Meeting aggregate requirements amidst pandemic
By Edit Team | September 22, 2021 11:46 am SHARE
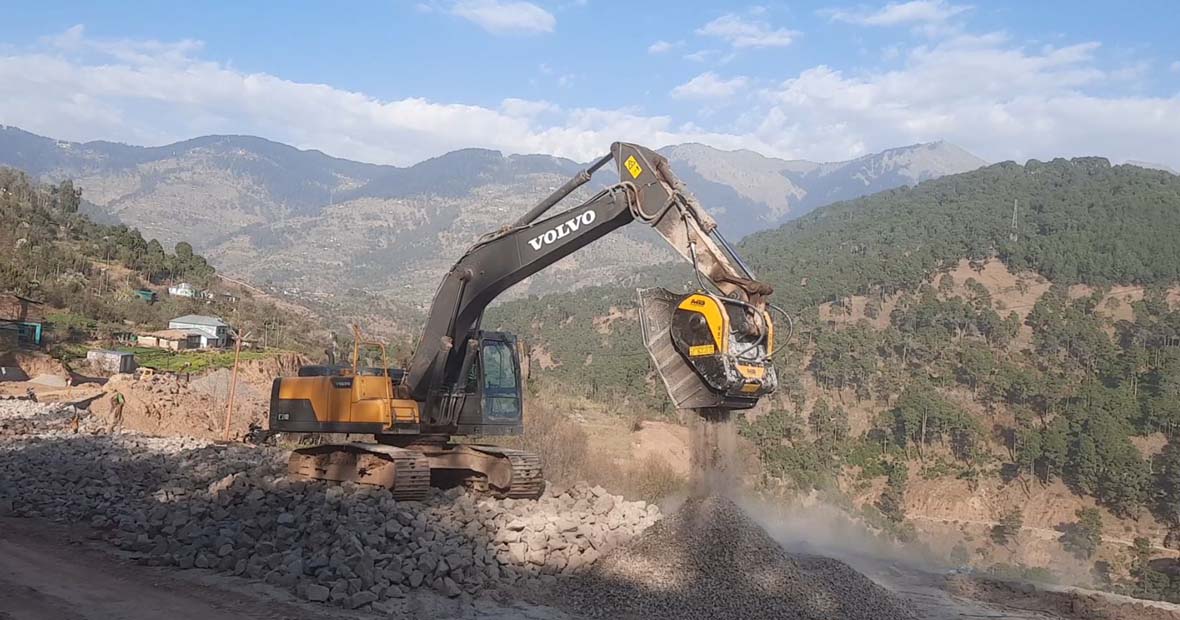
A mid-size A1 class road contractor from the northern part of India, with an annual turnover of more than `2,000 crores, was undertaking a road construction project of approximately 100 km with complexities related to tunnel work, integrated railway project and other factors.
At the beginning of the project, they were purchasing aggregates from a crusher site, which was 40 km away from their project site.
They were procuring aggregates, such as GSB (63 mm down) and WMM (40 mm down) bearing significant transportation costs on top of the material cost. Furthermore, with the lockdown in place, they were unable to be independent at site for their crushing requirements as manual labour was unavailable and/ or not consistently reliable.
Taking a step back to the project, the site had availability of river stone and hill rock thanks to hill cutting for the road project; it also had the requisite permission from the authorities to re-use the material for the road project.
But still, they were procuring inconsistent quantities from the crusher site, and at this point the Project Manager started looking for an alternative solution which would not only help him achieve consistent output, but also enhance the economic viability.
The solution was found by looking up to MB Crusher units: specifically, the model chosen was the MB Crusher bucket BF90.3 to crush river bed material and hill rock on the same excavator that was already deployed at site for other purposes.
By this way, they transformed their excavator into a crushing unit capable of producing all of their GSB and WMM requirements independently at site.
The result was outstanding as in just one move they completely eliminated their dependability on the crusher site, reduced the cost of aggregates and saved on transportation cost.
With the use of the MB Crusher bucket BF90.3, they are now achieving the productivity of approximately 800 CFT per hour with savings of more than `12 per CFT compared to their previous set up.
The jaw crusher BF90.3 is the first crusher bucket produced and patented in 2001, therefore the real flagship of the MB Crusher line of jaw crushers. Applicable to excavators of any brand starting from 21 tons, it has been improved and strengthened over the years, to keep the performance level with any type of material and application.
Cookie Consent
We use cookies to personalize your experience. By continuing to visit this website you agree to our Terms & Conditions, Privacy Policy and Cookie Policy.