Mines of the future
By Edit Team | April 14, 2018 7:24 am SHARE
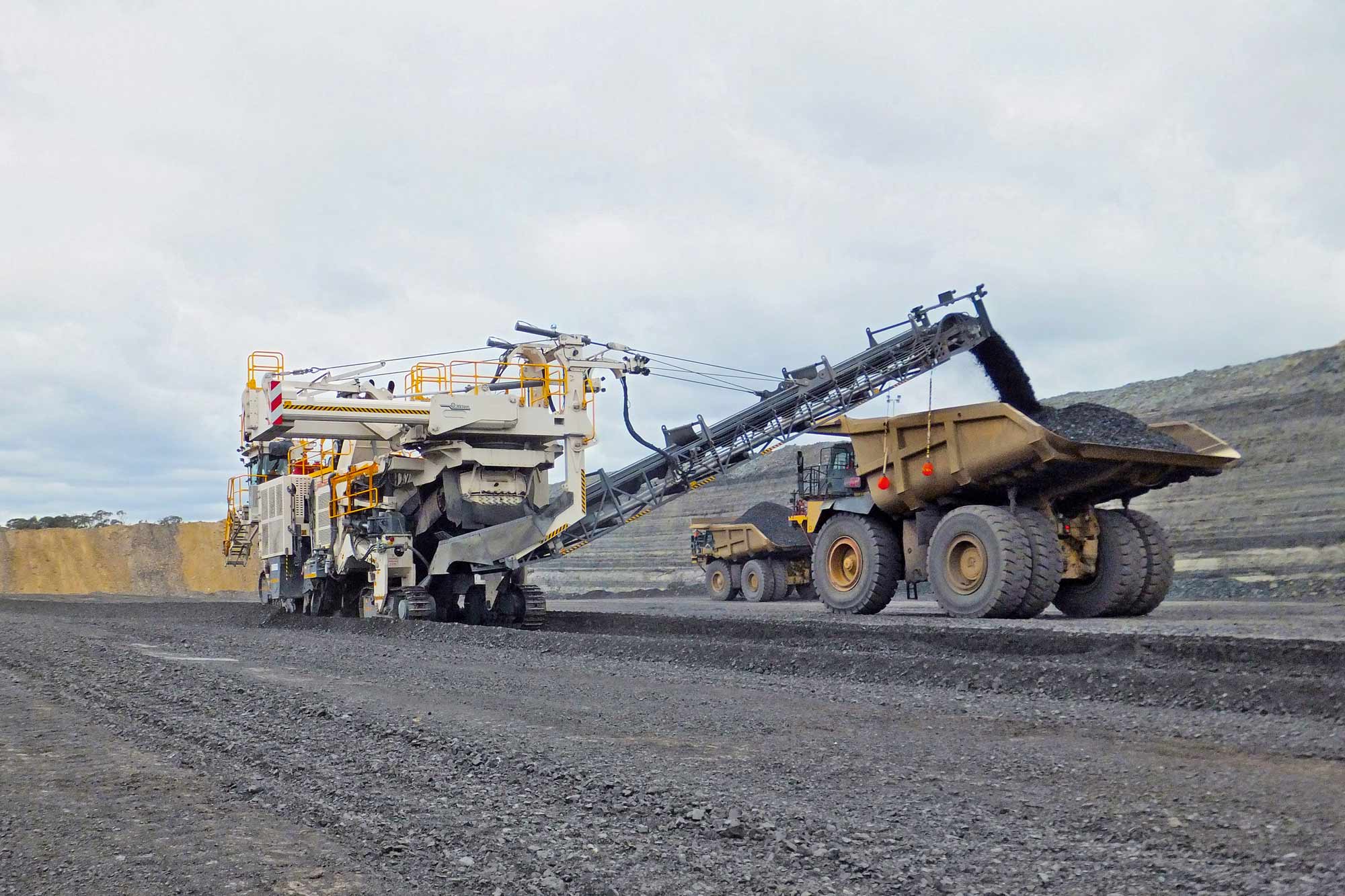
An exclusive report on why it is necessary to embrace advanced technologies for mines of the future.
Mining industry plays a significant role in any country’s industrial growth. Indian mining industry, contributed about 3 per cent of the GDP in 1990s and currently contributes 2 per cent of the GDP. While exploring on huge potential in Indian mining there are certain challenges that are faced by mining industry due which growth rate is not visible currently.
Apart from socio-economic, cultural and statutory issues, current major technical challenges faced by Indian mining industry are: Productivity improvement, capital project execution and ROI, infrastructure access, competitive land usage, and faster adoption to technological changes. It is the need of the hour for mining industry to focus on these challenges and covert the same to opportunities.
The use of good management operating systems combined with new-age technologies could be the answer to today’s mining challenges, believes Manoj Kumar, Assistant Vice President – PMG (Product Management Group), Bevcon Wayors. He adds, “As major mining operators in India are state-owned, government must realise the importance of the new technologies and encourage the vendors to get the benefits faster and better.”
He feels that continuous exploration of mining embracing the new age technologies will keep up Indian mining industry on target set growth path.
Mining has changed
Over the years, technology has been responsible for dramatically changing how mines are operated today. Today, our decisions are driven by Big Data. We can speak with more certainty and make more informed choices because technology is able to provide us with incredibly accurate measurements and information. “We depend on innovation to drive our industry forward. Remote control centres are removing workers from the face. Big Data and analytics are allowing us to monitor machine performance to schedule maintenance and reduce downtime. Autonomous trucks are helping sites stay safer and more productive. These amazing tools are revolutionising the way we do things and we have only begun to scratch the surface of their capabilities,” explains Soumitra Mukherjee, Dy. Director – Marketing, Komatsu Mining Corp.
Mining industry in constantly pushing towards improving efficiency, reducing costs and increasing safety. Samaresh Mitra, National Sales Head – OE, Komatsu Mining Corp. adds, “The keys to maximising returns in our industry lie in adopting new techniques and technologies. Automating mining operations will make the entire process leaner resulting in higher productivity, lower costs and less waste.”
Hemant Dahale, Managing Director, Hectronic India is also of the opinion that the ease with which mining is handled in any part of the world compared to probably few decades ago has periodically changed for the betterment. He added, “Majority of the credits go to the technical innovation which is surfaced on a constant basis to boon various activities which comprise a mining project. The soul reason behind the effort of such innovations are to approach a system that is efficient, fool proof, quick and transparent. It is quite important to imbibe such advances since in this modern era with all technologies synergising with one other on a larger scale, one will be left out of the race if he/she fails to do so.”
A process of transition and transformation
Mining remains relevant and valuable in today’s Indian economy. However, Shantanu Banerjee, Country Head, Hazemag India believes, “Modernisation is not simply mechanisation and/or gradual implementation of new technology. It is a process of transition and transformation of the mining industry of yesteryear and today to that of tomorrow.”
Chiranjit Banik, Dy. Manager – Marketing, Hazemag India observes that present day miners have started programs to eliminate the high fuel usage, labour and safety cost associated with trucks and shovel mining to increase mass material movement efficiency for better profitability.
To achieve the above requirement Hazemag offers solutions of mobile or semi-mobile crushers and screens which can be a game changer for an operator. The range encompasses feeder breaker, sizers, roll crushers, hammer mills, impact roll crushers, roller screens, apron feeders, chain conveyors for offering the optimum solution.
Careful selection of any one or combination of some of the above equipment can reduce fuel cost by 60-80 per cent, reduce emission, reduce moving objects resulting into higher safety standards and low cost of operation, claims Banik.
For example, an in pit crushing of overburden, conveying the same through conveyors and spreading through suitable spreaders can significantly reduce cost of trucking and help in consolidation of overburden dump reducing possibility of any slope failure.
Technology makes economic sense
The mining industry is not immune and has undergone rapid change during the past decade. The mines and miners of tomorrow will look and operate very differently to the industry as we know it today. Technology is bringing undreamed of innovation and possibility to the field while society’s expectations of miners are changing too. While mineralisation, logistics, capital, skills, technology, and regulation are all essential ingredients for any mine; it is the people who will manage, plan, mine and refine the ore that makes the industry possible.
According to Mukaya Simubali, Executive Director, AAC Mining Executors Group, “Mines of the future would focus on digital mining, Big Data analysis, knowledge production and mining mechanisation. Technology makes economic sense for ore mining.”
Automated mining involves the removal of human labour from the mining process. The mining industry is in the transition towards automation. Automated mining is an umbrella term that refers to two types of technology. The first type of mining automation deals with process and software automation; the second type deals with applying robotic technology to mining vehicles and equipment. Mukaya lists advanced solutions in this context:
Mine automation software
In order to gain more control over their operations, mining companies may implement mining automation software or processes. Reports generated by mine automation software allow administrators to identify productivity bottlenecks, increase accountability, and better understand the return on investment.
Mining equipment automation
Full automation can refer to the autonomous control of one or more mining vehicles. Robotic components manage all critical vehicle functions including ignition, steering, transmission, acceleration, braking, and implement control (i.e. blade control, dump bed control, excavator bucket and boom, etc.) without the need for operator intervention. Fully autonomous mining systems experience the most productivity gains as software controls one or more mining vehicles allowing operators to take on the role of mining facilitators, troubleshooting errors, and monitoring efficiency.
Explaining the benefits of automation, Mukaya said, “The benefits of mining equipment automation technologies are varied but may include: improved safety, better fuel efficiency, increased productivity, reduced unscheduled maintenance, improved working conditions, better vehicle utilisation, and reduced driver fatigue and attrition.”
A few advanced solutions for tomorrow’s mines
Wirtgen SM 2200: A versatile surface miner
WIRTGEN is one of the global market leaders in the manufacturing of machines for cutting rock in opencast mining operations. WIRTGEN surface miners cut primary resources such as coal, gypsum, iron ore, salt, phosphate, bauxite, limestone or granite, achieving high degrees of purity in the process. They are increasingly used as primary extraction equipment also in newly opened-up opencast mines or extensions of existing opencast mine operations.
Commenting on the WIRTGEN’s most advanced offering for tomorrow’s mines, Ramesh Palagiri, Managing Director and CEO, Wirtgen India said, “We not only develop innovative machines of the highest quality. With our machine technology, we also constantly endeavour to keep environmental pollution as low as possible. A WIRTGEN surface miner is a perfect example of this philosophy: it impresses with its environmentally friendly technology as it cuts, crushes and loads rock in a single operation.”
A tremendous advantage of selective mining is that the vibration-less mining operation without drilling and blasting is accompanied by low levels of dust and noise. The low environmental impact also permits maximum exploitation of the deposit right up to the edge of residential areas. The selective mining of high-quality materials requires considerably less space than conventional mining methods. WIRTGEN’s fuel-efficient, intelligently controlled engines comply with the strictest exhaust emission standards.
• WIRTGEN Surface Miners reduce four operating steps to one.
• State-of-the-art engine technology reduces exhaust and noise emissions.
• Anti-vibration engine support reduces vibration and noise emissions.
• State-of-the-art machine reduces exhaust and noise emissions.
• Soundproofing reduces noise emissions.
WIRTGEN offers advanced machines for cutting widths from 2.2 metres to 4.2 metres. Wirtgen SM 2200 offers raw material extraction in small and medium-sized mining operations. This is a versatile surface miner for the selective mining of raw materials with an unconfined compressive strength of up to 50 MPa or for routing operations and infrastructure projects. The 2.2-metre cutting drum unit – tailored precisely to the specified application – with a cutting depth of up to 300 mm guarantees high production rates at minimum tool wear. “Trucks with a load capacity of between 20 and 60 tonnes can be loaded using the powerful liftable and slewable front-loading conveyor,” informs Palagiri.
Bevcon’s Sandwich Belt High Angle Conveying
The mining industry is extremely capital-intensive, especially when implementing bigger equipment with larger capacities to increase production rate. However, low commodity prices have forced companies to discover innovative methods and equipment to decrease their overall capital costs by improving equipment productivity. One way to accomplish this is to utilise equipment more effectively and efficiently.
Conventional way of bringing ore is either through conventional belt conveyors, rail track or hauls trucks. This requires for the preparation of a lengthy path both in underground and open cast mines. These conventional carrying equipment have limitations in terms of carrying capacities and space restrictions.
The innovative and new age method of bringing ore to the surface is by continuous vertical Haulage. Bevcon Wayors has its collaboration with Dos Santos International – USA.
A high angle conveying system is an economic and energy saving alternative, with the capability of achieving very high, steep angle lifts and capacities up to 10,000 TPH. Standard locally available components and conventional belts are used. According to Bevcon, these new and innovative equipment adds greater value to the production.
Hazemag’s a simplified crushing and conveying solution
Several projects worldwide in the feasibility stage or an initial developmental stage have factored in in-pit crushing and conveying (IPCC) into their plans, encompassing either waste handling or ore mining.
IPCC has been shown to significantly reduce capital and operating costs, decreasing manning requirements, and reducing on-site emissions. This would reduce the peak number of trucks required to haul ore and waste.
“Having known the pros and cons of conventional IPCC solutions, Hazemag has developed a simplified crushing and conveying solution not only meeting the criteria of IPCC but surpassing it with significant additional benefits,” said Chiranjit Banik, Dy. Manager – Marketing, Hazemag India.
A crusher along with extendable conveyor can be located at a central, strategic location in a pit, which would take the waste material out of the pit and spread with a spreader reducing the requirement to haul waste material long distances to the waste dumps.
HAZEMAG is promoting the concept of minerals and overburden transportation with the use of mobile- or semi-mobile crusher with integrated wobbler and a conveyor from in-pit to ex-pit that can be moved to horizons with the commonly known methods: truck and shovel.
Hectronic delivers smart fuel management systems
Fuel consumption if not the highest, is certainly one of the major contributing factor for a mining project’s expenditure. Just by increasing its accountability and performing frequent analysis, one can discover deep insights and plan for any shortcomings. This is where Hectronic India shines as it provides a wide spectrum of end-to-end smart fuel management systems and services. “Although efficiency of a HEMM machines is quite not in your hands but what is in your control is minimising fuel losses like wastage during dispensing and other miscellaneous reasons. All such overhead losses will be cut down to bring about a tight closely-knit fuel autonomous system,” informs Hemant Dahale of Hectronic India.
Hectronic’s products are claimed to be a perfect blend of hi-tech hardware and software. Every transaction is recorded in its terminal which is then backed up securely to a server. All recorded data can be retrieved, analysed and translated to documents like excel, PDF, .csv and many more. Moreover, their SAP integration provides real-time data communication to clients, and with the flexibility of ERP integration any client-side software can be used to control all fuelling activities flawlessly.
Hectronic uses RFID technology to automatically dispense programmed amount of fuel only to the authorised vehicle and thereby eliminating unethical practices. “We also pioneer in wet stock management i.e. monitoring underground tanks and sensor systems that help keep a check on fuel stock. For mining sites which are operating in rough terrains where setting up autonomous fuel system is not feasible we provide bowser solutions, extending our expertise to on-the-go tanks carrying fuel. After a short period, the benefits of these solutions easily outweigh its cost,” explains Dahale.
Komatsu focusses mine safety and productivity
Komatsu Mining Corp. (KMC) is focused on creating new products and services to enhance mine safety and productivity.
Advanced analytics and processes: “Our smart solutions team offers advanced analytics and direct services customised to solve our customers’ toughest challenges,” said Soumitra Mukherjee of Komatsu Mining Corp. Smart solutions can be used to significantly increase productivity, plan maintenance and improve safety for mining operations around the world.
Smart products: KMC’s products can be configured for any operating conditions. They also come equipped with sensors that capture data to help operators predict significant changes in operating conditions, allowing workers to make adjustments as needed.
Advanced automation: KMC provides several options for improving productivity, safety and fuel efficiency through automation.
As major mining operators in India are state-owned, government must realise the importance of the new technologies and encourage the vendors to get the benefits faster and better.
Manoj Kumar, Assistant Vice President – PMG, Bevcon Wayors Pvt Ltd
The keys to maximising returns in our industry lie in adopting new techniques and technologies.
Samaresh Mitra, National Sales Head – OE, Komatsu Mining Corp.
Modernisation is not simply mechanisation and/or gradual implementation of new technology. It is a process of transition and transformation of the mining industry of yesteryear and today to that of tomorrow.
Shantanu Banerjee, Country Head,Hazemag India
Having known the pros and cons of conventional IPCC solutions, Hazemag has developed a simplified crushing and conveying solution not only meeting the criteria of IPCC but surpassing it with significant additional benefits.
Chiranjit Banik, Dy. Manager – Marketing, Hazemag India
Mines of the future would focus on digital mining, Big Data analysis, knowledge production and mining mechanisation. Technology makes economic sense for ore mining.
Mukaya Simubali, Executive Director,AAC Mining Executors Group
We not only develop innovative machines of the highest quality. With our machine technology, we also constantly endeavour to keep environmental pollution as low as possible.
Ramesh Palagiri, Managing Director and CEO, Wirtgen India
The ease with which mining is handled in any part of the world compared to probably few decades ago has periodically changed for the betterment.
Hemant Dahale, Managing Director,Hectronic India
Our Smart Solutions team offers advanced analytics and direct services customised to solve our customers’ toughest challenges.
Soumitra Mukherjee, Dy. Director – Marketing, Komatsu Mining Corp.
Cookie Consent
We use cookies to personalize your experience. By continuing to visit this website you agree to our Terms & Conditions, Privacy Policy and Cookie Policy.