Overcoming lubrication challenges in the crushing industry
By Staff Report | December 24, 2024 5:22 pm SHARE
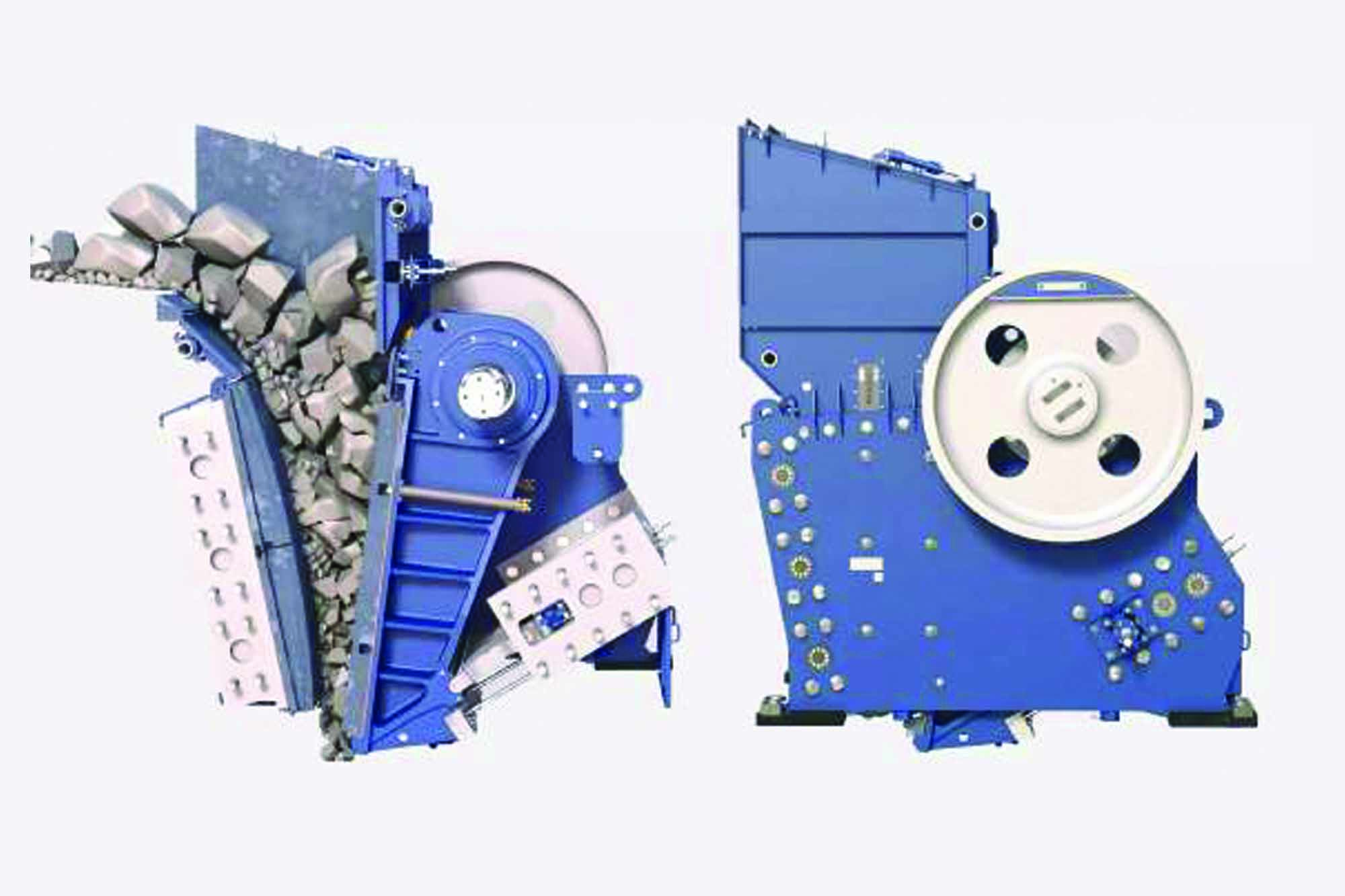
The crushing industry relies on durable machinery that faces extreme conditions daily, and effective lubrication is essential to prevent costly failures.
The crushing industry is the backbone of mining, building, and quarrying industries, where machinery faces harsh circumstances daily. Crushers crush hard, abrasive materials that require high performance from their components. However, this continuous pressure presents unique lubrication difficulties that, if not addressed, can result in catastrophic equipment failure, increased downtime, and increased maintenance expenses.
Key lubrication challenges
Overheating of machines: Crushing equipment frequently runs at high speeds and under heavy loads. This produces heat, which, if not controlled, can lead to overheating. Overheated machines can cause lubricant deterioration, lowering its effectiveness and making components subject to wear and tear.
Contamination: Crushers work in dusty, abrasive settings, making lubricant contamination a serious issue. Dust, dirt, and water infiltration can reduce lubrication efficiency, increasing friction and wear on moving components.
Seal damage: Seals are essential for conserving lubricants and preventing pollutants from entering the system. Crushers’ extreme operating conditions frequently cause seal breakage, resulting in lubricant leakage and contaminant penetration, increasing maintenance requirements.
Bearing damage: Bearings are essential for crushers, ensuring smooth rotating action. However, poor lubrication, pollution, and excessive operating loads frequently cause bearing damage, resulting in unscheduled downtime and costly repairs.
Reduced bearing life: Continuous exposure to excessive loads, impurities, and inadequate lubrication significantly shortens bearing life. This issue affects the overall reliability of crushing equipment, increasing operating inefficiencies.
Addressing lubrication challenges in crushing equipment
Use high-performance lubricants: Specialised lubricants designed for high-temperature, high-load conditions are required. Products with high thermal stability and oxidation resistance perform consistently, even in harsh environments.
Implement advanced filtration systems: Filtration systems can remove impurities from lubricants, increasing their efficacy and safeguarding components against wear. Regular filter replacement and lubricant monitoring are critical for keeping equipment in good working order.
Adopt preventive maintenance programs: Routine inspection and lubrication of critical components such as bearings and seals can help prevent equipment failures. Using lubricant analysis techniques allows you to discover possible problems before they escalate.
Upgrade sealing systems: Investing in long-lasting, high-quality seals protects against lubricant leakage and contaminant infiltration. Regular inspection and replacement of broken seals decreases downtime.
Train staff in proper lubrication practices
Educating maintenance teams on best practices for lubrication management, such as proper lubricant selection, application procedures, and intervals, improves equipment reliability.
The crushing industry’s success is strongly reliant on the efficiency and dependability of its equipment. Addressing lubrication issues—overheating, contamination, seal damage, bearing damage, and reduced bearing life—is critical to decreasing downtime, prolonging component life, and lowering operational costs.
High-performance lubricants, better-filtering systems, preventive maintenance methods, and improved sealing technologies can help the crusher sector overcome these problems and achieve long-term production.
For operations in this demanding industry, investing in a robust lubrication management strategy is not an option—it’s a necessity. To learn more about our offerings, please visit – https://www.molygraph.com/industries/mining
Cookie Consent
We use cookies to personalize your experience. By continuing to visit this website you agree to our Terms & Conditions, Privacy Policy and Cookie Policy.