Polymer modified inorganic binder based waterproofing systems
By Edit Team | June 16, 2016 10:36 am SHARE
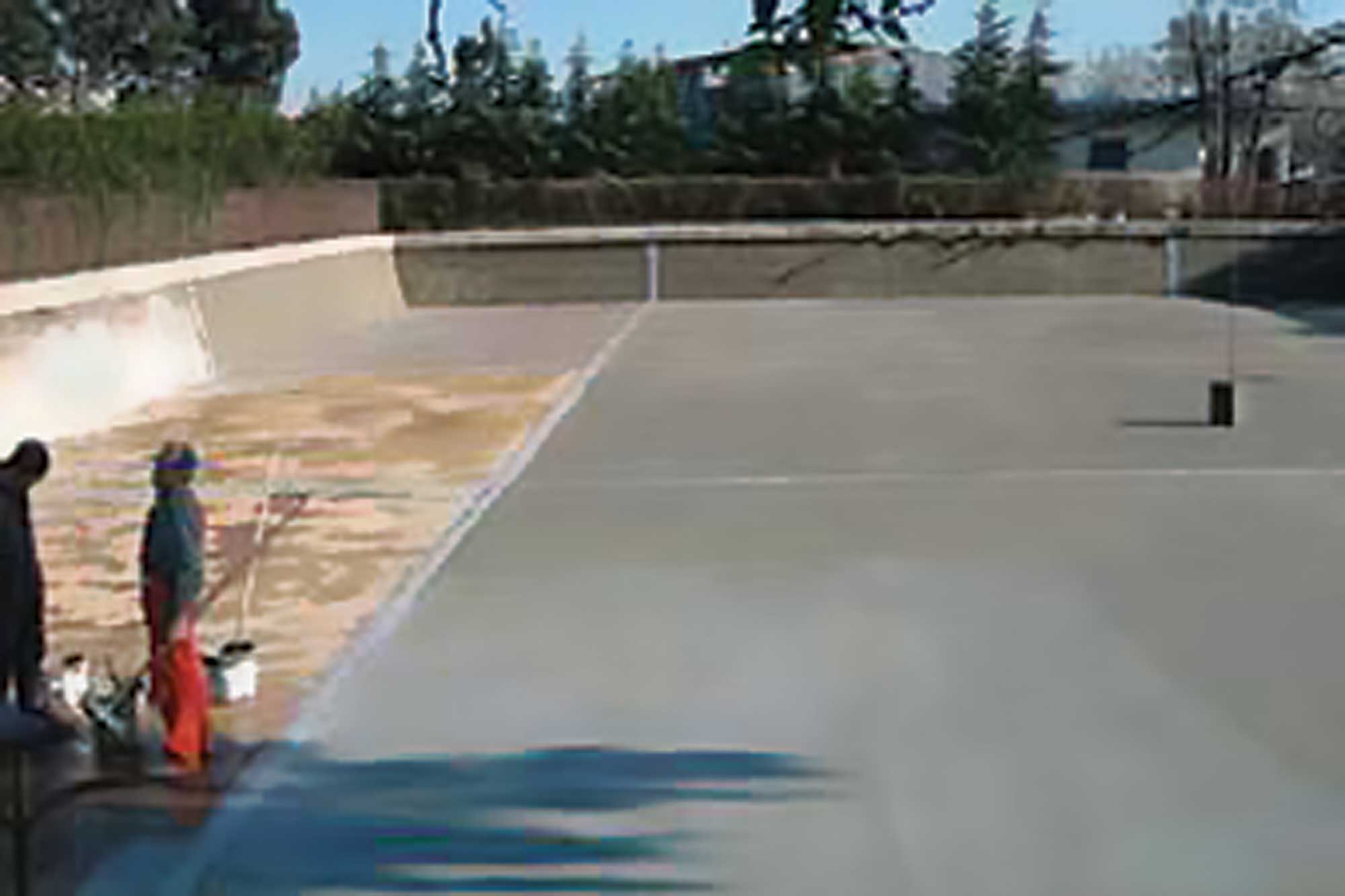
Of late, cement-based waterproofing materials have undergone fast development. This has paved way for realising of products, such as polymer modified cement-based waterproofing membranes, rigid polymer modified cement waterproofing mortars, crystalline waterproofing slurries, etc. among which the rigid polymer modified cement waterproofing material and the in-situ applied polymer modified cementitious membranes are the main products. The rigid waterproofing materials are modified by adding an organic polymer, a waterproofing admixture, a water reducer, and an expansion admixture to reduce and compensate for cement shrinkage, to prevent cracking, to reduce and refine the capillary pores of the materials, and to make the mortar denser and improve its impermeability remarkably. Although these materials have good aging resistance, they cannot accommodate extensive deformation of the substrate because of their rigidity. If drying shrinkage or expansion and contraction due to temperature changes lead to cracking of the substrate, the waterproofing layer may also suffer reflective cracking or delamination which will affect the waterproofing performance. Their application will find place for waterproofing of the concrete member subjected to unpressurised water stagnation and they cannot be applied to large-area waterproofing of engineered floors and roofs.
In recent years, waterproofing systems with a high ratio of polymer and cement are used as a liquid-applied membrane waterproofing materials which are widely used in apartments, basements, underground water tank, etc. They need mixing on site, and their single coating layer is thin due to the high ratios of polymer, cement and water, cement. Thus, the coated waterproofing materials need multiple coatings based on the degree of waterproofing required. The application of such products does not need highly skilled manpower and are easy to apply.
Talrak has developed products for better durability and less environmental impact during their application. They are cement-based waterproofing materials which are suitable to be used for different situations and are very user friendly. By improving the design, a polymer modified cement material with a lower polymer: cement and water: cement ratios, evenly mixed and dispersed at site. It combines the advantages of a rigid cement waterproofing material and flexible waterproofing material with a denser structure, better waterproofing performance, excellent durability, and capable of accommodating deformation of the substrate which can be prepared at site. These systems are suitable for indoor and outdoor or concealed areas of the structures. This material can bond to various mineral substrates and can be used on wet surfaces. Considering the advantages of the cement based waterproofing material, the material used in these products is essentially cementitious.
By blending hydraulic cement and a suitable polymer dispersion, a water-soluble polymer or a re-dispersible powder resin, or a hybrid system at a pre-weighed ratio of cement or polymer, a material that provides a flexible cement-based waterproofing system can be produced. The polymers used to modify the cement based system should meet the performance criteria of the cement-based waterproofing materials and the desired material characteristics. They should preferably have one or more of the following advantages:
• Higher filler binding capacity
• Good flexibility or high elasticity at application temperatures
• Excellent anti-ultraviolet ray resistance and good durability
• Good breathability and toughness
• Good film forming property at high temperatures
• Water impermeably
To enhance their tear resistance and alkali-resistant, short synthetic fibres, at a pre-determined ratio to cement are also added. The molecules of the polymer, used as modifier, are evenly adhered to the surface of the cement particles. A three dimensional network is formed in which the elastic film and the cement hydration products interpenetrates, which may greatly enhance the bond and waterproofing performance, rendering the cement materials more cohesive and hydrophobic. This also helps to get required toughness of the applied membrane.
For further details contact: chethana.g@talrak.co.in
Cookie Consent
We use cookies to personalize your experience. By continuing to visit this website you agree to our Terms & Conditions, Privacy Policy and Cookie Policy.