Panasonic enables automated welding with robotic systems
By Edit Team | March 5, 2020 11:59 am SHARE
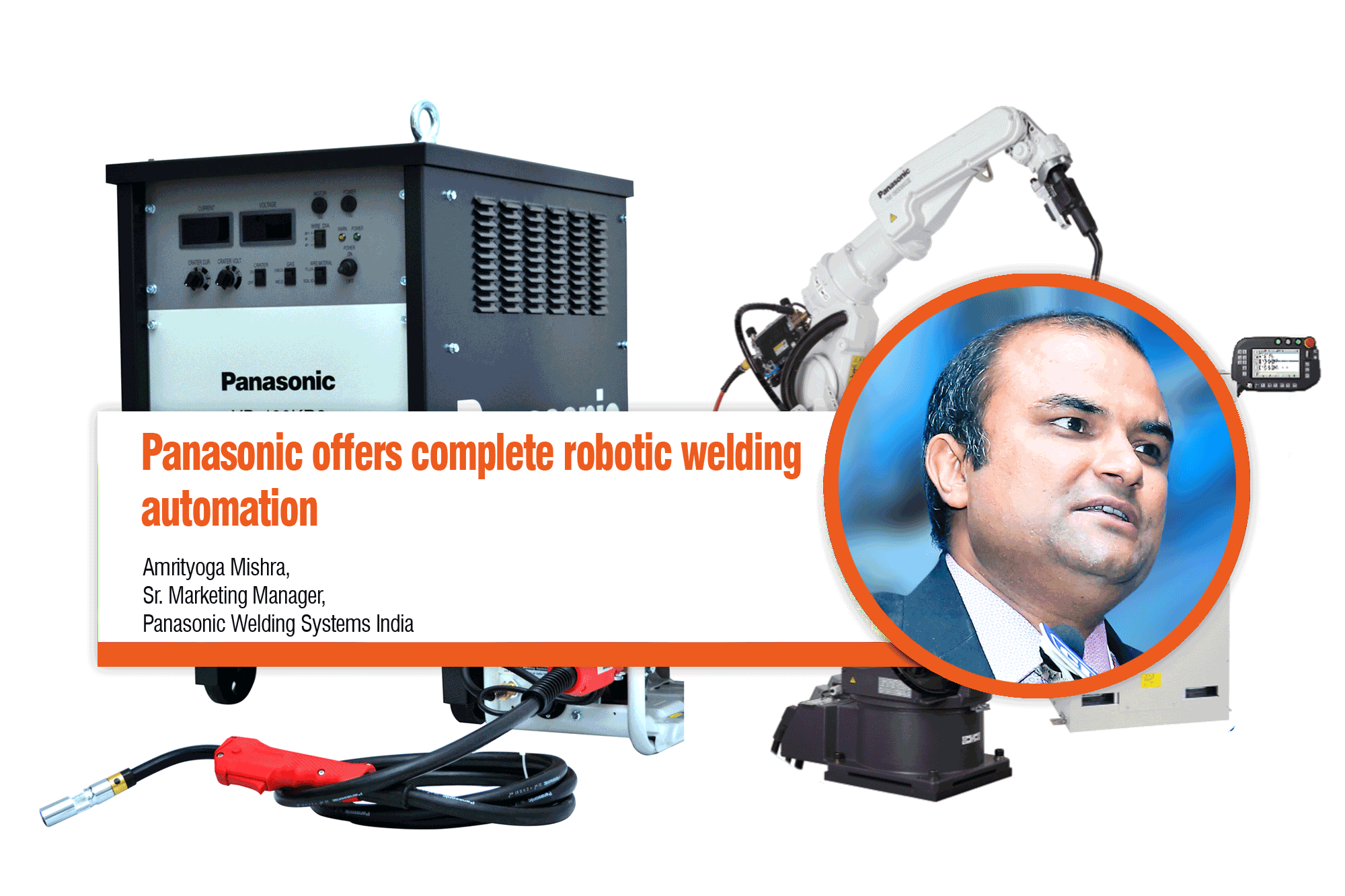
Amrityoga Mishra, Sr. Marketing Manager, Panasonic Welding Systems India talks about different robotic automation systems and how the welding sector is changing with times.
In the current economic scenario what are the market opportunities for your products in India?
India’s growth slowed down to 4.5 per cent in the July-September quarter of FY 201920, which is lowest in last 10 years. But there appears a green shoot as Purchasing Managers’ index (PMI) for manufacturing and services was 55.3 for January 2020, which is at eight year high. We are optimistic that GDP growth will pick up to six per cent in next FY2020-21 as compared to probable GDP growth at five per cent in the current FY 2019-20 (at 2011-12 prices). The Government of India, under the Make in India initiative, is trying to give boost to the contribution made by the manufacturing sector and aims to take it up to 25 per cent of the GDP from current 17 per cent.
These figures dictate a very good opportunity for welding machines and robots. Besides three huge investment plan will propel the growth of welding products and they are as follows:
- India is expected to attract investment of around US$ 100 billion to develop the oil and gas infrastructure over next five years.
- Infrastructure sector (power, bridges, dams, roads and urban infrastructure development etc) – US$1.5 trillion investment planned over next five years.
- US$ 750 billion investment planned in railway infrastructure over next 10 years.
What are the innovative products you offer for the construction and infra segment?
We have machines and robots with many special features for construction and infrastructure sector as follows :
Pipeline construction: We have special MMA welding power source, which is in high demand to use cellulosic electrodes. These special MMA welding power sources are safe to run on diesel generator as voltage fluctuation of up to +/-20 per cent also is no problem.
Earthmoving and Mining equipment – like backhoe loader, excavator, telehandler, soil compactor, crane etc. We provide complete robotic automation (with touch sensor and arc sensor) for the equipment parts like Bucket and boom welding. We also have MIG/ MAG power source 500 Amps @100 per cent duty cycle for manual MIG/MAG welding. This machine is highly preferred by heavy metal fabricators.
Power plant and other plant erection: We have MMA -400 machine which due to its internal compartment type design is dustproof and thus offers long life even in dusty condition. This machine has fan on top unlike usual on side panel, this feature provides strong cooling to electrical parts inside the machine ,thus this machine is able to perform well even in high ambient temperature like 50o C.
Tipper Trailor Truck: Panasonic has substantial market share due to its robust thyristorised MIG/MAG machine 400 amps.
Fabrication of steel girder bridges – MIG -500 Amp @100 per cent duty cycle is an extremely preferred machine for this application.
In a timeline when a number of processes are getting automated, what will be the role of automation in the welding sector?
There is a severe shortage of skilled workforce in welding and also speed of welding needs to be increased without compromising on quality to compete in the global market. And for these two reasons welding automation is catching up fast. In future, welding automation will go beyond its tradition automotive sector and will extend to other sectors like hospital bed manufacturing, e-rickshaw manufacturing etc.
Panasonic has a dedicated division which provides complete robotic welding automation to customers. We have already successfully supplied following complete robotic automation systems –
- Boom and Arm welding for construction equipment
- Bucket welding for construction equipment
- H-frame for construction equipment
- Fuel tank and inlet cap welding (2-Wheeler)
- Mining cutter (3 Cone bit assembly)
- Exhaust Muffler cabin manufacturing (2 Wheeler)
- EGR Cooler Assembly (4-Wheeler A.C.)
- Whitner Housing (Rice Mill Machinery)
- Structure frame assembly (Silencer mount assembly for M&HCV)
When it comes to the adoption of innovative welding techniques, how does the Indian market fare? Before the economic reforms in 1991, India was behind Japanese and European welding practice by 40-50 years. But currently majority of Indian metal fabricators are behind Japanese and European welding practice by 10-15 years.
Let us consider the generation of welding power sources as follows:
- Diode technology – 1st generation
- Thyristor technology – 2nd generation
- Inverter technology – 3rd generation
- Digital technology – 4th generation
In India, Inverter technology is used by approximately 40 per cent metal fabrication companies only and only two per cent are using digital technology. Around 58 per cent are still using Diode and Thyristor technology, whereas in Japan almost all metal fabrication companies are using inverter and digital technology.
In Japan, a new technology Direct diode laser welding technology, is fast catching up, it is expected to be 5-6 times faster than robotic spot welding in Passenger Vehicle (PV) car makers. But Indian PV car makers will adopt this technology probably after 15-20 years.
It is good news that due to “Make in India” initiative of Government of India, Indian companies are implementing new technologies faster than before so that they can manufacture products of global quality and are able to compete in the global market.
Cookie Consent
We use cookies to personalize your experience. By continuing to visit this website you agree to our Terms & Conditions, Privacy Policy and Cookie Policy.