Promtech introduces cold galvanising by Zinc metal spray
By Edit Team | July 28, 2014 11:13 am SHARE
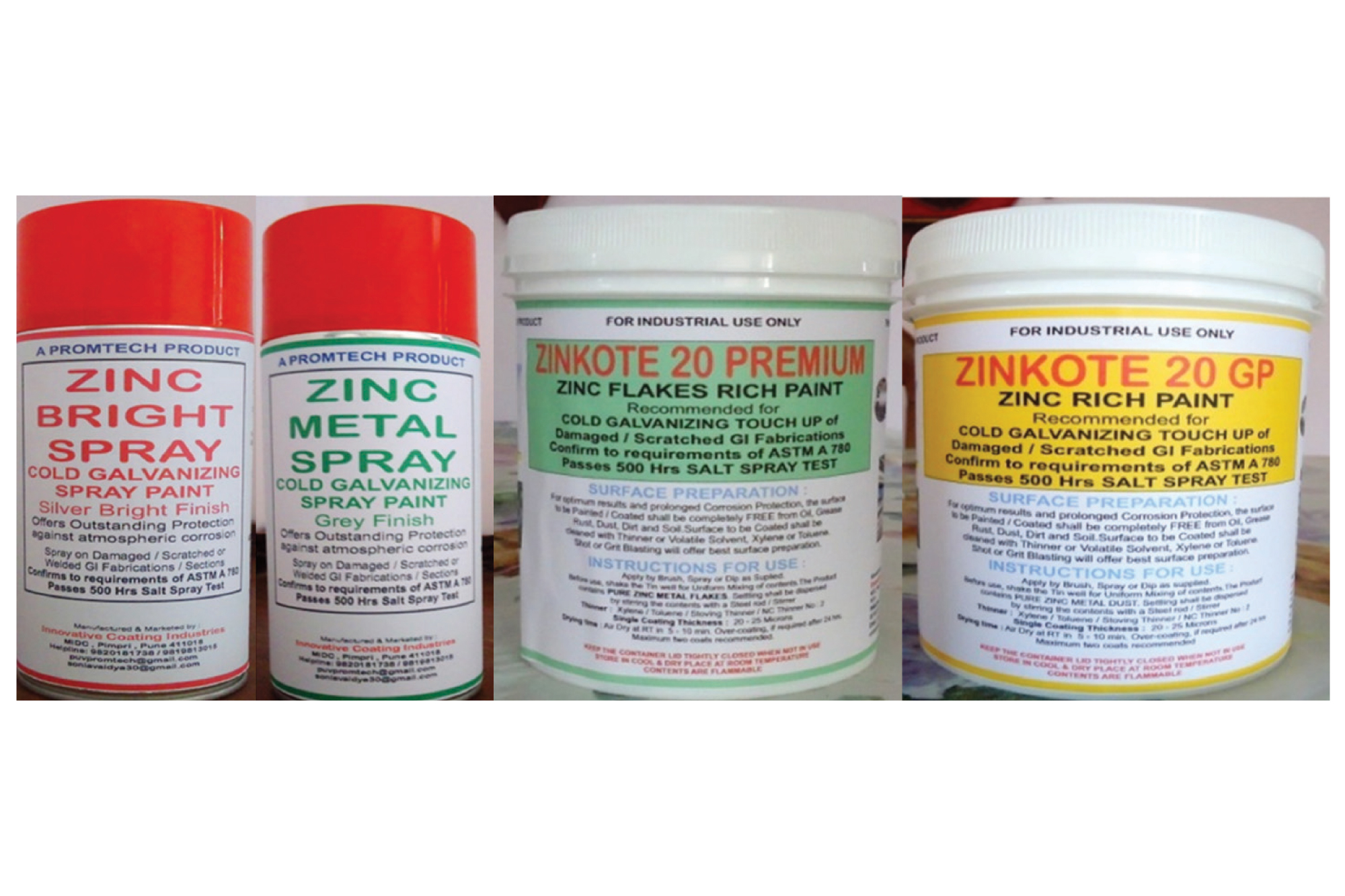
For damaged galvanising, corroded and welded galvanised surfaces, cold galvanising by Zinc metal spray is offered by Promtech
The reason for the extensive use of hot dip galvanising is the two-fold nature of the coating. As a barrier coating, it provides a tough, metallurgically bonded zinc coating, which completely covers the steel surface and seals the same from the corrosive action of the environment. Additionally sacrificial action of zinc protects steel even where damage or minor discontinuity occurs in the coating.
How zinc protects steel from corrosion
Zinc forms a metallurgical bond with mild steel. Zinc coating has good impact and abrasion resistance. Zinc spray offers corner and edge protection. Zinc metal spray offers satisfactory corrosion performance in sea water and salt spray testing an in saline atmosphere.
For damaged galvanising, corroded and welded galvanised surfaces, cold galvanising by Zinc metal spray is an ideal cure. This quick drying, high solids coating provides good protection to steel and ferrous metals against harsh corrosive environments.
Zinc metal spray is an acrylated epoxy solvent deposited coating which fuses to metal substrates to guard against corrosion. This coating constantly fights against rust and corrosion. It is highly resistant to salt water corrosion, does not sag and may be top-coated with conventional primers, paints and epoxies. Cold galvanising spray provides the protection of hot-dip galvanising plus the convenience of on the job aerosol application.
Characteristics
Zinc metal spray has electrochemical bond, quick drying, needs minimum surface preparation. It offers easy and user-friendly application for pre-despatch inspection stages and on-site use for touch-up. It stops rust and corrosion on any iron and mild steel surface.Zinc metal spray can be applied over wide range of temperatures and humidity, and also reduces maintenance costs.
Physical and chemical standards
• Zinc contents: up to 35 to 40 per cent in the formulation
• Purity of zinc: 99 per cent pure spray dried
• Zinc contents in the DFT : 88 – 92 per cent
• Colour: greyish and silver finish available
• Film thickness: 20 – 25 microns by one coat
• Salt spray life: over 500 hrs of fog chamber salt spray test
• Touch dry time: 3-5 min, Overcoating time: 30 min, Hard dry time: 24 hrs, Can shelf life: 1 year
• Storage conditions: Store the aerosol spray cans in a cool, dry place in cupboard/closed shelf, under 45 C.
Applications
• Structural steel bridges/dams/ transmission and telecommunication line towers/antennas
• Railway transmission lines, electric poles, high rise masts, stairs, railings and water drain pipes
• Nuclear, thermal and hydro power generation plants and equipment, wing mill power equipment
• Marine applications, aircrafts, ships, naval and sea going vessels, road crash barriers and railings
• Water pipelines, water treatment and effluent treatment plants and equipment, nuts and bolts
• Damaged and welded galvanised steel structures metal equipment, cable trays, hvac equipment.
Surface preparation
Surfaces to be coated must be clean, dry and totally free of dust and burnt carbon. Wipe the surface with solvent / thinner (for removal of oil
and grease) followed by wire brushing / grinding.
Cookie Consent
We use cookies to personalize your experience. By continuing to visit this website you agree to our Terms & Conditions, Privacy Policy and Cookie Policy.