MB Crusher revolutionises shafts screeners
By Edit Team | May 16, 2019 11:11 am SHARE
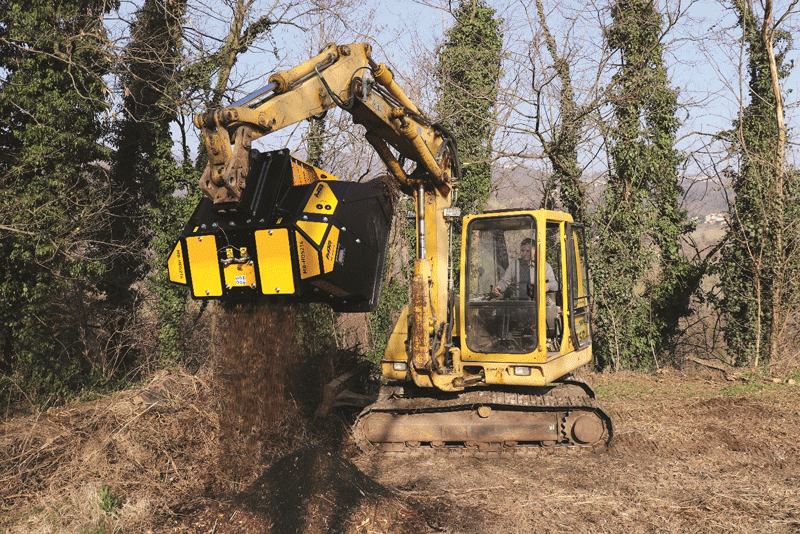
MB Crusher has announced launch of the new generation of Shafts Screeners, which were also introduced in Bauma 2019 in Germany. From the creators of the world’s first patented multi-functional jaw crusher, comes the innovative MB-HDS series – a true revolution beneficial to all users.
“The new MB-HDS series can adapt to a range of different working environments and can select different types of materials with unprecedented simplicity and speed, without the need for a specialist or special training,” says Diego Azzolin, Production Director at MB Crusher.
What is new about the MB-HDS Shafts Screener is its ability to adapt to different types of work and different materials. It is a solution for processing different kind of waste rubble, which can quickly be turned into re-usable and profitable material.
“We have created a machine which, alone, is capable of overcoming the various challenges faced every day by those involved in earth removal, excavation, demolition, recycling, agricultural activities and landscaping. The new MB-HDS series selects and crushes excavation and demolition materials, asphalt, coal, organic materials, wood, bark and light plastics, also it enables products to be re-purposed immediately. It is possible to transform one material into another effortlessly any time you need to.
The screening bucket is available in four models with shafts suitable for the different material selection requirements and, as with all MB Crusher machines, they can be easily installed on excavators, diggers, mini diggers and loaders (from 5 to 35 tonnes) in order to easily access and move around work sites, construction sites, areas containing large pipelines, towns or remote agricultural areas. Changing of the rotary shafts can be carried out anywhere, they have a centralised greasing system and all maintenance tools are located inside a compartment of the shafts screener. However, these are not the only innovations, because the new generation MB-HDS also takes care of the machine on which it is installed. An engineered automated shock-absorbing hydraulic system reduces the discharge so that the engine, transmission components and the machine boom do not suffer any damage. Preserving machinery life expectancy and reducing maintenance costs.
For more information,
visit: www.mbcrusher.com
Cookie Consent
We use cookies to personalize your experience. By continuing to visit this website you agree to our Terms & Conditions, Privacy Policy and Cookie Policy.