Konecranes makes maintenance easy with RopeQ
By Edit Team | November 21, 2014 7:01 am SHARE
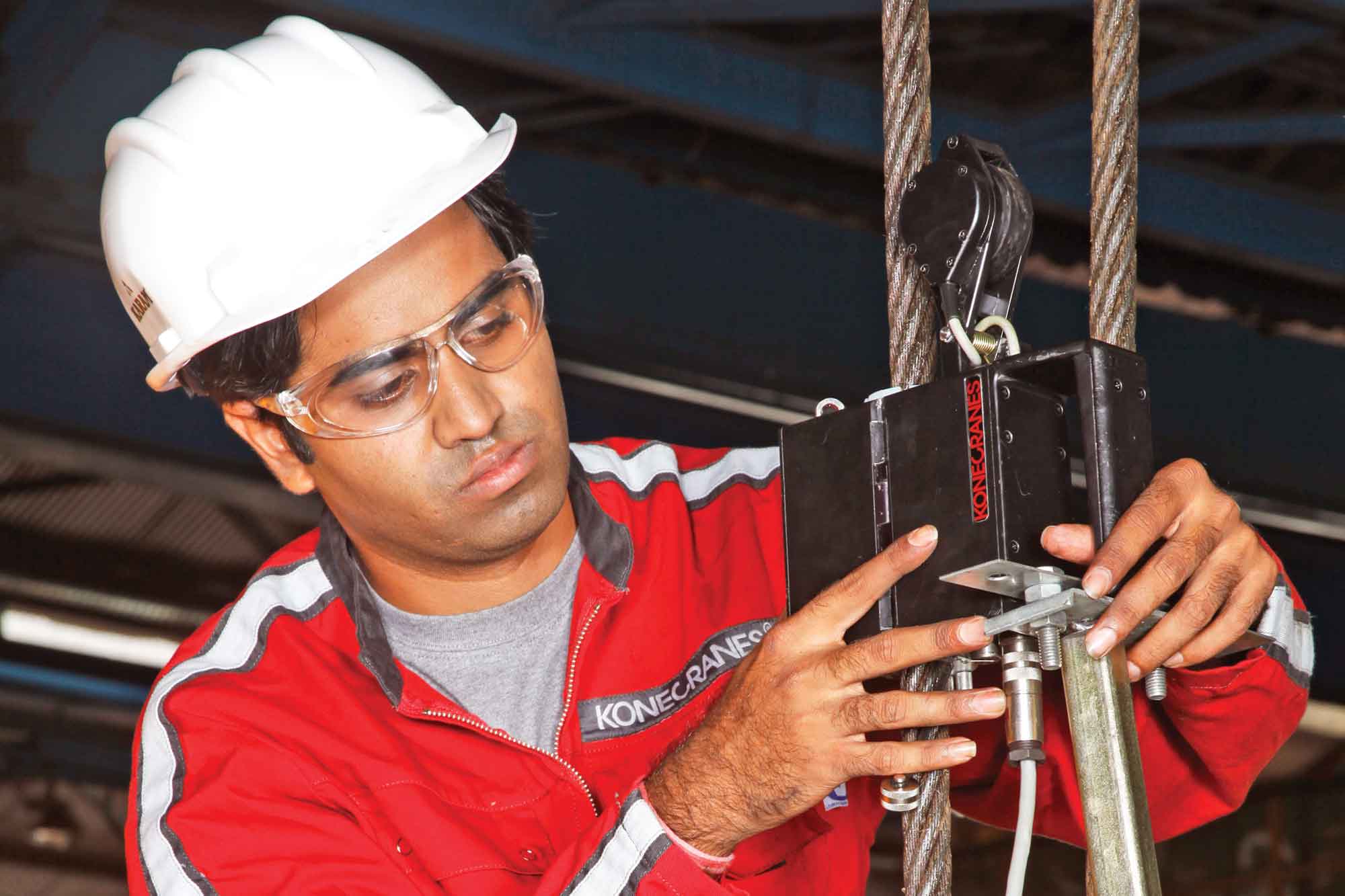
Konecranes, one of the global leaders in lifting industry, has developed RopeQ, a reliable and practical system that evaluates the working condition of wire ropes using advanced, Non-Destructive Testing (NDT) methods.
RopeQ is a diagnostic tool that uses electromagnetic technology to assess the inner and outer wires and strands of a wire rope. This testing method achieves reliable, accurate, and repetitive inspection results that ensure safe use and improve total lifecycle cost.
Wire rope contains up to 400 individual wires. Throughout a wire rope’s working life, the wires are subject to bending and abrasion wear. If too many of these wires are broken, the safety of the rope cannot be guaranteed. Usually only the outer surface of a wire rope is checked during a visual inspection. It is impossible to inspect the inner core using standard methods of inspection. For this reason many wire ropes are classified as safe even when they should be discarded because of heavy internal damage.
Backed by more than 60 years of experience and research in the design and maintenance of hoisting equipment, Konecranes has developed this technology called RopeQ. It applies an electromagnetic-inductive testing method to detect flaws that are not visible on the surface of wire ropes, producing an accurate assessment that can increase safety and reduce wire rope cost.
The RopeQ diagnostic tool fastens to wire rope assemblies and records a series of interior images along the entire length of the wire rope. The diagnostic survey produces data that pinpoints all areas and degrees of degradation. The precise results help to determine whether continued use is safe or whether the rope needs to be changed.
In addition, RopeQ can improve the total lifecycle costs of equipment by optimising wire rope change intervals in process duty and critical equipment. Throughout the working life of a wire rope, the strands and core are subjected to tension, bending, and abrasion, which can compromise strength and safety. Routine maintenance often relies on pre-determined replacement intervals regardless of the actual condition of the wire ropes, meaning that safe and operable ropes might be replaced too often or too soon, resulting in unnecessary downtime and costs.
RopeQ produces verifiable condition assessments that can be compared against discard criteria, reducing the possibility of changing wire ropes that are still compliant with lifting regulations. Most importantly, RopeQ is able to detect faults that are not visible to the naked eye, thus improving the overall safety of the lifting equipment.
Benefits of RopeQ
• Improved safety from detecting non-visible defects
• Optimised wire rope change interval
• Repeatable and reliable results
• A report that is easy to read and interpret completed with recommendations for action.
Applications
RopeQ is appropriate for a wide range of applications, including steel mills, paper mills, steel service centres, foundries, waste-to-energy plants, pulp mills, chemical plants, power stations, nuclear power plants, aerospace and general manufacturing.
It is suitable for any wire rope application and is particularly useful in the following as well:
• process cranes in constant use
• cranes that are used only occasionally
• ropes that are particularly hard to inspect visually
• post-accident inspections.
Cookie Consent
We use cookies to personalize your experience. By continuing to visit this website you agree to our Terms & Conditions, Privacy Policy and Cookie Policy.