No-Leak Zone: Tough solutions for tough conditions in construction and mining sites
By Edit Team | September 22, 2022 12:09 pm SHARE
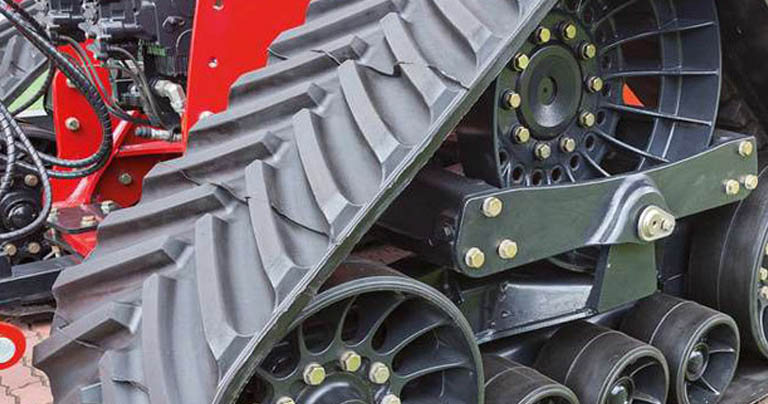
The trend toward mechanised lot implementation, intelligent remote-control systems, and automation for heavy off-highway equipment in the agriculture, construction, and mining industries means safety and efficiency are more important than ever. These advancements enable heavy equipment to operate autonomously and work in increasingly harsh environments. To ensure the equipment runs efficiently and reliably with minimal downtime in these new frontiers, all components, including the mechanical face seals, need to withstand both rough terrain and temperatures that can range wildly from one continent to another.
Mechanical face seals also called lifetime seals and floater seals, are important to the long-life function of heavy equipment in agriculture, construction, and mining. The performance requirements for this equipment are becoming more stringent because of the trend toward autonomous solutions. Mechanical face seals are specialised deals that protect the shafts and inner parts against the external environment, which they simultaneously protect by preventing oil leakage from the inner components.
These are heavy-duty seals for extremely harsh environments. They are specifically engineered for rotating applications in extremely arduous environments in which they withstand severe wear and prevent the ingress of harsh and abrasive external media. As technology plays a bigger role in agriculture, construction, and mining, equipment will be expected to perform more efficiently and consistently than ever before, especially for global OEMs that build equipment designed for varying terrain. Mechanical face seals play a critical role in applications such as transmissions, gearboxes, and undercarriages because of their simple, reliable design, long service life, and ease of assembly.
There are two types of mechanical face seals. The first and most common type uses an elastomeric O-ring as a secondary sealing element. The second type uses an elastomer with a diamond-shaped cross-section as a secondary sealing element instead of the O-ring. Both types consist of two identical metal seal rings mounted in two separate housings face-to-face on a lapped seal face. The metal rings usually come in Bearing Steel & Cast Iron. Trelleborg Sealing Solutions has recently launched a new material called “Nexus”. Nexus is a new spring steel material used to produce mechanical face seals with good performance for construction equipment in which peripheral speed is relatively low. Nexus mechanical face seals also have more flexibility against mud packing.
Advantages and operating conditions
In muddy and aggressive environments in the off-highway industry, mechanical face seals offer advantages against vibration and misalignment. All in all, the mechanical face seal provides cost-effective sealing against external dirt, sand, and water. Protecting and extending the life of large equipment also improves sustainability by reducing the volume of damaged parts and components that end up in landfills.
Nexus Seals offer the following advantages:
• High sealing performance in an application where peripheral speed is limited
• Nexus shows good flexibility against MUD compression.
• The excavators and construction machines are working in a very tough environment where the MUD attach is very aggressive. The MFS needs to resist the MUD compression that pushes on metal parts.
• With different types of mechanical face seals that can be made with three types of materials, Trelleborg Sealing Solutions can help identify the right solution for the job and offer tough solutions for tough conditions.
For more information https://www.trelleborg.com/en/tssindia
Cookie Consent
We use cookies to personalize your experience. By continuing to visit this website you agree to our Terms & Conditions, Privacy Policy and Cookie Policy.