Precast technology elevates construction quality
By Edit Team | September 7, 2023 12:02 pm SHARE
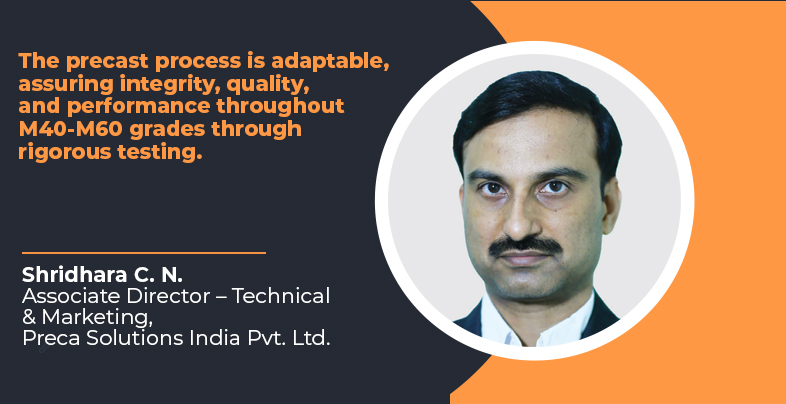
The precast process is adaptable, assuring integrity, quality, and performance throughout M40-M60 grades through rigorous testing.
In an interview with B2B Purchase, Shridhara C N discusses how precast technology boosts construction efficiency, structural design, cost-effectiveness, quality control, project scope, and environmental sustainability in a comprehensive interview.”
How has adopting concrete precast technology transformed the construction industry’s efficiency and project timelines?
The Indian market practically understands the benefits of precast technology. So many projects are delivered in very short spans compared to the normal conventional construction method. Also, the market understood that precast technology would increase the efficiency of the buildings in terms of bigger internal working spaces, quality, neat execution, good finishes, and durability.
What factors influence the design versatility and structural integrity of concrete precast components?
The aesthetic view (elevations) of the building any elevation can be achieved by using precast technology, but difficult elevations may cost a little more. Also, precast technology will help achieve any elevation shape per an architect’s or client’s dream. Structural integrity will be studied by considering the building profile, location, usage, and load factors. While doing analysis and design, the precast structural engineer has to consider all these factors.
How does the cost-effectiveness of concrete precast compare to traditional on-site concrete pouring in large-scale construction projects?
The cost-effectiveness of precasting is always to be looked at in terms of the project’s total cost. People should not compare the material cost of traditional construction with precast construction. Material costs are always higher in precast construction because the grade of concrete and quality are higher. The minimum grade of concrete will be M40 in precast construction. Sometimes, M50 and M60 grades of concrete are also to be used.
What are the rigorous testing standards and quality control measures ensuring the long-term performance of concrete precast elements?
Testing of the quality of concrete is mandatory while casting precast elements. Cube results are to be recorded in proper format and the production department accordingly. To maintain 70 percent of concrete strength as a benchmark for demoulding the elements from moulds.
Also, the design load tests are to be carried out on the randomly picked casted precast elements. The load test will be carried out for 24-hour loading, and the deflections will be adequately monitored.
Which projects have you commenced and completed with the new-age concrete and precast methods?
We started commercial building as the first project. In 10 years, we executed over 100 precast buildings in all sectors, such as hospitals, schools, commercial buildings, pharmaceutical sector buildings, industrial buildings, IT buildings, and crematoriums.
How do concrete precast methods contribute to reducing carbon footprints and promoting environmentally responsible construction practices?
We can use fly ash or GGBS to reduce the carbon footprint in precast construction concrete. Because most precast companies have batching plants, adjusting environmentally friendly concrete recipes is easy.
In precast construction, all building elements are cast at the factory and erected at the site using equipment. This will reduce a lot of pollution, which impacts the environment. The construction dust pollution will be drastically reduced using the precast methodology. It will reduce sound pollution. Also, it will save a lot of natural resources like water because the total curing process will happen at the factory, not at the site.
Spokesperson – Shridhara C. N., Associate Director – Technical & Marketing, Preca Solutions India Pvt. Ltd.
Cookie Consent
We use cookies to personalize your experience. By continuing to visit this website you agree to our Terms & Conditions, Privacy Policy and Cookie Policy.