IoT-enabled systems improve welding precision and compliance
By Staff Report | October 24, 2024 3:49 pm SHARE
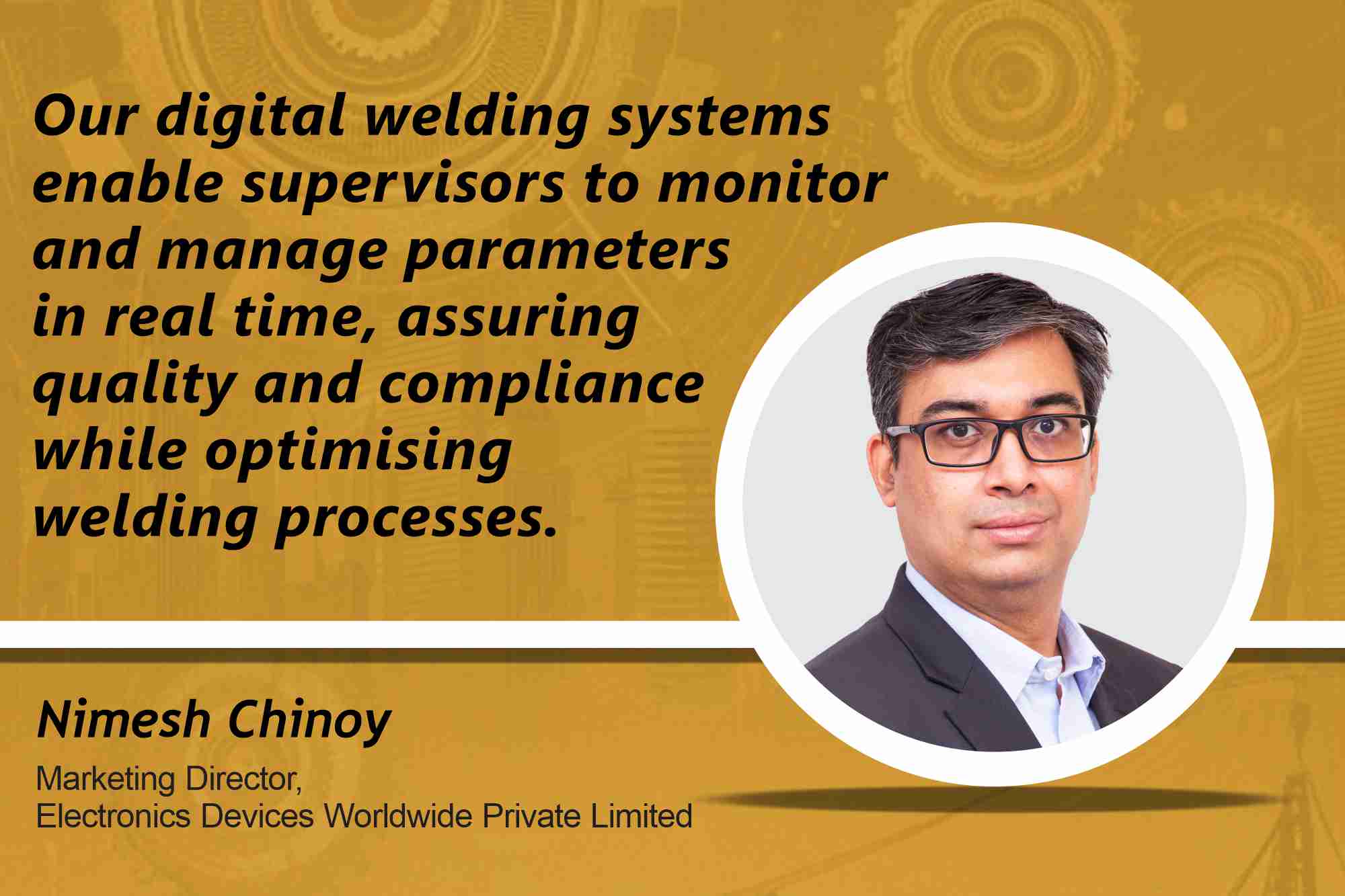
Innovative welding and cutting technologies are altering infrastructure construction by increasing resilience and sustainability while improving efficiency and performance, ultimately changing how we build and maintain critical structures.
How are advancements in welding and cutting enhancing the resilience and durability of infrastructure projects?
Welding has always been a balance of productivity and quality. In infrastructure projects, the design must survive worst-case situations in load carrying and natural disaster resilience (earthquakes, heavy rains, etc.). The appropriate material selection and defect-free welding help you attain these milestones faster. Because infrastructure projects require significant onsite building and fabrication, ARC Welding (SMAW) was preferred. With advancements in power sources and digital inverters, it is now possible to weld using flux-cored wires (FCAW), self-shielded wires, and metal-core wires, which improves weld speed and quality. The Thin Wire SAW method with 600 Amps and 1000 Amps CC/CV welding power sources has also increased productivity for thinner materials (5mm to 15mm) while maintaining excellent weld quality standards.
How do innovative materials enhance the longevity and performance of products in large-scale infrastructure projects?
The longevity and performance of our products (SigmaWeld, welding power sources, and Induction Heaters) onsite are heavily influenced by their IP rating and lightweight. With modern Silicon Carbide Semiconductors and IGBTs, achieving lower losses at greater switching frequencies is feasible, allowing the equipment to be more compact and lightweight. This also enables our Pro Series inverters to be IP23 rated, which means they can endure severe site conditions while maintaining 100 percent quality and duty cycle performance. There are additional newer components, and our research and development team works tirelessly to guarantee that the goods we make and design are ahead of the curve. We have over six patents for creative goods that we designed.
Can you describe any recent projects where your products improved the infrastructure’s ability to withstand environmental or operational stresses?
Recently, we were tasked with fixing a leaking pipe at a key position. This power plant project is of tremendous national importance and has been on hold for a long time. We were to design the automation and welding approach to cut the inaccessible current pipe, edge prep it, install a new pipe, align it, and weld it correctly the first time. It was a radiography joint, and the entire procedure was to be performed remotely and autonomously. This was a vital issue, and we successfully designed, developed, and executed the weld joint in under six months. The project has been completed, and we are pleased to report that the power plant has subsequently begun and become essential.
How are your solutions integrating with smart technologies or digital systems to optimise performance and maintenance in infrastructure applications?
Our new welding systems (SigmaWeld) are entirely digital and have built-in IOT. These systems are linked via GSM to our cloud server or a fixed site at the customer’s premises. This aids in monitoring the welding parameters of each machine for each weld joint and each welder connected to the system. Welding supervisors can also assign welding parameters (WPS) to specific welders, which are loaded onto the welder’s ID CARD (RFID or NFC). When the welder approaches any welding machine on the station and swipes his card to start the machine, the parameter (WPS) is transferred to the machine. The welding equipment will only operate within these restrictions for the day or until another card is swiped.
We also have a version of DMS that can be attached to any welding machine and record critical welding characteristics such as welding current, welding voltage, and arc in real time and against a time stamp. This helps determine whether the welder followed the WPS or departed from it. This is also highly useful and extensively used for welder certification and WPS establishment. Many of our clients have employed these for similar purposes at other infrastructure sites, particularly in cross-country pipelines with relatively distant locations.
What are the key challenges in ensuring your products meet the evolving sustainability and environmental impact standards?
Sustainability and environmental impact must be examined in many ways. How can we positively affect the environment by using less and generating more? The majority of our products conserve energy (up to 40 percent more than typical thyristors or transformer-based welding equipment).
When building our SigmaWeld Accelerated Tig solution, we accepted the task of going above and beyond to provide the lowest possible environmental effect. This solution welds 30 times faster, does not require edge preparation (saving energy, time, and material), and does not require filler material when welding up to 10 mm (consumable saved, resulting in lower consumption, processing, and mining of minerals), uses 70 percent less gas (argon or argon hydrogen mixture), saves 80 percent on power during welding, and reduces overall welding costs by more than 75 percent. All this is done while welding important materials like stainless steel (used in manufacturing food, pharmaceutical, and chemical equipment), titanium, hesta-alloys, and other critical materials.
How do you balance cost and performance when developing new solutions for critical infrastructure components?
We must assess the value we provide to help our consumers save time, money, and resources. Cost and performance must be determined by the customer’s application and its requirements. Provide easy solutions that can help enhance quality and performance while saving overall costs for the end consumer. In any industry, value can only be realised when cost and performance are balanced for the client.
How are your products or technologies addressing the needs of rapidly urbanising environments and ageing infrastructure?
Rapid urbanisation necessitates the use of primarily pre-engineered buildings. We assist our customers in migrating from SMAW to Flux Cored and Thin Wire SAW for better productivity and higher welding quality. These solutions are semi-automated, sometimes entirely automatic, with reduced reliance on expert labour.
We assist our customers in infrastructure, such as power plant erection and commissioning, using induction heating solutions for pre- and post-weld heat treatment applications. These incredibly efficient devices allow faster and more direct temperature control in the joint. This helps to save expenditures in terms of power and time. We heated a shell’s 150mm thick long seam for one client without heating the surrounding area. This made the welder more comfortable (because the working temperature was ambient for him rather than 60 or 70 degrees Celsius). As a result, he produced nearly twice as many weld passes while maintaining strict welding standards.
Newer materials and welding with the proper settings can increase resilience and significantly impact infrastructure life.
For more information, visit: https://electronicsdevices.com/
Cookie Consent
We use cookies to personalize your experience. By continuing to visit this website you agree to our Terms & Conditions, Privacy Policy and Cookie Policy.