Picking high-quality chemicals to ensure sustainability
By Edit Team | February 23, 2019 8:41 am SHARE
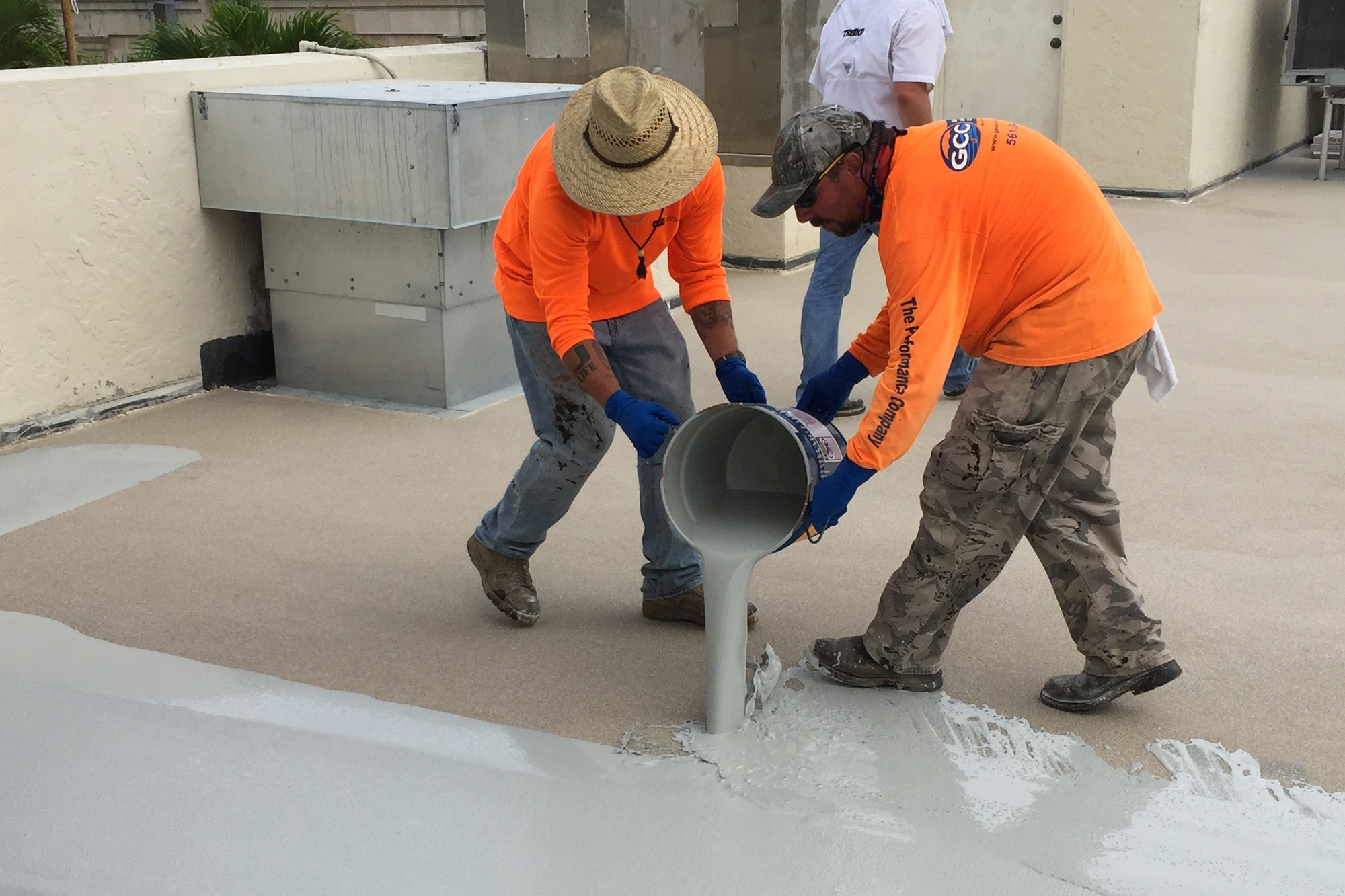
Selection criteria should consist of ease of application, chemical reaction with concrete, life of product once used in concrete, history of product performance.
Concrete consists of cement, sand, aggregate and water. Anything other than this, if added in concrete either before or during mixing to alter the properties to the desired requirement are termed as admixtures. There are two basic types of admixtures available viz. chemical and mineral. Admixtures like flyash, silicate fume, slag comes in the category of mineral admixtures. They are added to concrete to enhance the workability, improve resistance to thermal cracking and alkali–aggregate reaction and to enable reduction in cement content.
Buoying strength
Chemical admixtures are added to concrete in very small amounts mainly for air entrainment, reduction of water or cement content, plasticising of fresh concrete mixtures or to control the setting time of concrete. Admixtures can be broadly classified as superplasticizers, accelerators, retarders, water reducers and air entraining admixtures according to Shantal Naik, DGM – R&D, STP Ltd.
Superplasticizers help in reducing the water requirement by 15 to 20 per cent without affecting the workability leading to a high strength and dense concrete. The purpose of superplasticizers is to produce a flowing concrete with high slump 175 to 200 mm which is used in densely reinforced structures. Accelerators are added to reduce the setting time of concrete thus helping early removal of forms and are also used in cold weather concreting. Calcium chloride – a commonly used accelerator when used in reinforced concrete – can promote corrosion activity of steel reinforcement. Retarders are added to increase the setting time by slowing down the hydration of cement. They are preferred in places of high temperature concreting. Retarders consist of organic and inorganic agents. Most retarders also act as water reducers. They are called water-reducing retarders, thereby resulting in greater compressive strength due to low water-cement ratio.
Water reducing admixtures are added to concrete to achieve certain workability (slump) at low water-cement ratio. Water reducers are mostly used in hot weather concreting and to aid pumping. Air entraining admixtures entrain small air bubbles in concrete. These air bubbles act as rollers and thus, improve the workability and are also very effective in freeze-thaw cycles as they provide a cushioning effect on the expanding water in the concreting in cold climate.
Epoxy grouting is done based on the type of crack, width and depth of crack in concrete structure. Grouting of wide cracks requires large quantity of grout materials. In such cases, fillers are used to fill the cracks before epoxy grouting. Low viscosity epoxy resin and hardener composition is used for injection grouting of cracks. Based on the width of crack, depth and extent of cracks and other relevant details, the viscosity of the resin hardener mix, their proportions, pot life, application procedure etc. is selected in consultation with the manufacturer. The epoxy mortar selected should not be susceptible to fire and explosion during injection process and must be stable under varying climatic conditions, explains Naik.
Water-cement ratio
The main factor affecting the strength of concrete is the higher water-cement (W/C) ratio. A large amount of water present in the mix reduces the strength, up to a great extent as only around 20-25 per cent of the water gets consumed in hydration and the balance water tends to evaporate through the concrete body, thus, creating a large number of capillary paths inside the hardened concrete. As a result, concrete’s strength gets reduced. In case of higher W/C ratio, higher amount of water filled voids are available inside the concrete mass and as soon as the hydration process starts, due to precipitation, the hydration gel moves away from the surface of cement particle resulting in larger spaces available for development of gel formation. Hence, large vacant areas created inside reduce the strength of the concrete.
The solution for achieving workable concrete with the lower W/C ratio is an admixture. By using admixtures, we can create a repulsive force between cement particles and get better dispersion of the same. So, in one word, this can be described as a mechanical dispersion instate of water dispersion, says Sukanta Mallik, AVP – Business Development and R&D, CICO Technologies Ltd.
Despite such control of W/C ratio, there will be some capillaries left inside concrete, and there may be some voids or cracks left inside that can be treated through injecting grouting of low viscosity epoxy grout, he added.
Enhancing durability
More than just considering strength, today it is relevant to see how these materials can add to the life of the structure. These materials of course add strength to concrete by means of enhancing mechanical properties, but also add considerably to the durability of the structure,” Sunny Surlaker, Head of Marketing and Technical Communication, Tremco India Pvt Ltd, says.
Various admixtures added to concrete and they have many basic functions within a concrete mix, such as improve concrete performance (strength and permeability), enhance workability, resist thermal cracking, resist alkali-aggregate expansion, resist sulfate attack and reduce cement content.
Ingress of moisture is detrimental to concrete’s durability that in turn hampers the sustainability of a structure. Hence, making concrete a waterproof barrier is a more effective way to ensure water ingress is halted, Anandita Kakkar, Deputy General Manager, Kryton Buildmat Co. Pvt Ltd, says.
Making quality concrete
Admixture helps in improving various properties of concrete in fresh state such as workability, retardation or acceleration in setting time, reduction in segregation and bleeding, improved pumpability, slump retention, etc. In hardened state helps to improve durability, strength, permeability, early strength gain, etc.
Admixtures are added in smaller doses, and when plasticizer is added into concrete, it helps in reduction of water requirement in concrete that aids strength. This reduction is achieved by mechanism of electro-static repulsion or steric hindrance, type of acting mechanism is based on chemistry of admixture product. Durability is also enhanced by use of admixtures in concrete, says Akshay Rajpurohit, Head –Product Management Group – Construction Chemicals, Thermax ltd.
Uses of different type of admixtures in proper proportions help in achieving various types of concretes like free flow concrete, PQC concrete, self compacting or consolidating concrete.
Selection criteria
A host of factors have to be considered for selecting proper admixture. As a thumb rule, Mallik says, low-grade concrete – M10 to M25 grade Normal WRA; medium-grade concrete – M30 to M60 grade of concrete Superplasticizers; high-grade concrete – M50 and above the grade of concrete Hyper plasticizers; self-compacting concrete – superplasticizers or hyper plasticizers with VMA; pre-cast concrete – special superplasticizers.
Selection process of epoxy material is very critical as there are many considerations. Before going for an epoxy grout, consulting with technical consultant is recommended.
Moisture content of concrete mass, ambient temperature, amount of voids (this is important as the reaction is exothermic, and if the quantity is more, a huge amount of heat will get generated leading to adverse effects), nature of cracks, live or static and weather-exposed to sunlight or not should be consider while selecting suitable epoxy material.
Performance, durability, sustainability and most importantly, green quotient of the product should be the most important considerations in selection of right products for construction. In financial terms, it is better to consider life-cycle cost of the materials rather than initial cost, in order to ensure maximum cost benefits over life of the structure, says Surlaker.
Construction of durable structures is absolutely not possible without the right usage of construction chemicals. In short, any material that enhances structure’s durability in the long term increases sustainability, as it means lesser use of resources, material, manpower and money required in the maintenance and repair process.
Selection criteria should consist of ease of application, chemical reaction with concrete, life of product once used in concrete, history of product performance both on field and in lab, and fulfilling the need of concrete, says Kakkar. These are critical points that should be considered before choosing any admixture and only after weighing all options provided should any RMC, client or engineer select the right admixture for their concrete needs.
Selection of suitable grouting material depends upon the condition of structure. Generally, MMA- based products are suggested for highly unstable and fire-damaged structures owing to its fast curing and good bonding. Proper storage and handling has to be done for such products to get maximum benefits, says Rajpurohit.
Epoxy mortar selected should not be susceptible to fire and explosion during injection process and must be stable under varying climatic conditions.
Shantal Naik, DGM – R&D, STP Ltd
Using admixtures we can create a repulsive force between the cement particles and get better dispersion of the same.
Sukanta Mallik, AVP – Business Development and R&D, CICO Technologies Ltd.
Performance, durability, sustainability and most importantly green quotient of the product should be the most important considerations in selection of right products for construction.
Sunny Surlaker, Head of Marketing and Technical Communication, Tremco India Pvt. Ltd.
The most catastrophic element to the durability of concrete and further, the sustainability of a structure is the ingress of moisture.
Anandita Kakkar, Deputy General Manager, Kryton Buildmat Co. Pvt Ltd
An important aspect like durability is also enhanced by use of admixtures in concrete.
Akshay Rajpurohit, Head –Product Management Group – Construction Chemicals, Thermax ltd
Cookie Consent
We use cookies to personalize your experience. By continuing to visit this website you agree to our Terms & Conditions, Privacy Policy and Cookie Policy.