Overcoming Traditional Cutting Challenges with CNC Bevelling Machines
By Edit Team | October 7, 2023 6:35 pm SHARE
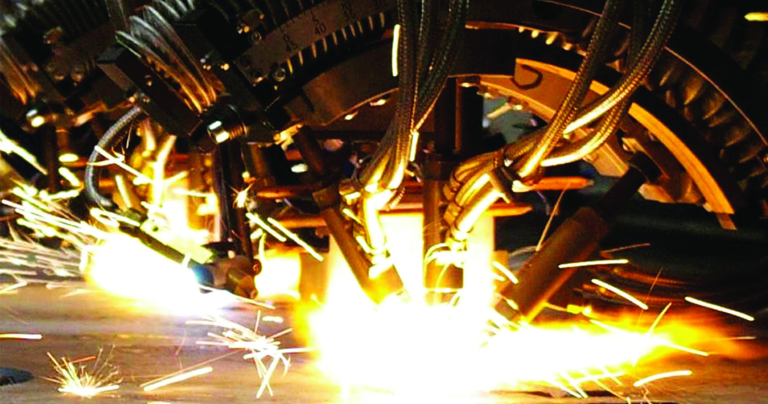
A clean, consistent gap between the two pieces to be welded will produce a stronger, more consistent weld with less filler metal, reducing costs and saving time.
Edge preparation in the welding industry is a type of art. In this interview, Messer Bevel Solutions discusses the challenges associated with mastering this trade using traditional methods and how CNC bevelling is raising the bar for weld quality.
Why is bevel cutting needed in fabrication units?
In any application, properly preparing metal for welding is key to producing high-quality results, maintaining consistent productivity levels, and minimising costs, especially those related to rework and downtime.
Preparing metal for welding is often done by cutting, fitting, and bevelling the base material. The amount of care and preparation put into the initial cut can reduce the amount of work that goes into post-processing later.
Many tools can be used for cutting, including a torch/plasma cutter, shears, laser/waterjet/CNC tables, and manual tools such as cutting wheels, mechanical bevel cutters, etc. However, each method of edge preparation has its pros and cons.
Properly preparing metal for welding is the key to producing high-quality results, maintaining consistent productivity levels, and minimising costs.
Offhand, cutting with a right-angle grinder is inexpensive, portable, and does not require as much setup and maintenance as most of the other options. But to achieve clean, straight cuts, you need a fair amount of practice and skill. Making the initial cut as clean, straight, and consistent as possible will make it easier to produce quality results.
A clean, consistent gap between the two pieces to be welded will produce a stronger, more consistent weld with less filler metal, reducing costs and saving time.
Challenges in the current scenario for edge preparation
The accuracy of a fabricated or welded component mostly relies on welded edge preparation, fitment or alignment of parts, and welded joints. Having understood that the existing industry practices of edge preparation are done with hand grinding, torching, or plasma cutting by hand, portable beveling machines, stationary beveling machines,
There are several challenges associated with the above process. Firstly, it involves more dirty operations and results in rough surfaces. Secondly, there are issues with inconsistent bevel surfaces. Additionally, the process requires a high setup and cycle time for each component. Safety is also a concern due to unsafe practices in hand grinding. Furthermore, there are high operating costs and a reliance on heavy human effort. Fitments can be inconsistent, leading to poor aesthetics. Lastly, fabrication errors can occur due to poor weld joints.
The solution to edge preparation
Automatic edge preparation is achieved through CNC bevelling via the thermal cutting process, which gives an accurate edge quality for welding. Setup time is negligible in the case of CNC bevelling. The thermal cutting process is one of the easiest ways to achieve clean cuts with accurate dimensional results. However, the thickness of the bevelling process is limited based on the nature of the process.
Spokesperson – Ravichandran Duraiswamy, Assistant General Manager – Product Management, Messer Cutting Systems India Pvt Ltd
Cookie Consent
We use cookies to personalize your experience. By continuing to visit this website you agree to our Terms & Conditions, Privacy Policy and Cookie Policy.