On the road to Robotics
By Edit Team | February 17, 2014 9:40 am SHARE
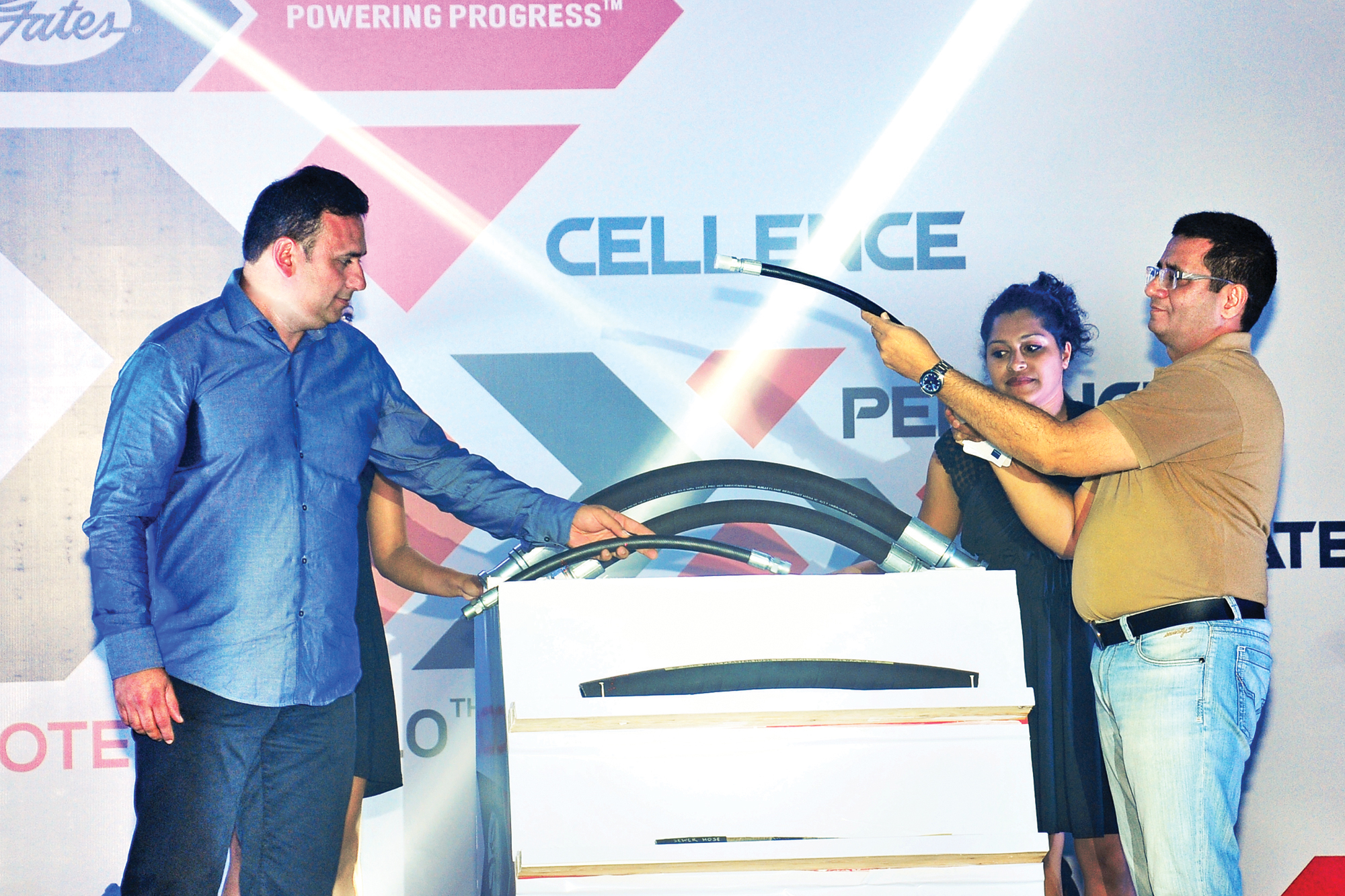
Polysoude invests in new development facilities
Polysoude has been proposing comprehensive automated welding solutions for many years. Multi-axis CNC systems, and even robots, are designed to cope with demands for increasingly high welding or cladding speeds in numerous industrial sectors.
Almost all industrial manufacturers faced with high output rates must also tackle difficulties relating to the complexity of the applications and the solutions available on the market. If the purchase and definition of components are still within their grasp, the assembly and interfacing required to turn them into a functional machine can prove to be a more arduous, if not impossible, task.
Polysoude brings full integration into the realms of possibility through its commitment to supply “turnkey” systems. The notion of “turnkey solutions” at Polysoude goes beyond what is traditionally understood. It means, above all, sharing the risk with the customer and an obligation to perform in an environment where:
• Applications are particularly complex
• The customer and the developer reach a mutual agreement on the basis of a set of specifications without necessarily knowing all the details at the outset.
Today’s conventional automated welding solutions are restricted in most cases to linear or rotary movements due to the torch holder. However manufacturers are increasingly having to deal with complex welding or cladding trajectories or limited accessibility or environmental constraints.
Robots – essentially multi-functional, multi-directional and multi-tasking tool holders – are particularly suited to welding by focusing on the torch – the decisive component in the tools developed by Polysoude. The “robotics” approach is however not a recent phenomenon at Polysoude. On numerous occasions over the last decade or more, the company has integrated different brands of robot to meet customer needs as closely as possible. Therefore, wherever irreproachable joint quality is a compulsory factor, the axes of movement and motion peripherals are designed on a case-by-case basis to transform the robot into a more suitable control device. Moreover, the robot can accommodate all types of torch depending on the cold-wire or hot-wire TIG or plasma welding process adopted, not only for standard joints but also narrow gap applications.
This approach has resulted in the acquisition of new programming skills within the company’s Applications Department for the development of welding procedures. At the Polysoude headquarters in Nantes, the company – which boasts 50 years of experience in welding and cladding techniques – has invested in a robot to develop specific tools and to study these applications. This opens up other channels in which technological solutions can be optimized to ensure that perfect integration can be achieved.
The synergy between knowledge of welding and cladding techniques and robot integration represents a culmination in technological support to provide the best solution to industrial manufacturers’ specific needs.
Cookie Consent
We use cookies to personalize your experience. By continuing to visit this website you agree to our Terms & Conditions, Privacy Policy and Cookie Policy.