Recent success stories of CLOOS India
By Staff Report | November 25, 2024 12:00 pm SHARE
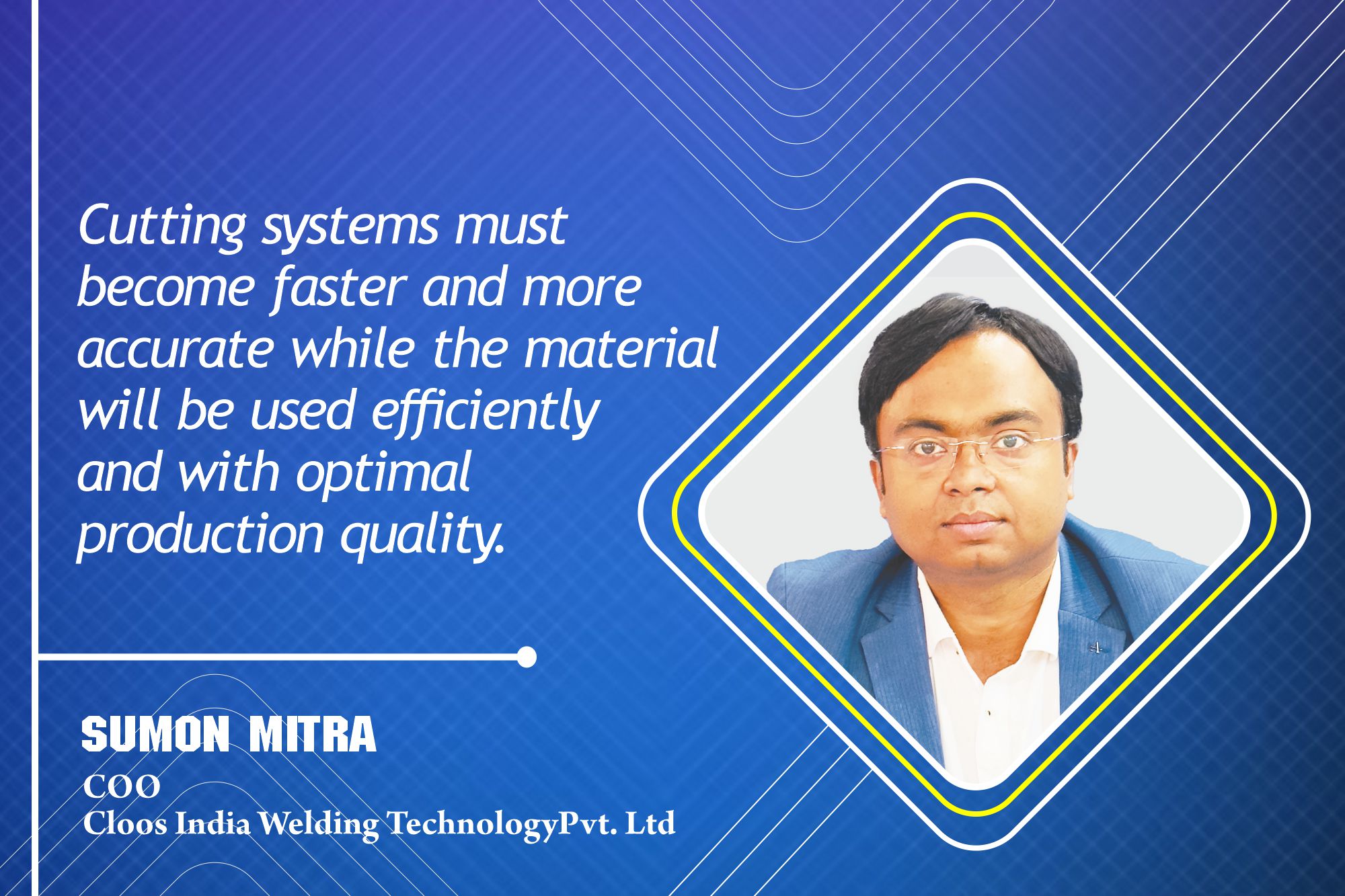
CLOOS’s customised single-source welding technology solution has been redefining the industry for a decade. Sumon Mitra, COO of Cloos India Welding Technology, affirms that CLOOS is at the forefront of innovation with its comprehensive solutions.
Cloos successfully installed a robotic welding and cutting solution for Larsen & Toubro’s crusher rotor. Cutting technologies play an essential part in modern manufacturing. As with welding, the need for it is steadily expanding. Cutting systems must become faster and more accurate. The machining time for a component will be reduced, while the material will be used efficiently and with optimal production quality. At the same time, usability, production dependability, and energy efficiency are critical. Innovative cutting technologies are in high demand to meet rising efficiency and quality standards. When choosing a cutting system, it is critical to ensure it is precisely suited to the task at hand and consider future projects.
CLOOS provided Larsen & Toubro Robotic with a cutting solution that included an automatic tool changer, addressing the issue of manual cutting quality and time. Oxy-fuel flame cutting was used to cut a star plate with a thickness ranging from 80 to 120 mm. On average, adopting robot technology for cutting reduces manufacturing costs by 25 to 30 percent while significantly improving quality. Cloos provides the best machining technology for any welding and cutting application.
CLOOS welding solution
Larsen & Toubro rely on CLOOS as a single source provider for welding the crusher rotor, which entirely transforms their three-stage welding process. They also benefit from CLOOS Tandem Weld technology, which provides maximal deposition with less heat input and an automatic tool changer for critical welding seams using a single torch.
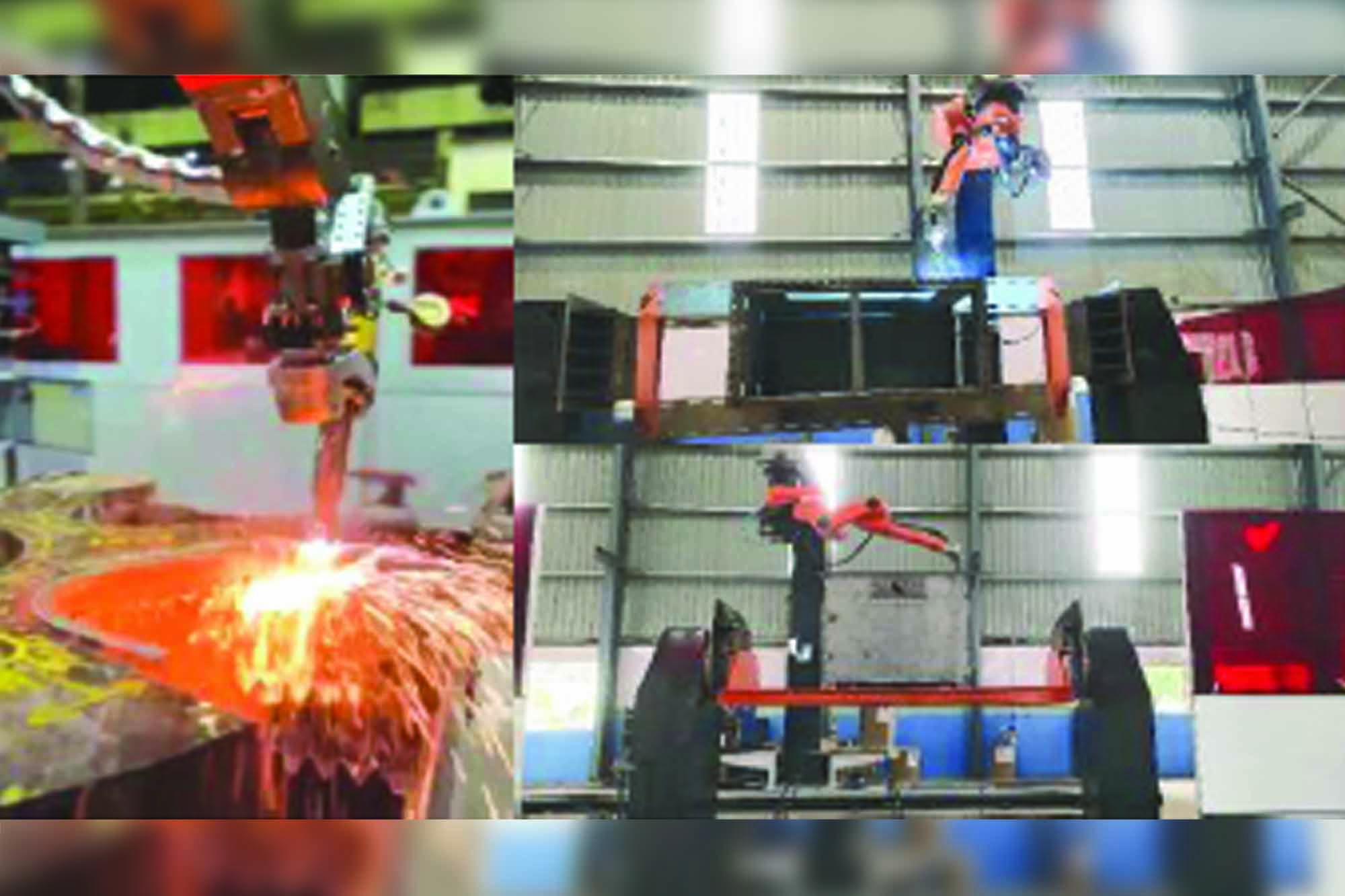
Transformer tank welding at Crompton Greaves
CLOOS successfully implemented a robot welding solution for transformer welding at Crompton Greaves. Cloos has long provided robotic welding solutions to the transformer industry. Crompton Greaves relies on Carl Cloos Schweisstechnik GmbH for transformer tank welding competence. The new welding system is about 22 meters long and consists of two stations and a Cloos 7-axis robot (QIROX QRC-410-E). It enables flexible processing of various components, improving the efficiency and quality of hall manufacturing.
If you wish to modify your current Transformer tank subassembly and full assembly welding process, count on CLOOS’s superior welding technology and tailored Robotic welding solution, backed by their 105 years of experience!
Speed Weld
CLOOS stable all-round Innovative welding process Speed Weld completely changed welding quality in the many sectors’ low- or high-capacity range. Speed welding is employed in every aspect of metal machining. The voltage-controlled MIG/MAG pulsed arc method allows for extremely high arc pressure even under extreme conditions. The intense arc in Speed Weld allows you to achieve high welding speeds. It provides exceptional weld quality due to the deep penetration. Users can avoid significant reworks because spatters and undercuts are low.
Benefits:
• High welding speeds due to the powerful arc
• Excellent welding quality because of a deep penetration
• Reduced rework thanks to the pulsed arc technology with regulated drop separation.
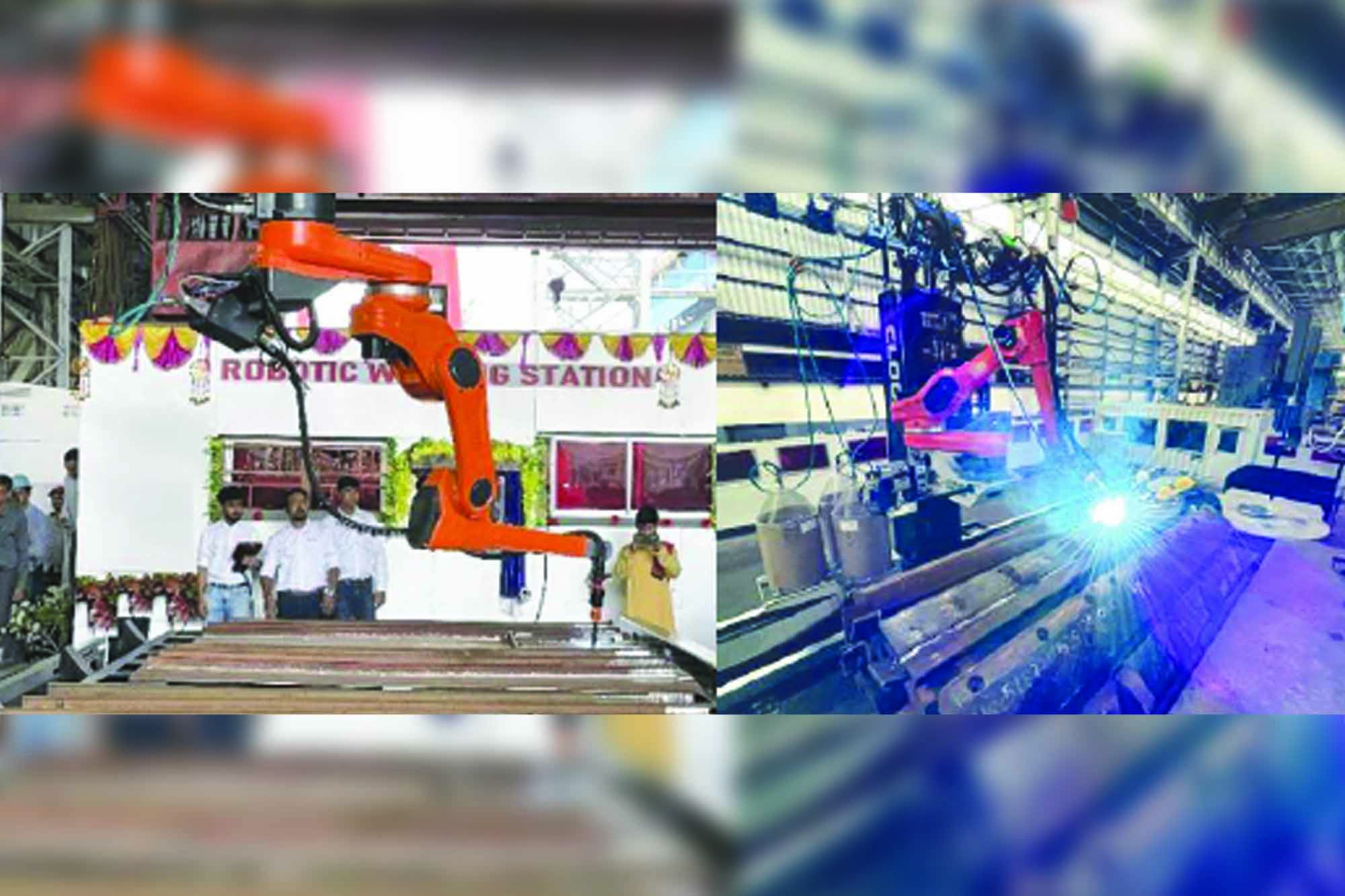
The benefit of CLOOS Arc Seam Tracking
The sensor precisely measures the torch’s position relative to the specified path during welding. This allows for automated adjustment in the event of any discrepancies, resulting in constant, high-quality welding. Because measuring and welding occur simultaneously with the arc sensor, time loss is minimal. At the same time, workpiece distortion, such as from thermal expansion, is directly adjusted for. The CLOOS arc sensor, therefore, combines productivity with high quality.
The first robotic welding system in the Indian shipping industry
GRSE trusted CLOOS and installed the first robotic welding system in the Indian shipping industry. CLOOS’ offline Roboplan software solves the problem of non-repetitive ship panel welding. Using the TEACH procedure takes less time than developing a new program in the robot system. As a result, system utilisation increases, the manufacturing process is streamlined, and welding production becomes more adaptable.
Cloos successfully welded Radiators, PF condenser Charge Air coler, and Barplate radiators by Cloos innovative welding process Cold weld.
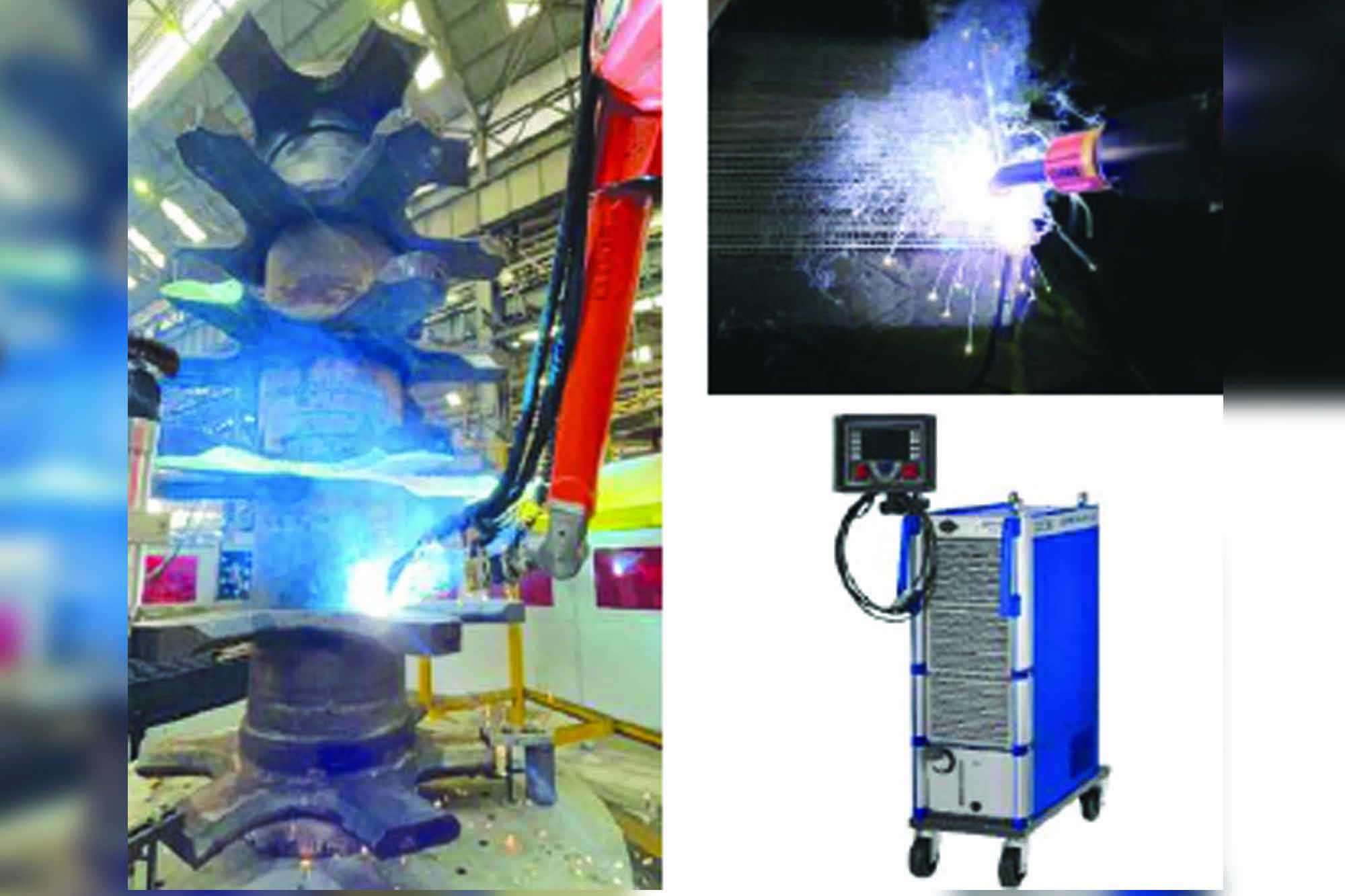
CLOOS This achieve excellent results when welding challenging materials using the directionally stable MIG/MAG AC pulsed arc. Cold Weld combines a pulsed arc with AC technology. Due to the adjustable AC part you can individually control the heat input into the component. Cold Weld enables higher welding speeds by increasing the deposition rate while maintaining an optimal heat input, which positively impacts the component and material characteristics. The reduced heat input preserves the original material properties, minimising distortion and the need for extensive rework. Additionally, Cold Weld can compensate for material tolerances thanks to its excellent gap-bridging ability.
Contact:
Cloos India Welding Technology Private Limited
Ground & 1st Floor,Plot No. 114/1/3,
General Block, Midc Bhosari, Pune,
Maharashtra 411026 India
Website:- http://www.cloos.de
Email :- contact@cloos.in,
Mobile:-7003545907 / 9168383939
Cookie Consent
We use cookies to personalize your experience. By continuing to visit this website you agree to our Terms & Conditions, Privacy Policy and Cookie Policy.