Reducing OPEX by 85 percent in the 5th Stage of ZLD Process
By Edit Team | December 15, 2021 5:19 pm SHARE
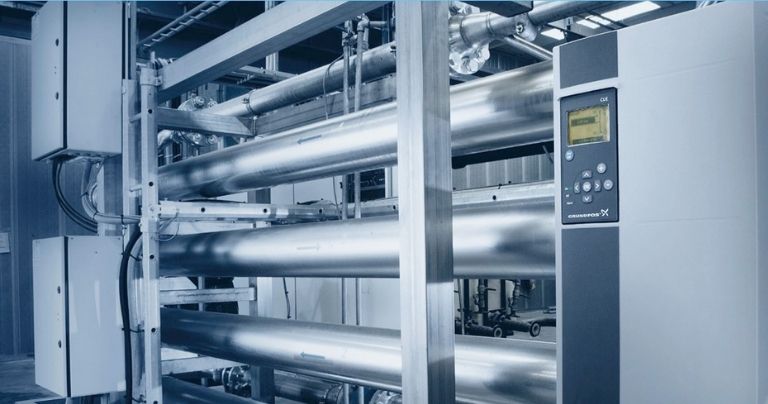
Uninterrupted operations in the fifth stage of RO process for the ZLD plant with Grundfos wastewater technology.
The situation
The textile industry in India uses 1,608 MLD (million litres per day) of water everyday for its industrial processes. Due to India’s regulation on the use of water, many textile companies have begun to embrace global best practices such as Zero Liquid Discharge (ZLD) to reuse their process water and reduce water footprint. However, the ZLD process has higher OPEX due to the process of ‘Mechanical Vapor Recompression Evaporation’ (MVRE) which has a high energy requirement.
This MVRE process is critical to increase the water concentration before the final salt recovery after the fourth stage of the Reverse Osmosis (RO) in ZLD. A leading textile company in the southern part of India was looking out for 5th stage RO as an alternative for MVRE to reduce the overall OPEX in ZLD process.
The solution
To reduce the energy foot-print of the ZLD plant, the customer replaced a less efficient MVRE process with a more robust 5th stage RO in their plant, which requires high-pressure pumps and membranes with operating pressures up to 80 bar.
Grundfos new BMSHS pumps are the perfect fit for this high-pressure application in the 5th stage RO process. This BMSHS solution can manage pressure up to 82.7 bar efficiently and with the use of permanent magnet motor technology, the entire solution is compact, efficient and needs less footprint.
Grundfos offered BMSHS and BM pumps with MPC controller to ensure automatic operation with safety interlocks, eliminating the need for any manual interventions.
Pump specification:
FlowPre: Up to 30 m3/hour
Pressure: 80 bar
Pump Model: BMS 17-22HS, 85 kW & BM17-40R, 22kW
The outcome
Grundfos solution significantly cut down the OPEX of the 5th stage RO of the ZLD plant by up to 85 percent. Grundfos’ reliable BM and BMS pumps ensured uninterrupted operations in the fifth stage of the RO process for the ZLD plant.
Grundfos MPC controller and variable-frequency drive connected with a communication module ensures that the pressure, flow, and speed are optimally managed for varying process requirements. Further, this MPC controller enables automatic operations and ensures that the safety precautions for pumps are in place while delivering process requirements seamlessly.
Benefits of Grundfos BMS & BM range of boosters with MPC controllers
Maximum efficiency: A permanent magnet motor is the secret behind the improved efficiency of the BMS high-speed range. This high-speed motor in BMShs range also offers a smaller footprint and drastically reduces the weight of the pump.
High durability
All wetted components are made of super duplex stainless steel resulting in high durability. The Grundfos BMS HS range has been put through rigorous tests, to ensure maximum process reliability.
Less Opex
Grundfos’ BMSHS solution has brought down the OPEX of the 5th stage RO of this ZLD process by up to 85 percent.
Package Solutions
Grundfos MPC controllers with BM and BMSHS pumps offered as a package solution to this 5th stage RO process ensures complete process automation and safety.
Cookie Consent
We use cookies to personalize your experience. By continuing to visit this website you agree to our Terms & Conditions, Privacy Policy and Cookie Policy.