Overcoming complex design constraints with innovative solutions for a massive aircraft hanger
By Edit Team | October 27, 2023 2:42 pm SHARE
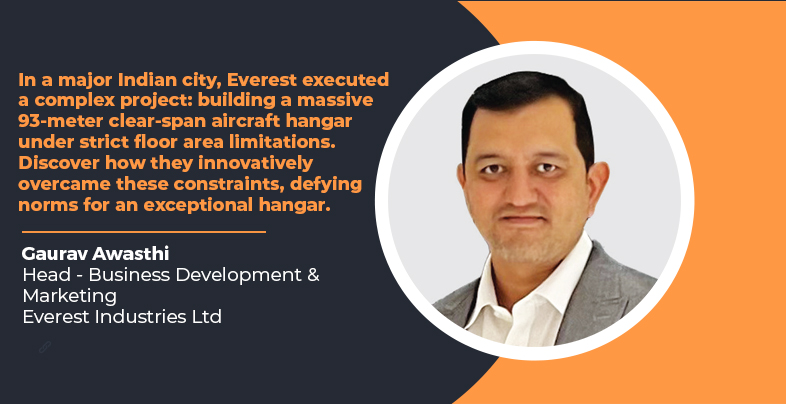
In a major Indian city, Everest faced a challenge: building a massive 93-meter clear-span aeroplane hangar under strict floor area limitations. Discover how they innovatively overcame these constraints, defying norms for an exceptional hangar.
Project brief:
Everest executed a prestigious project of a commercial aeroplane hangar with a clear span of 93 m in one of India’s leading metros. Indigo, the end user and consultant, had specific limitations of floor area usage strictly imposed by the authorities that were making the design of the aeroplane hangar impossible by conventional methods – called a “fixed base” design.
Challenges and solutions
The design and engineering team of Everest worked with the consultant and understood the reason for the limitations in space. Once the same was acknowledged as non-negotiable, the design team from Everest revisited the design concept and successfully performed the design using the “pinned base” philosophy.
In a fixed base design, the vertical columns supporting the structure transmit the imposed loads and the moment to the base via their base plates. Since the size of the base plate has a direct bearing on the size of the concrete pedestal where anchor bolts are cast, this directly causes the civil work sizes to increase in the form of a heavier pedestal.
In a pinned base design, the moments are absorbed and compensated at the joint between the column (vertical member) and rafter (horizontal member). This means that the coupler between the column and rafter (called “haunch”) is designed to be much heavier and rigid.
The key challenges in a pinned base design include heavier haunches and iterative designs, including kicker elements (plates provided at the haunch) to the higher loads and higher deflections at the centre of the rafters. These require an intimate compensation understanding of the interplay between the various forces and the sensitivity of members to each. ESBS design team is very well versed in these complexities and could easily handle this complex design without compromising the integrity or safety of the hangar.
Conclusion
Using a pinned base reduced the area of the base plate by nearly 70 percent, and an overall saving of 10 percent was affected in the weight. In addition, the inside-to-inside and outside-to-outside dimensional limitations of the hangar were also maintained.
Expertise shared by Gaurav Awasthi, Head-Business Development & Marketing, Everest industries ltd.
Cookie Consent
We use cookies to personalize your experience. By continuing to visit this website you agree to our Terms & Conditions, Privacy Policy and Cookie Policy.