Repair and rehabilitation add strength, longevity to construction
By Edit Team | April 16, 2019 10:57 am SHARE
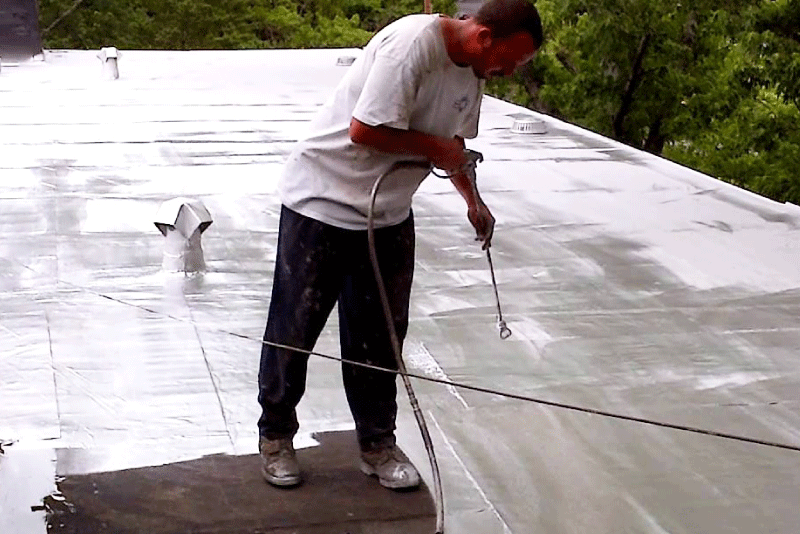
Establishing nature, extent of damage and identifying the cause of a structure’s deterioration, entails correct assessment.
The present uptrend in demand can be attributed to a rising volume of infrastructure rehabilitation projects in the transport, water management and energy sectors. India is witnessing high demand for new infrastructure, however, maintaining the existing infrastructure and improvement is equally crucial.
Proper selection of repair material
Deterioration of concrete mainly happens due to corrosion in reinforcing steel, structural damage, water infiltration, seismic impact etc. Industry experts estimate that the cost of corrosion of infrastructure in India is over `2 trillion per annum. Losses can be pared by awareness on corrosion management and life cycle improvement of structures by proper selection of repair material and process, says Pushpam Kumar, National Manager – Refurbishment, Sika India Pvt Ltd.
In new construction after cement hydration, the concrete forms an alkaline environment and protects reinforcing steel from corrosion. Its alkalinity provides a pH of between 12.5~13.5. Reinforcing steel gains a hard surface due to this alkaline condition which consists of a passive layer of iron oxides.
Adding life to structures
Repair and rehabilitation are significant for adding life to structures that have notably deteriorated, but cannot be dismantled due to cost considerations. Waterproofing too plays an important role in repair as it forms the protective barrier to enhance the life of repair.
Tremco adds value to the segment by providing high-tech solutions with tremendously long life as well as quick and easy application.
“TREMproof Waterproofing Systems, Vulkem Traffic Resistant Systems, Dymonic Sealants and AlphaGuard Roof Coatings all ensure that the repaired structure can be brought back into service in a very short time, sometimes within a couple of days after casting,” says Sunny Surlaker, Marketing Manager, Tremco India Private Limited.
Versatility of concrete
Mouldability and durability make concrete versatile making its usage attractive in varied exposure conditions. Vulnerability of concrete to deterioration has always been a cause of deep concern, says Er. Sujit Kumar Kar, Head Specification & Marketing, MC-Bauchemie (India) Pvt Ltd.
Generally, the process of deterioration begins almost immediately after the casting. Considering a mix of complicated construction, quick completion deadlines, speed of construction and economy, it becomes virtually impossible to cast specified cover to reinforcement. The outermost layer of concrete therefore becomes the weakest one. If formworks are not impermeable and slump of concrete is not adequate, the cement paste does not cover the reinforcement optimally to render it passive to corrosion. This facilitates deterioration and the subsequent need for repairs.
Identifying root cause
Successful repair activity of any infrastructure depends on identifying the root cause of deterioration. Repairs can be done for improving strength and durability, thus extending the structure’s life, says Dinesh Chavan, G M – Operations, Choksey Chemicals Pvt Ltd. The processes of restoring the structure to service level, once it had and now lost, strengthening consists in achieving the structure with a service level, higher than that initially planned by altering the structure not necessarily defective area.
Durability of concrete
Concrete’s ability to resist weathering action, chemical attack, and abrasion while maintaining its desired engineering properties depends on the exposures environment and properties desired, says Vijesh Lal, Manager – Projects & Specifications, Cera-Chem Pvt Ltd.
Concrete construction is generally expected to give free service throughout its design life. However, these hopes are not met in many constructions. This is attributed to the reasons like structural deficiency, low quality materials, unanticipated overloading or physical damage and pollution of our atmosphere with toxic gases etc. This is when repair and rehabilitation plays a major role in enhancing the durability of structures.
The objective of any repair should be to produce rehabilitation – which means a repair carried out relatively low cost, with a limited and predictable degree of change with time and without premature deterioration and or distress throughout its intended life and purpose. To achieve this goal, it is necessary to consider the factors affecting the durability of a repaired structural system as part of a whole, or a component of composite system. These can be grouped into three categories such as durable repair design, durable repair application and evaluation of the repairs.
Durability of a structure can be increased with the help of repair materials like special concretes and mortar (CeraMicroconcrete, CeraFibrecrete), admixtures (CeraGuniteRapidset, CeraHyperplast XR W40), special elements for accelerated strength gain (Cera Carbon Fibre Wrap System), expansive grout (Cera Grout 40), polymer mortars (CeraPolymortar), rust eliminators (Cera Rust Remover, Cera Rust Converter), corrosion inhibitors (Ceraplast CI 100, Cera Cote SP CI), zinc rich primers (Cera Zinc ZR), anti-carbonationcoating (CeraInfraguard WA), epoxy injection (Cera Screed EPLV Injectable) and repair of cracks (CeraSilicoConstro).
Restoration of structure
Being the technical aspect of rehabilitation, repair is returning to healthy conditions of concrete structure and renovation or restoration with creative application of scientific principles. “Repair restores the structure and is used to modify a structure to meet new functional and other requirements, says Puneet Kakroo, Business Head, Fibrex Construction Chemicals Pvt Ltd.
Determining the origin of distress, removing damaged materials and causes of distress, as well as selecting and applying appropriate repair materials extend a structure’s life. The effects of strengthening or removing part or all of structural element must be analysed carefully to determine their influence on the structure’s global behaviour.
Good slopes and effective drainage prevent water from ponding and application of waterproofing treatment, thereby preventing water absorption. Structure design should accentuate water-shedding characteristics for vertical elements and incorporate slopes and drain holes for such horizontal elements as deck,” says Hasan Rizvi, Sr. Vice President, STP Ltd.
Buying high-quality chemicals
Sika in accordance with European Standard EN – 1504 suggest 5 key stages in concrete repair and rehabilitation are assessment of the structure by visual observation or by laboratory test to identify the cause and determine the effects and consequences, diagnose cause of deterioration to control further damage, options and objectives of repair to restore structural integrity, improve durability, repair the defect and improve appearance of the structure, selection of appropriate repair method – patch repair, pouring or spray application and quality material. The surface preparation, application and quality control procedure for the repair works should be carried out in accordance with the recommendations as per EN 1504 and maintain complete records of all the materials used in the works for future reference and maintenance plan based on anticipated new life expectancy of the structure, says Kumar.
Whenever there is a need for structural strengthening due to excessive corrosion or due to an increase in the structural load bearing capacity of structure, carbon or glass fibre reinforced polymer (SikaWrap), carbon laminates (Sika Carbodur), structural grade adhesive and epoxy injections (Sikadur) can be adopted as externally bonded reinforcement (EBR) with minimal destruction to existing structure and its occupants without adding any major weight to the parent structure.
Selection of right products
Performance, durability and sustainability should be the important considerations in selection of right products for corrosion control and repair. In financial terms, it is better to consider life-cycle cost of the materials rather than initial cost, in order to ensure maximum cost benefits over life of the structure, says Surlaker.
Corrosion-wise, Alumanation 301 has set the sustainable standard in metal protection for over 60 years. A high-solids, asphaltic, asbestos-free coating, Alumanation uses advanced fibre reinforcement technology, to protect and reinforce corroded metallic substrates. Once coated surfaces do not rust, provide seamless waterproofing and reduce temperatures within the coated structures. This provides durability, energy savings and sustainability in the repair of metal structures.
There would be many other such factors governing selection criteria. It also helps to evaluate the sustainability of the material as part of the construction system and not merely the material itself. For e.g. certain coatings may be made from virgin materials, but the durability and protection they provide, would end up making the construction system sustainable.
Fast and cost-efficient implementation
Our cement-bound corrosion protection coatings offer short application times, ensuring fast and cost-efficient implementation of the entire concrete repair project. MC bonding coats not only improve the adhesion of ageing concrete, they are also suitable for horizontal, vertical and overhead working, ideally formulated to meet a wide range of building requirements, says Sujit.
With the concrete replacement systems from MC, no task is too great. Whether for manual trowelling or spray application on a horizontal, vertical or overhead surface, for corrosion protection, for composite bonding or even fire protection of the reinforcement, the company offer the ideal solution. One can seal pores, pitting and blowholes, smooth rough areas and provide full-surface finishes using the fine fillers and mortars, based on cement, ECC (engineered cement composites) or dispersion technology. No two concrete structures are the same, and this is also true when it comes to the consistency of ageing concrete. Concrete repair work has to take into account various structure-related requirements, including strength class, modulus of elasticity and other variables. The European repair standard EN 1504 Part 3 groups’ concrete replacement materials into classes R1 to R4 that reflect conditions typical to certain structures and substrates.
Correct assessment a must
Mainly depends on the many factors namely, condition of structure, nature of damage accrued, ease of work to do and specifications specified in BOQ, requirement of mechanical properties, durability span and budget, says Chavan. A faulty diagnosis may lead to improper selection of materials and repair techniques leading to the failure of the repaired zone again. It may also be necessary that the serviceability of the structure is checked after carrying out the necessary repairs.
Ease of application
Selection criteria in buying the chemicals should consist of ease of application, chemical reaction with concrete, life of product once used in concrete, history of product performance. Basically the need of repair rehabilitations of structures can arise from any of the following:
Selection and assessment of site; assessment of environment; design consideration; choice of materials; design mix; proper workmanship and quality control; protection and protective treatments; role of inspection and testing; proper maintenance and timely repair.
Effective corrosion inhibitors
Concrete additives like corrosion inhibitors should preferably be bipolar. Corrosion is mainly due to CO2 entering in concrete and Cl ion present in water. “Corrosion inhibiting admixture material should give a dense concrete, thus preventing, ingress of aggressive gases in concrete and prevent damage due to Cl ion on steel. Apart from this during rehab, the epoxy boding material should be water insensitive, so that it can be sued in wet conditions during rehab, says Rizvi.
Losses can be pared by awareness on corrosion management and life cycle improvement of structures by proper selection of repair material.
Pushpam Kumar, National Manager – Refurbishment, Sika India Pvt Ltd
Successful repair activity of any infrastructure depends on the identifying the root cause of the concrete structure’s deterioration.
Dinesh Chavan, G M – Operations, Choksey Chemicals Pvt Ltd
Performance, durability and sustainability should be the important considerations in selection of right products for corrosion control and repair.
Sunny Surlaker, Marketing Manager, Tremco India Private Limited
MC bonding coats not only improve the adhesion of ageing concrete, they are also suitable for horizontal, vertical and overhead working.
Er. Sujit Kumar Kar, Head Specification & Marketing, MC-Bauchemie (India) Pvt Ltd
Different concretes require different degrees of durability depending on the exposures environment and properties desired.
Vijesh Lal, Manager – Projects & Specifications, Cera-Chem Pvt Ltd
Repair restores the structure and is used to modify a structure to meet new functional and other requirements.
Puneet Kakroo, Business Head, Fibrex Construction Chemicals Pvt Ltd
Corrosion inhibiting admixture material should give a dense concrete, thus preventing ingress of aggressive gases and damage.
Hasan Rizvi, Sr. Vice President, STP Ltd
Cookie Consent
We use cookies to personalize your experience. By continuing to visit this website you agree to our Terms & Conditions, Privacy Policy and Cookie Policy.