Rebar Fusion Bonded Epoxy Coating Plant
By Edit Team | July 16, 2018 12:39 pm SHARE
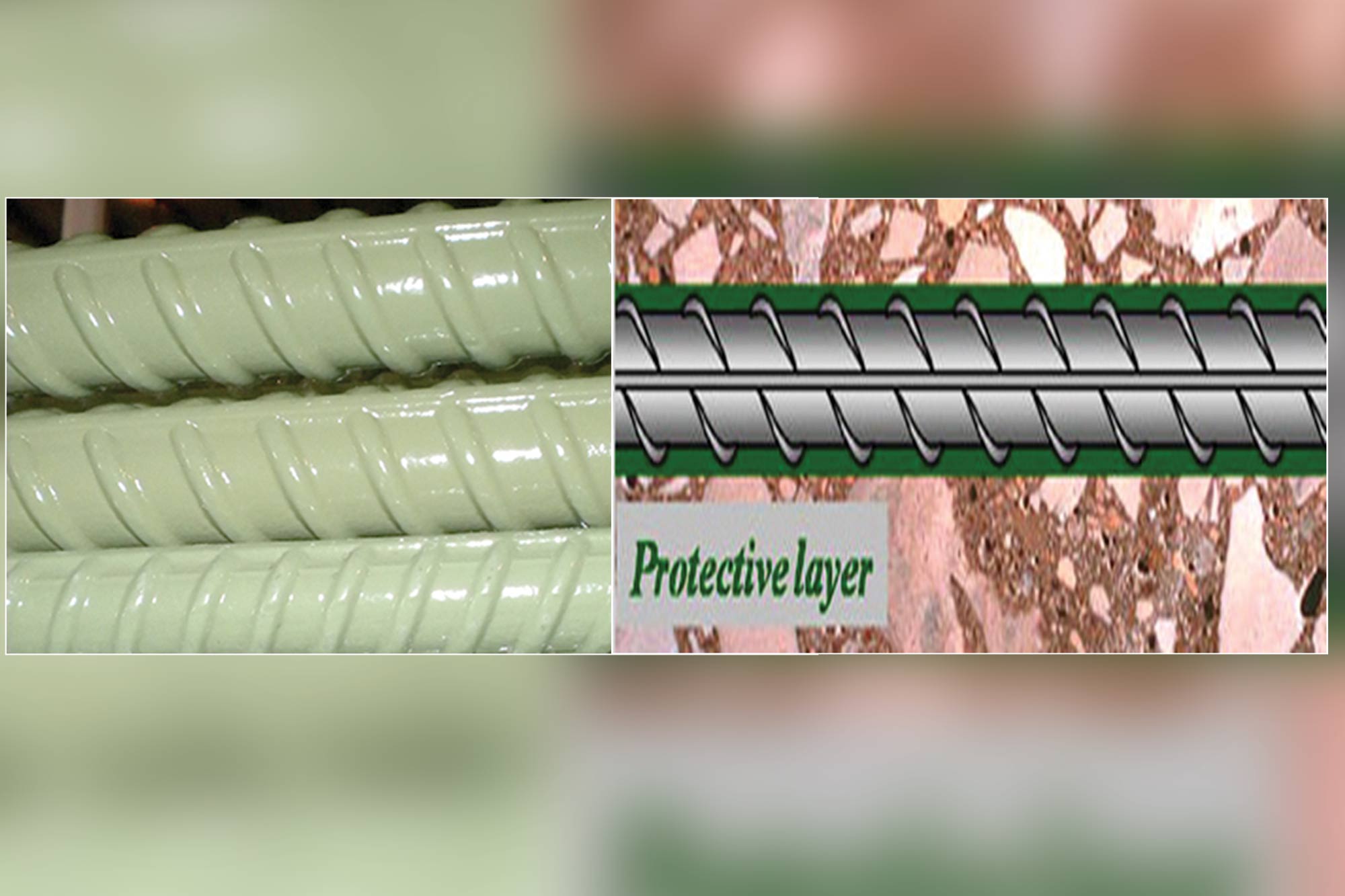
Fusion-bonded epoxy coating, also known as fusion-bond epoxy powder coating and commonly referred to as FBE coating, is an epoxy-based powder coating that is widely used to protect concrete reinforcing bars (rebar). FBE coatings are thermoset polymer coatings. The name fusion-bond epoxy is due to resin cross-linking and the application method, which is different from a conventional paint. The resin and hardener components in the dry powder FBE stock remain un-reacted at normal storage conditions.
At typical coating application temperatures, usually in the range of 180 to 250 C (356 to 482 F), the contents of the powder melt and transform to a liquid form. The liquid FBE film wets and flows onto the steel surface on which it is applied, and soon becomes a solid coating by chemical cross-linking, assisted by heat. This process is known as “fusion bonding”. The chemical cross-linking reaction taking place in this case is irreversible. Once the curing takes place, the coating cannot be returned to its original form by any means. Application of further heating will not “melt” the coating and thus it is known as a thermoset coating.
Fusion-bonded epoxy coating application process
Regardless of the shape and type of steel surface to be coated, the FBE powder coating application has six essential stages as mentioned below:
Surface preparation — airless (wheel blast) shot blasting process
Shot Blast cleaning is the most commonly used method for preparation of steel surfaces. This effectively removes rust, scale, slats, and makes surface rough (rough surface is called profile). Profile increases the effective surface area of the steel. The cleanliness achieved is assessed to by Swedish standard from a set of photographic slides in Swedish standard (SIS) showing examples of the common terminology of white-metal, near white-metal, etc. Typically, SA two-and-a-half is used for pipelines (equivalent to NACE N2).
It is important to remove grease or oil contamination prior to blast cleaning. Solvent cleaning, burn-off, etc., are commonly used for this purpose. In the blast cleaning process, a blasting wheel uses centrifugal force to propel the abrasive against rebar in controlled direction, speed and quantity. The equipment is equipped with four blast wheels. Two blast wheels are mounted on the top of the cabinet and positioned above the pass line of the work and the other two-blast wheels are mounted in the bottom of the cabinet positioned below the pass line of the rebar.
Pre Heating – induction Heating
Heating can be achieved by using several methods, but the most commonly used ones are ‘’induction heating’’. Induction heating is the process of heating an electrically conducting object (usually a metal) by electromagnetic induction, where eddy currents are generated within the metal and resistance leads to Joule heating of the metal. An induction heater (for any process) consists of an electromagnet, through which a high-frequency alternating current (AC) is passed. Heat may also be generated by magnetic hysteresis losses in materials that have significant relative permeability. The frequency of AC used depends on the object size, material type, coupling (between the work coil and the object to be heated) and the penetration depth.
The steel part is passed through a high frequency alternating current magnetic field, which heats the metal part to the required FBE coating application temperature. Typical application temperature for a standalone FBE is 225 to 245C. When used as a primer in a multi-layer polyolifine system, application temperature may be dropped based on FBE manufacturer’s recommendations, in order to meet the “inter-coat adhesion” parameters.
Fusion-bonded epoxy coating
The FBE powder is placed on a “fluidisation bed”. In a fluidisation bed, the powder particles are suspended in a stream of air, in which the powder will “behave” like a fluid. Once the air supply is turned off, the powder will remain in its original form. The fluidised powder is sprayed onto the hot substrate using suitable spray guns. An electrostatic spray gun incorporates an ionizer electrode on it, which gives the powder particles a positive electric charge.
The steel to be coated is passed through the powder stream on conveyor. The charged powder particles uniformly wrap around the substrate, and melts into a liquid form. The molten powder ‘flows’ into the profile and bonds with the steel. The molten powder will become a solid coating, when the ‘gel time’ is over, which usually occurs within few seconds after coating application. The resin part of coating will undergo cross-linking, which is known as “curing” under the hot condition. Complete curing is achieved depending on the FBE coating system; full cure can be achieved in less than one minute.
Curing
The molten powder becomes a solid coating, when the ‘gel time’ is over, which usually occurs within few seconds after coating application. The resin part of coating undergoes cross linking, which is known as ‘curing’ under the hot condition. Complete curing is achieved either by the residual heat on the steel, or by the help of additional heating sources. Depending on the FBE coating system, full cure can be achieved in less than one minute to a few minutes in case of long cure FBE’s. During curing time the coating gets hardens to a solid.
Water quenching
The coated bars after curing are passed through a water tunnel. Water is sprayed on to the bars to cool them.
Holiday testing
Once the rebar has passed through the cooling tank, it is tested with a holiday detection device that electrically examines the rebar for minute cracks or pinholes in the coating. If a holiday is detected, the area is marked for easy identification during the touch-up procedure. The rebars are conveyed from the holiday detection device to a rack area where the holidays are touched up. After the rebar are repaired, they are bundled and readied for shipment.
Advantages of FBE coating
• FBE coating on reinforcement bars has the following advantages.
• Since the coating is done on the coating lines, better quality control is achieved. The process gives uniform coating thickness.
• There is good bonding of coating with the steel as FBE has very good adhesive properties.
• Because of flexibility, the coating does not get damaged when the straight bar is bent during fabrication on a special mandrill.
• FBE coating acts as insulator for electro chemical cells and offer barrier protection to steel which prevents chloride ions through it.
• There are well established criteria for acceptance for FBE coating in different standards.
• FBE coated reinforcement bars provide the most effective corrosion protection to the reinforcement bars.
• Unlike many paints, the fusion-bonded epoxy coatings used for steel reinforcement do not contain appreciable solvents or other environmentally hazardous substances.
• Applying an epoxy coating plays a role of electrochemical and a physical barrier, and prevents oxygen and chlorides from reaching the steel surface reducing corrosion.
Authored by
Nilesh Vaja (Manager Sales)
Patel Furnace & Forging Pvt Ltd (Shot Blasting Division)
Cookie Consent
We use cookies to personalize your experience. By continuing to visit this website you agree to our Terms & Conditions, Privacy Policy and Cookie Policy.