Machine owners are now looking for intelligent machines
By Edit Team | May 8, 2021 5:57 pm SHARE
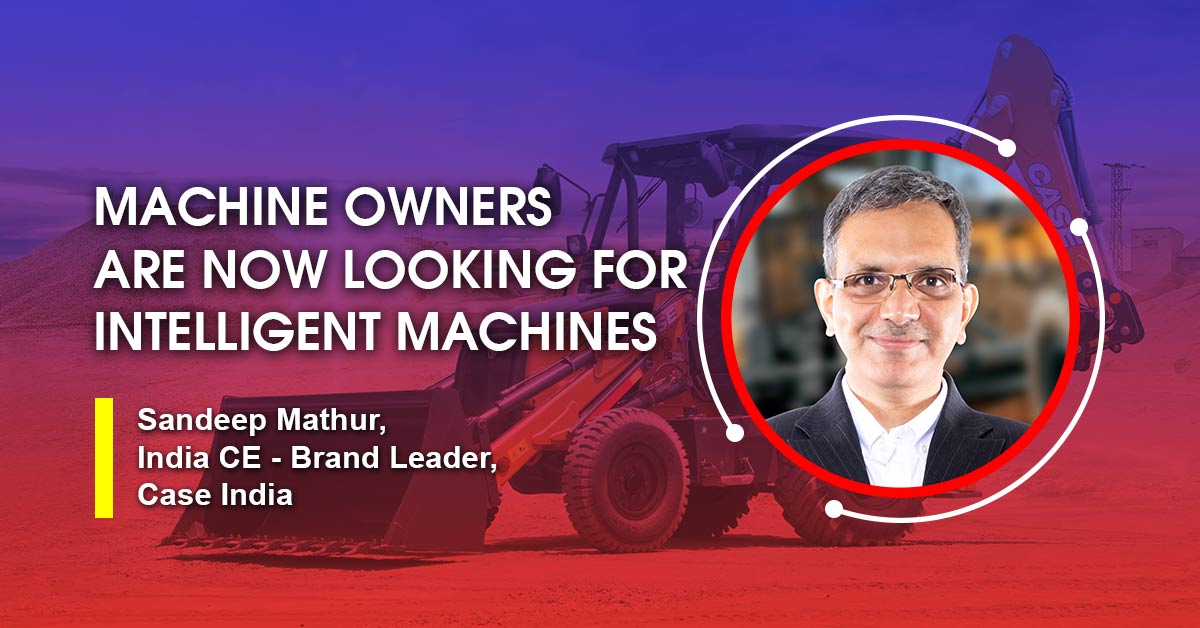
Case Care is a cost-effective service contract under which we proactively monitor the machine which helps in preventive maintenance, says Sandeep Mathur, India CE – Brand Leader, Case India.
What is the role of maintenance in the upkeep of construction equipment?
Construction equipment is designed and built to be used in challenging environments. From construction of roads and canals to usage in mining and quarrying, equipment is prone to extensive wear and tear over extended periods of time and usage. Challenging projects usually have short deadlines or high production requirements to meet, as a result of which the machines are used extensively. Construction and mining equipment encounter rough terrains, rocky underfoot conditions, greatly varying temperatures and humidity, and long working hours. These factors take a toll on the equipment and without timely maintenance, can wear the machine components. For example, backhoe loaders and excavators, especially those working in stone quarries, have to handle and load stone rubble, and as a result, normal buckets and tyres wear out faster. Similarly, motor graders that work on levelling different layers of roads, usually traverse hard or rocky surfaces.
At Case, our equipment is made of sturdy and durable components, ensuring the efficiency in the toughest of terrains and climates. Our machines have optional heavy duty components buckets, blades and tyres that ensure the longevity of these components that are especially prone to wear. Case India’s equipment ensures lower cost of ownership and comes with longer service intervals as well. We also provide quick solutions through our after-sales service spread across 200 touchpoints to ensure that the customer gets service even in remote locations. At Case, we believe in taking on real challenges and so do our products.
What are the maintenance practices followed for the upkeep of construction equipment?
It’s important to take proper care of construction equipment in order to prolong its efficiency and productivity. Customers and operators need to have adequate knowledge on the working of the equipment to reduce the chances of any malfunction. Adopting a disciplined regimen of proper lubrication and maintenance for all the components is essential along with regular cleaning after a day’s work.
At Case, we care about our customers and their business as well. So, to decrease downtime and increase productivity for our customers, we have a dedicated aftermarket team which provides quality parts and services. Case offers optional extended warranties and service support, so customers can use their machines more confidently knowing that CASE will support them through the machine’s lifecycle. Case Care is a cost-effective service contract under which we pro-actively monitor the machine which helps in preventive maintenance. Case Protect is a comprehensive extended warranty which ensures expert care, roundthe-clock availability and hassle-free operations.
For fleet owners, Case offers maintenance contracts with dedicated service manpower available at site to ensure uptime. In terms of spare parts and product support, we have a good amount of stock supplies at key locations and even in these challenging times we are delivering parts and scheduling services via our comprehensive dealer network, keeping all the safety precautions in mind. Case Site-watch is also monitored by Case After Market team, to ensure that timely action can be taken in case of any potential disruption in working. Our customers are aware that Case guarantees peace of mind and can vouch for our commitment to their business and the fact that we’re always ready to go the extra mile for them.
How is predictive maintenance gaining importance in construction equipment and plants?
As the category evolves, so do its customers. Machine owners these days are looking for intelligent machines which deliver efficiency on all parameters during their work and after. With predictive maintenance, customers can reduce downtime, save any additional repair cost, keep the machine up to date and maintain its performance and delivery. In a category where machines face heavy wear and tear, predictive maintenance is of paramount importance.
What is the role of digital technology in plant/equipment operation and maintenance?
Technological upgrades have been a perennial part of the CE industry and Case has always been a technology first brand. Our products come equipped with the renowned Eagle-EyeTelematics technology which helps in enhancing the performance and efficiency of the machine. This technology notifies the user through alerts about the machine’s service intervals, usage, productivity, spare part requirements and can also plan services and replacements in advance. This means lower down times and increased productivity for the customer.
Additionally, we recently launched a Sitewatch technology platform which helps give an all-new dashboard, more intuitive navigation and new overview sections that spotlight critical information without requiring the user to search extensively for the data. It also gives an easy dropdown menu, makes critical reports on factors such as equipment utilisation, fuel consumption and maintenance, all at the click of a button.
What is the importance of skill development in machine operation and maintenance? How will this help improve the machine uptime?
Operator training is paramount to ensure that the best features of the machine are used and the benefits reaped. To an extent, every machine is only as good as its operator. Lack of training also means that operators may overwork a machine beyond its capability resulting in downtimes due to frequent service requirements. Case has a fleet of trained operators and we are working on establishing a training program to train more – to try and reduce the impact of this challenge.
At Case, we design equipment and processes keeping our people and their surroundings in mind. We try our best to create products with a simple and easy-to-use interface and to further ease the process, we host training programs all around the year and deploy some of our well-trained officers on site to help users with regular training, ground check and maintenance. We believe in incorporating practices that enable people and will continue to do so.
Cookie Consent
We use cookies to personalize your experience. By continuing to visit this website you agree to our Terms & Conditions, Privacy Policy and Cookie Policy.