Pro Series MIG machines are the latest digital welding machines
By Admin | August 13, 2022 11:49 am SHARE
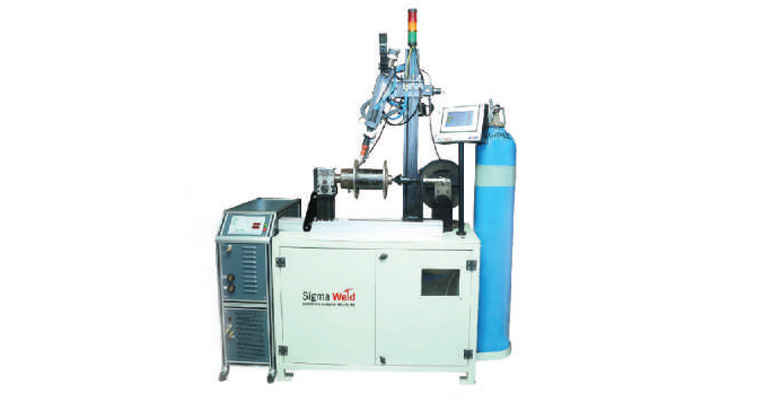
Nimesh Chinoy, Marketing Director, Electronics Devices Worldwide Pvt. Ltd., predicts that welding and cutting will play a significant role as India approaches a $5 trillion GDP.
What are the present market opportunities for welding and cutting solutions for infrastructure?
Infrastructure-based projects require greater productivity for their beams, columns, foam work structures, and other structural components. We have specialised Thin Wire SAW systems that help with I Beam, H Beam, and Pre- Fabrication Structure manufacturing. This enables the exploitation of the benefits of submerged arc welding for materials with modest thicknesses, ranging from 5 to 15 mm. The typical submerged arc technique performs perfectly above 15mm.
The typical submerged arc technique performs perfectly above 15mm. Additionally, switching from the traditional SMAW to GMAW or FCAW aids in raising production in this sector. To help them enhance their throughput, SigmaWeld offers semi-automated solutions, including magnetic trolleys, weaves, and unique carriages.
Which latest equipment and advanced welding and cutting technologies are used for fabrication in infrastructure?
Our Pro Series Mig machines are the latest modular technology-based digital welding machines. They provide specific welding programs, including DAC MD (Modulated Arc), Pulse, Super Pulse, and JetARC, enabling welders to weld in all positions and get greater penetration in a single pass. The system makes judgments every 6.7 microseconds when operating at 150 kHz. This enables the machine to make quick decisions and makes welding easier for the welder. The wire speed adjusts itself to maintain the constant arc gap if the user is inexperienced and has unsteady hands. This makes it possible for welders of all levels to produce a clean, excellent bead finish.
How do technologies like Laser cutting, WAAM, and others add precision and speed to projects?
WAAM, or loosely called metallic 3D printing, is still in its nascent stage, and many applications are being worked upon. Currently, they are helpful in making sophisticated parts that require a lot of machining or material removal from a block. WAAM can save a significant amount of material and time needed to construct the part. Therefore, the applications with high material prices are being assessed first.
The adaption in the aerospace and replacement parts industries is good. However, I don’t yet see it accelerating infrastructure projects in particular. SigmaWeld collaborates closely with a few research facilities across the nation that are developing numerous WAAM and 3D printing technologies. Laser cutting will add speed to the process and improve the child parts’ accuracy, making production faster.
What are the existing challenges in procuring weld equipment and technologies?
SigmaWeld has been manufacturing welding power sources, its PCBs and other parts in India since its inception. The global scenario at the moment has made procuring semiconductor ICs, capacitors, and power devices such as IGBTs difficult. The EV industry also requires many power electronic components, uch as similar or identical IGBTs, diodes, IC chipsets, and capacitors. The global focus shifting to EVs, the present situation in China, and Europe’s power crisis are all adding to the shortage of these key components. It is time for India to invest in semiconductor manufacturing and improve our capacity to produce capacitors and other electronic components.
How is it further impacting the project deliverables?
Supply chain delays will impact the deliverables of the projects. They may be delayed. We will have to let go of the lean and go fat again on the stocks to see this time through. The cost of projects will also go up.
How are laser technologies gaining prominence in cutting and welding applications?
The laser for welding and cutting is perfect and will be very useful in productivity improvement. It can enhance the speed of execution and weld quality too. However, it will need automation and will be capital intensive. Critical applications such as aerospace and nuclear will see a faster adaptation. Also, the automotive sector uses lasers very heavily.
How are laser technologies gaining prominence in cutting and welding applications?
The laser for welding and cutting is perfect and will be very useful in productivity improvement. It can enhance the speed of execution and weld quality too. However, it will need automation and will be capital intensive. Critical applications such as aerospace and nuclear will see a faster adaptation. Also, the automotive sector uses lasers very heavily.
Cookie Consent
We use cookies to personalize your experience. By continuing to visit this website you agree to our Terms & Conditions, Privacy Policy and Cookie Policy.