Polysoude India organises Technovation 2016
By Edit Team | May 17, 2016 10:43 am SHARE
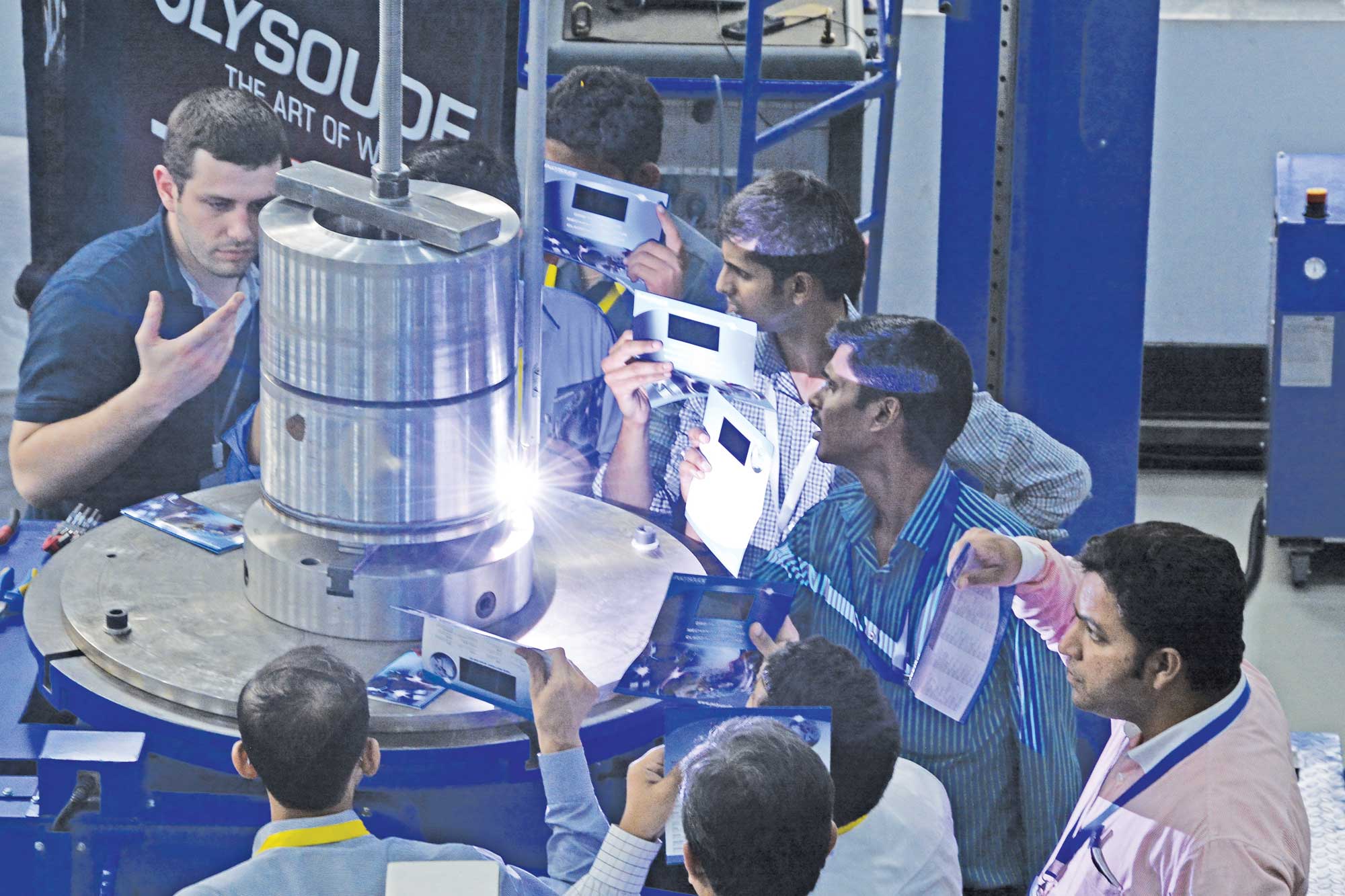
Polysoude India organised its ‘Open Days’ event under the name of Technovation 2016 on 9th and 20th April at its new premises in Pune.
More than 100 participants took part in the event during which Polysoude India arranged live demonstrations on orbital welding, automated Narrow Groove welding and weld overlay cladding in their brand new showroom. Hans-Peter Mariner, CEO and President of Polysoude inaugurated the event by presenting Polysoude India within the Global Welding Technology group. The TWI, represented by Chris Wiseman, Industry Sector Manager, was part of the programme showing the structure, activities and expertise of the organisation worldwide and in particular in India.
During the technical presentations, participants took the floor at several occasions to share their experience in the use of Polysoude equipment.
Numerous partner companies have completed the versatile event programme – for example EWM with a demonstration stand for manual welding and DWT for tube end preparation and bevelling. Other local suppliers have supported the event, as Anvin Engineering for heavy duty electro-mechanical assemblies and FSH Welding Asia for filler wire, and this way reinforced their collaboration with Polysoude.
The participants have been impressed by the new building, the technical possibilities and the organisation of the event. Some of them have expressed having learnt a lot and being interested in the exhibited products and services.
Strengthening presence in India
The Indian subsidiary of Polysoude grew from a small office to an operational entity in accordance with the potential of the country. Today the company offers complete orbital range, as well as for automated narrow groove welding and weld overlay cladding. Polysoude India also provides services with its adequate stock of spare parts.
Polysoude Nantes would continue to accompany the local team in order to help this new structure becoming a reference supplier in welding and cladding equipment in India.
Sharpening competitive edge of industrial customers
Orbital TIG welding is the ideal technology for tube-to-tube or tube-to-tube sheet welding applications when high quality welds are required. With or without filler wire, this is a stable, reliable process that can be used on steel, stainless steel, titanium and nickel and aluminium alloys, for example. With the latest generation of power sources, the development of a welding program, easily created via the graphical unit interface, guarantees a high-quality weld through automation. The welding cycle can be repeated as often as necessary with the same result.
For very thick-walled parts, another way of increasing productivity in addition to the Hot-Wire TIG process consists in reducing the groove, and therefore the volume to be filled by the weld. The use of an open-type carriage welding head equipped with a Narrow Groove torch limits the quantity of metal to be deposited. Additional gains are made on preparing the groove by limiting the loss of stock and the machining time. This technology guarantees a quality weld thanks to the TIG process and is perfectly reproducible by virtue of automation. Automation via a program recorded in the power source guarantees flawless production.
Another application of the TIG process is cladding. To increase their lifetime, components are coated in a resistant layer by the weld overlay cladding technique. Among the latest developments in terms of cladding or buttering, Polysoude’s TIGer technology is based on a special torch design that allows the juxtaposition of two TIG arcs. This technology is not only effective in meeting productivity requirements, but also provides a perfect response to constraints relating to the degree of dilution.
Cookie Consent
We use cookies to personalize your experience. By continuing to visit this website you agree to our Terms & Conditions, Privacy Policy and Cookie Policy.