Obtaining welding efficiency through robotic and digital machines
By Admin | November 1, 2022 6:17 pm SHARE
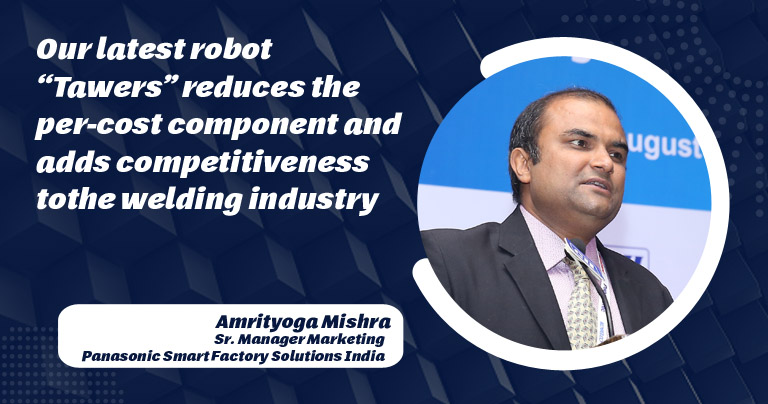
What unique features of your equipment and technology give you a cutting edge over others?
Panasonic Robots & Machines has many unique features that help customers achieve great productivity through high-speed, high-quality welding. Some of their characteristics are
Panasonic manufactures the full Arc welding robot, including the power source, controller, and manipulator. In the case of competition, the client needs three sources: one for power, another for the controller and manipulator, and a third for integration of these. However, Panasonic offers single-window options.
The “Tawers” line of robots uses a single CPU as both a power supply and a controller. This provides 250 times quicker connection speeds and 1.5 to 2 times faster welding speeds than current robotic technologies on the market.
The Super Active Tawers – this is the latest robot developed in the “Tawers” range. It has unique software installed under the name “HBC-Heat balance control.” HBC is a very useful tool for the welding of high-tensile steel.
The Super Active Tawers is the most recent robot in the “Tawers” line. It is outfitted with proprietary software known as “HBC-Heat Balance Control.” HBC is an extremely important instrument for welding high-tensile steel.
The 350GL5 is a completely digital MIG/MAG pulse welding power source. It is the first full-digital welding machine manufactured in India by any company. Other countries’ full-digital welding machines are imported by our competitors. PSFSIN believes in “Make-in-India.”
It has numerous advantages that will assist the Indian sector in generating welds of world quality. There is a feature known as “ALC-Arc length consistency,” which is an encoder feedback system that eliminates tiny shaking of the welding flame while still allowing less experienced operators to produce a mature weld output. It is a critical attribute because India currently has a severe dearth of competent welding operators, resulting in very precise welding output.
Could you please tell us about the need to improve equipment efficiency in your industry?
Most metal fabricators continue to use outmoded technology (diode and thyristor).Welding equipment manufacturers are organising several training programmes to educate consumers on how to use the most recent IGBT inverter technology. IGBT machines usually consume 20-30 percent less energy. Energy-saving methods can result in significant cost reductions. A 400-amp welding power supply, for example, runs 12 hours per day, 300 days per year, and consumes almost $1,000,000 in electricity. This annual power cost per machine can be reduced to 70,000-80,000. If 50,000 old-technology welding machines are still in operation, switching them to more power-efficient IGBT machines might save approximately 150 crores of rupees each year. In terms of cutting-edge technology, “tawers” would produce 1.5-2 times more output if installed. As a result, the cost per component (CPC) can be reduced greatly, and industry competitiveness improves.
What initiatives are taken by your organisation to manage/reduce waste?
Lead, polybrominated diphenyl ethers (PBDE), mercury, hexavalent chromium, cadmium, polybrominated biphenyls (PBB), and phthalates (DEHP, BBP, and DIBP) are all examples of pollutants. These toxins endanger both people and the environment. Panasonic products can thus be disposed of safely without risk of harming individuals or the environment.
Do you notice any shift in the procurement pattern for equipment and technologies?
There is a critical shortage of welders in India. Approximately 30 percent of welding operators and engineers are imported to complete projects on time. The market has demonstrated two tendencies to solve this issue: The automotive industry has traditionally utilised the great majority of welding robots, accounting for roughly 95 percent of global consumption. However, robots are gradually catching up in other industries, such as hospital beds, wheelchairs, the furniture industry, and gym equipment.
Customers prefer the more expensive comprehensive digital equipment that is offered. These tools help welders repair their mistakes and generate excellent welds. These devices have a cutting-edge waveform and a feedback mechanism for the encoder.
How can welding technologies and equipment contribute to recycling old and waste equipment?
Welding equipment is widely beneficial for maintenance and repair applications. This prevents the customer from buying new equipment. There are 2 types of M&R welding in the industry.
It also includes the repair of broken products, like the surfacing of equipment to enhance product life.
Some application areas in a typical thermal power plant:Coal handling components include the Coal Vibratory Screen CAM, Hopper/Feeder Guide plates, Crusher Rings, Body plates, and Primary air fans. Mill plant-Coal pipe bend, Coal chutes, Louvre ring and blades, Ventury Cone.
It also includes products for boiler maintenance, turbines, Ash Handling, and other applications like raw water pump impellers and sleeves, ID fan Casing, ID Fan Blades, Motor End Covers, and Electrical Contact.
Cookie Consent
We use cookies to personalize your experience. By continuing to visit this website you agree to our Terms & Conditions, Privacy Policy and Cookie Policy.