from selecting optimal parameters to maintaining consistency across various materials. The advent of intelligent welding systems is revolutionising this landscape. Amlan Saha from Fronius India states, “Intelligent systems are not just enhancing precision; they are fundamentally changing how we approach welding.” These systems integrate advanced technologies like smart card devices, which provide Internet of Things (IoT) functionalities for improved traceability and quality control.
One of the standout features of these systems is the intelligent teaching mode. Traditional robotic welding setups often require meticulous manual adjustments, leading to potential errors and inefficiencies. Saha explains, “With intelligent teaching, we can simplify robotic setups, drastically reducing time and minimising rework.” This innovation is particularly beneficial in applications like thick plate welding for bogie frames and thin material welding, where precision and adaptation to variations are crucial.
The practical impact of these intelligent systems is evident in their ability to manage complex welding tasks with minimal intervention. For instance, hard automation systems and intelligent power sources in large-scale industrial settings contribute to high-quality welding, enhancing productivity and reducing defects. Saha concludes, “The evolution of intelligent welding systems represents a major leap forward, addressing the multifaceted challenges of modern manufacturing.”
Emerging trends in fibre laser welding
Fiber laser welding is rapidly gaining prominence due to its speed, precision, and versatility. Amrityoga Mishra of Great-Yuva Welding Expert highlights the transformative impact of this technology, particularly in the automotive sector. “Fiber laser welding is not just a trend; it’s becoming a cornerstone of modern manufacturing,” Mishra notes. The technique’s ability to perform high-speed, high-precision welds makes it an attractive option, surpassing traditional efficiency and design flexibility methods.
Mishra emphasises the advantages of fibre laser welding, including its speed up to seven times faster than traditional methods. This efficiency is achieved through a single-sided welding process that eliminates the need for double-sided pressing. Moreover, fibre laser welding offers significant design freedom, reducing the need for additional supports and components. As Mishra elaborates, “The ability to achieve deep, precise welds with minimal heat-affected zones makes fibre laser welding ideal for industries demanding high-quality and complex joints.”
Keyhole welding, a technique within fibre laser welding, further exemplifies the technology’s precision. With power densities significantly higher than traditional methods, keyhole welding enables deep penetration and high-quality welds with reduced thermal distortion. As Mishra predicts, “The continued advancement of fibre laser welding will drive further innovation and adoption, leading the future of welding practices.”
Innovation in robotic welding technology
Integrating robotics into welding technology is reshaping the industry, offering enhanced productivity, precision, and efficiency. Anoop Singhal from CRP Robot Technology emphasises the versatility of modern robotic systems. “Today’s robotic welding solutions are designed to handle a wide range of tasks, from delicate operations to heavy-duty applications,” Singhal explains. With capabilities ranging from 3 kg to 210 kg payloads and reach options from 600 mm to 3.5 meters, these robots cater to various welding techniques, including MIG, TIG, and laser cutting.
Advanced sensors and software further enhance the precision of robotic welding. Laser sensors, seam trackers, and arc sensors ensure high accuracy, while offline simulation software allows for meticulous planning and programming of welding tasks. Singhal notes, “The integration of these technologies streamlines operations and reduces setup times, leading to more efficient and accurate welding processes.”
Collaborative robots (COBOTS) represent another significant advancement. Designed to work alongside human operators, COBOTS enhance safety and flexibility. Singhal highlights their user-friendly design and intuitive programming, improving welding operations’ productivity and safety. “COBOTS are a game-changer, offering a blend of automation and human collaboration that boosts overall efficiency,” Singhal asserts.
Automation and advanced material handling in plate-cutting
The plate-cutting industry is undergoing a significant transformation with the shift towards automation. Duraiswamy Ravichandran from Messer Cutting System India Pvt. Ltd emphasises the benefits of automation in enhancing productivity, reducing costs, and improving safety. “Automation addresses inefficiencies in traditional manual methods, leading to streamlined processes and higher operational efficiency,” Ravichandran explains.
Automation systems offer numerous advantages, including increased productivity and improved safety. By handling materials more efficiently, automation reduces operation times and lowers costs. Advanced systems, such as vertical storage towers and automated retrieval units, optimise material handling and reduce manual intervention. Ravichandran highlights practical applications, such as a facility that achieved a 30 percent increase in productivity and a 25% reduction in labour costs through automation.
Furthermore, automation improves product quality by ensuring precise and consistent cutting, minimising errors, and reducing material wastage. Ravichandran concludes, “Embracing automation in plate-cutting enhances efficiency and supports sustainability by optimising resource utilisation and reducing waste.”
Embracing a sustainable future
As the industry advances, addressing environmental impact remains a critical focus. Rituraj Bose, Honorary Secretary General of IIW-India, underscores the importance of adopting green welding practices. “Despite technological advancements, the environmental impact of welding is a pressing issue that needs to be tackled,” Bose states. Welding processes release pollutants that contribute to global warming and pose health risks, making adopting greener techniques essential.
Green welding practices, such as solid-state welding methods, offer significant environmental benefits. Techniques like friction stir welding generate less pollution and energy consumption than traditional methods. Bose explains, “Friction stir welding is highly energy-efficient and produces no smoke or noise, making it a cleaner alternative.” Additionally, arc welding techniques like submerged arc welding (SAW) offer reduced emissions, although they are limited to specific applications.
Using virtual reality (VR) simulators in training represents another step towards sustainability. By reducing the consumption of materials during initial training stages, VR simulators help minimise waste and lower costs. Bose advocates for the broader adoption of these tools, stating, “Investing in VR simulators and greener welding techniques will reduce environmental impact and enhance worker safety.”
Bridging gaps and driving innovation
Collaboration among industry stakeholders is crucial for driving innovation and improving welding practices. Duraiswamy Ravichandran underscores the value of close cooperation between OEMs and integrators. He notes, “The best ideas come when integrators and source suppliers work closely together,” highlighting how collaborative efforts can lead to superior outcomes in manufacturing.
Anoop Singhal echoes this sentiment, emphasising the need for more industry sessions to facilitate knowledge exchange. He points out, “There is still a significant gap in information sharing within the cutting and welding sector,” suggesting that more frequent interactions are essential for driving the industry forward. Industry associations and media professionals play a vital role in fostering these connections and aligning educational outcomes with industry needs.
Aligning education with industry demands
The welding industry faces challenges in aligning educational training with actual industry needs. Amrityoga Mishra stresses the importance of frequent interaction between industry associations and educational institutions to bridge this gap. He suggests that “frequent interaction and seminars are required to align educational outcomes with industry demands,” emphasising the need for updated training programmes that reflect current industry practices.
Investing in skilling and training is crucial for addressing the shortage of skilled welders and ensuring the workforce is equipped to handle emerging technologies and practices. By aligning education with industry requirements, the welding sector can build a more capable and adaptable workforce ready to meet the demands of modern manufacturing.
Conclusion
Intelligent welding systems, fibre laser welding, and robotic technologies are reshaping the field, offering new solutions to longstanding challenges. Embracing green practices and investing in skilling and training further contribute to the industry’s evolution. As the sector advances, collaboration and strategic planning will be key to achieving greater efficiency, quality, and sustainability in welding practices.
Cookie Consent
We use cookies to personalize your experience. By continuing to visit this website you agree to our Terms & Conditions, Privacy Policy and Cookie Policy.