Polysoude demonstrates latest developments at Schweißen & Schneiden
By Edit Team | November 13, 2017 7:24 am SHARE
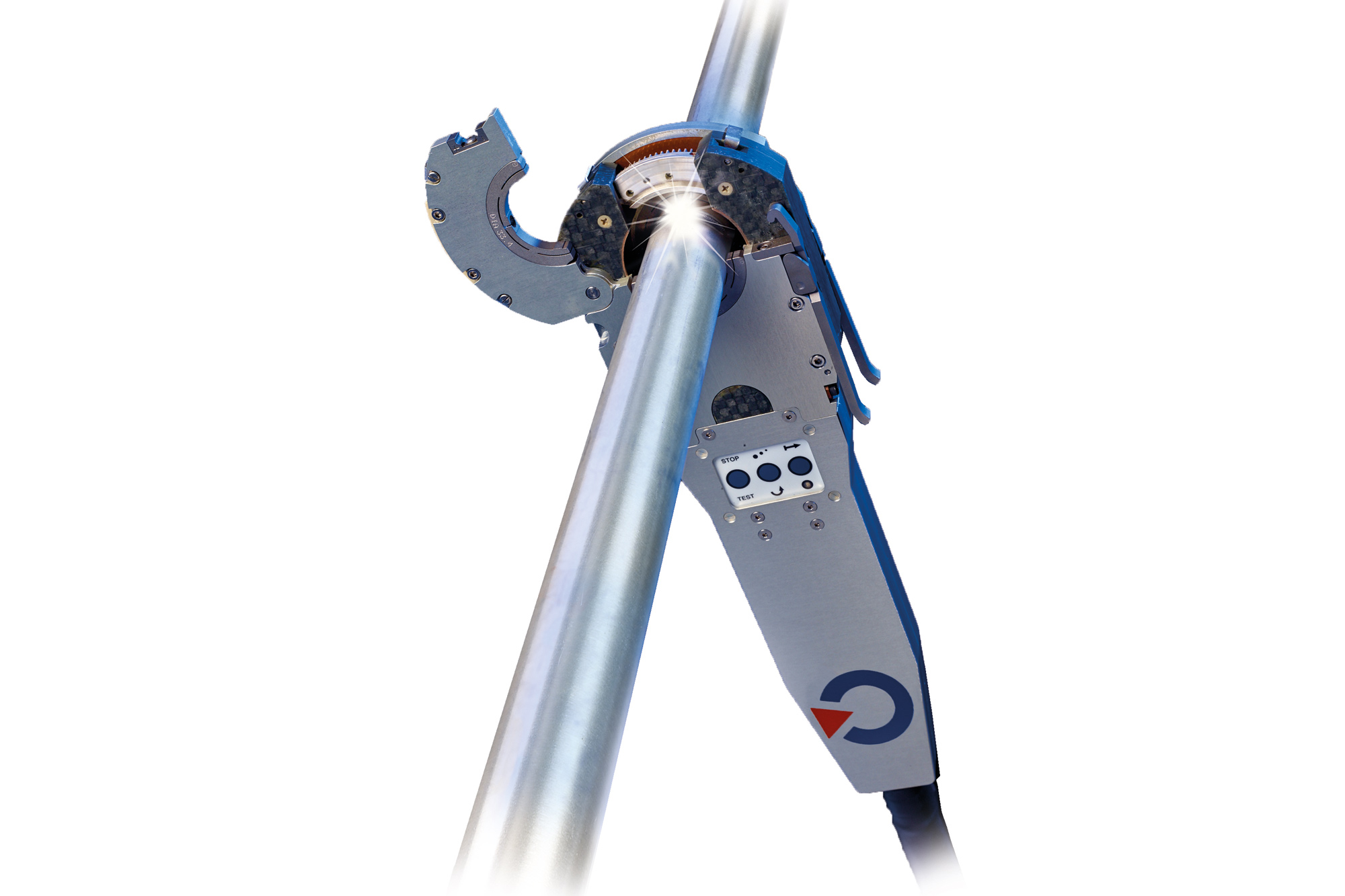
Polysoude demonstrated its latest developments in both the orbital welding and automated cladding industry at the Schweißen & Schneiden trade fair held in Düsseldorf, Germany. According to Polysoude, these developments have been driven by the need to satisfy the specificity of the customers’ need.
“With the recent economic difficulties, it has been seen that a significant investment in technology requires a significant improvement in productivity, ease of use and most importantly, product quality. Schweißen & Schneiden is a great opportunity for Polysoude to showcase these advances,” the company said.
The Schweißen & Schneiden trade fair provides the members of the welding industry with the opportunity to present their latest innovations in the market.
Expansion of the welding head range
In order to meet this demand, Polysoude has expanded its range of closed chamber welding heads with the MW 34 (Fig. 1), with an application range of 6 mm to 34 mm. Just like all the other welding heads from this series, the MW is in high demand, due to its ease of use with the controls placed directly on the handle of the head and a high duty cycle which meets growing market demand.
The MW welding head is the ideal product regarding size capability, meeting not only the reduced radial space requirements of the micro-fittings industry but also the quality requirements of pharmacology and food industries. Another considerable advantage of this welding head: the casing (TCI), used for all closed chamber welding heads by Polysoude, is made of titanium, this allows response to variations in temperature on the outer diameter of tubes. By using titanium, Polysoude is in a position to provide both a lifetime casing warranty and also the possibility to avoid all performance loss over time in comparison with aluminium casing.
The new tube-plate welding head
At the fair, Polysoude will also reveal the TS 8/75-2, the latest in the series of tube-plate welding heads. Several welding heads can be used simultaneously thanks to the more the more compact and ergonomic design of the double handle, with integrated welding and clamping controls. (Fig. 2) This welding head has an impressive level of automation with its integrated AVC. With this new series, even tubes with a lower value can be welded in assembly with the new clamping/centering system.
New development: Mastering the quality and productivity with data acquisition
The close collaboration between field staff and Research & Development has resulted in the creation of the new DAQbox (Fig. 3): a brand new concept combining data acquisition with functions enabling the optimisation of productivity while ensuring a reproducible weld of indisputable quality.
The core function of DAQbox is data acquisition, an essential tool for the production monitoring as part of the quality process. However Polysoude has added features that provide the welder and Quality Department with enhanced monitoring of the welding process.
As seen in figure 4, the welder can now simultaneously monitor the smooth functioning of the welding process and respect the operating procedure while closely following the deposit rate and the welding energy utilised.
In a single click the operator can choose the type of setting to be displayed and at all times return to the original settings.
The installation is done very simply with the use of a USB2 stick with a free software licence and there is no need for an Ethernet network. This way the data saved during the complete welding cycle can be read on any PC in order to validate production.
In comparison with data acquisition systems currently available on the market which consist of only six measurements (current, voltage, rotation speed, wire speed, hot wire current and gas flow) the DAQbox proposes the following additional data acquisition: temperature measurement, welding energy, wire deposition rate, linear and analog channels are increased to 15 (previously 5) and are customisable by the user according to the process requirements. Regarding the usability of the software, Polysoude exports more than 85 per cent of its equipment abroad, non-Latin languages such as languages such as Russian and Chinese are also available.
Automated welding: tailor-made by catalogue
A major concern for manufacturers is the length of time it takes between the decisions to install the equipment, up until the moment the equipment is ready to start production. This is considered as too long in many cases.
Having engaged in years of development and feedback, Polysoude has widened its approach to meet shorter deadlines. This therefore allows the proposal of standard elements of installation, even for the more complex of configurations.
The new Polysoude catalogues (Fig.5) contain the majority of solutions in the field of automated welding and cladding. They have become essential tools to respond to customer specifications, providing advice and enable the implementation of their projects. For some customers, the standard solutions may not meet all of the requirements. However, starting with the catalogue solutions, the Polysoude R&D team will focus entirely on a bespoke and unique solution. This installation will be perfectly compliant to with the product specification and delivered in an acceptable timeframe.
Contact
Polysoude India
Anil B. Kulkarni (Head of Representations)
Plot No. X-17 & X-1, MIDC, Bhosari, Pune-411026
Mobile: +91-9890529923
Tele: +91-20-27127678 Fax: +91-20-27137679
Email: ab.kulkarani@polysoude.in
Cookie Consent
We use cookies to personalize your experience. By continuing to visit this website you agree to our Terms & Conditions, Privacy Policy and Cookie Policy.