Road potential in India springs economic prospects
By Edit Team | February 23, 2019 5:09 am SHARE
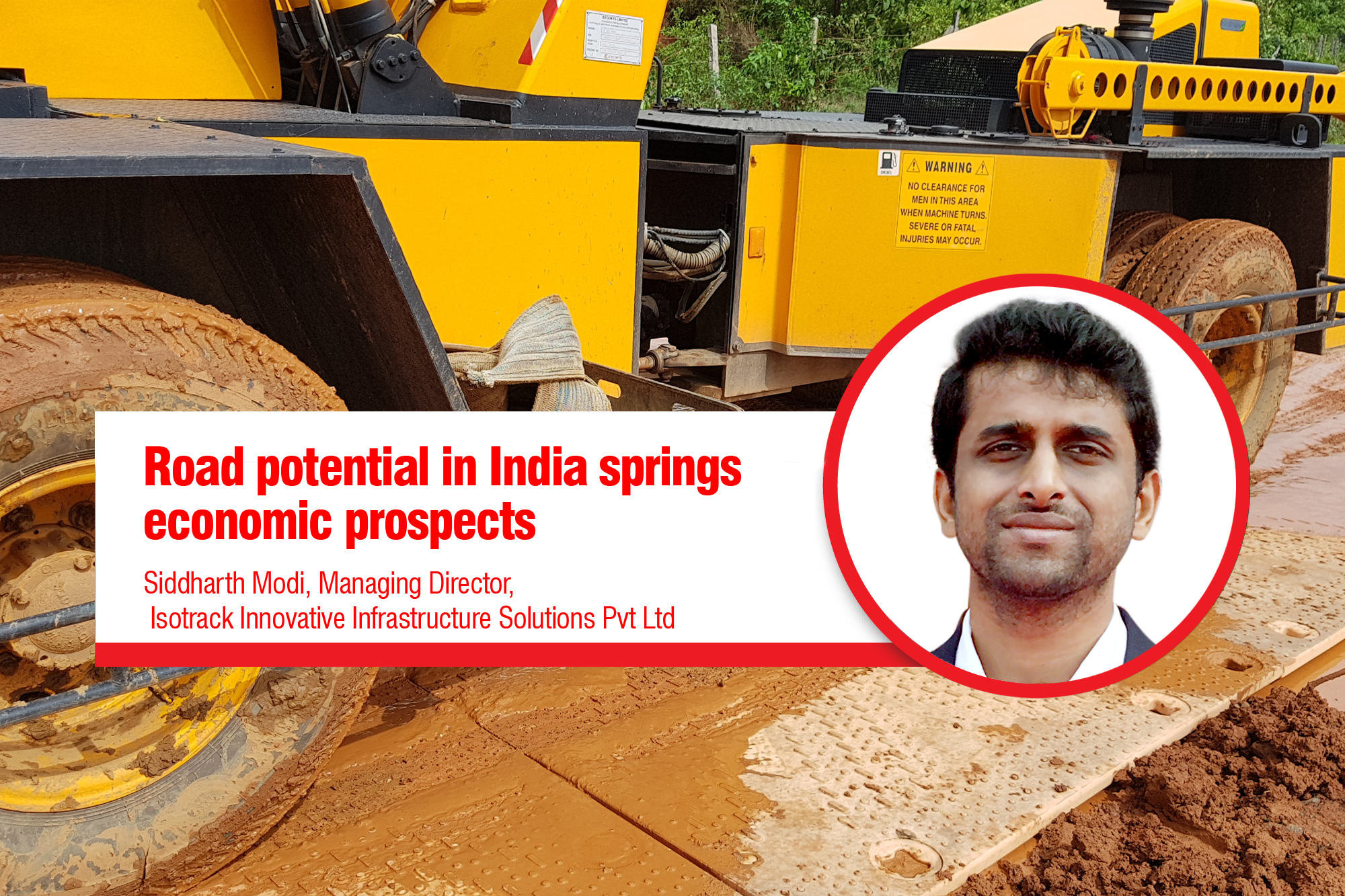
Isotrack caters with ground matting solution to the industries that are engaged in heavy equipment moving. Their X-Series mats simplify work in sludge situation and improve efficiency, says Managing Director, Siddharth Modi.
Please talk about your latest innovation.
Our star product is the X-series mats that are made of high density polyethylene through compression moulding. This is useful for remote locations where soil conditions are difficult for accessing or working using heavy machinery like cranes and vehicles transporting construction material. By using the mat, people can utilise their equipment for longer period during the year and work much faster than they would. But, globally, industries like oil and gas, power transmission and distribution tower, railway and road construction are involved in lot of heavy equipment moving to remote locations that barely has permanent infrastructure for these machines to access.
What kind of material it is made of?
The X series mats are made of virgin high density polyethylene that is compression moulded under high heat conditions. It has a hollow core filled with foam to prevent water ingress, thereby, increasing the weight, if the mat is punctured during rough
conditions. Secondly, the overall density is lighter than water, making it float on water as well.
What kind of life does it have?
While the mats last for 15-20 years, it majorly depends on the handling. These are rough usage materials designed to withstand a lot of wear and tear. But, if used properly, they can last for over 20 years.
How cost efficient is this material as compared to traditional surface preparation?
This kind of material can reduce costs by as much as 90-95 per cent, but it varies depending on the project’s length since this is an infrastructure equipment. Hence, our biggest sector is oil and gas where there are drilling rigs active throughout the year in very remote locations. Depending on the case, we’ve seen cost reductions of up to 90 per cent, because earlier people had a lot of idle machinery. We calculate on the basis of machine utilisation and how much lesser labour and time are required because you no longer require a lot of people to bring soil from other places and lay down a road from scratch.
What is a breaking point in this surface?
We are accredited by European universities and most of the strength tests were done there. The X-Series mats can bear 415 tonnes per sq. m of compression strength.
Inherently, the mat is very strong with usable area per mat being 6.84 sq. m. Its main application is to transfer the load to the ground beneath. They have a special proprietary connection technology through which mats can be connected in multiple configuration. They will distribute the load of a heavy machinery through a larger surface area reducing the load transmitted to the ground. So that the soil itself will not sink and the machinery can work safely on the surface of mat.
What would be the approximate costing per mat?
We don’t really share the costing given that the product as such as the concept itself is new. So, we go to the client site, prepare cost benefit analysis of how many mats they need, and the solution they’re using, how much they can save if they use the mats and then based on those savings, the costing is presented. It is necessary to present potential savings to customers while offering new products, because if costing is presented straight off, customers won’t be willing to explore further.
Where is your manufacturing facility and what kind of capacity do you have at present?
The manufacturing facility is at Slovenia in a small town called Carinthia. While our current manufacturing is around 3,000 mats per month, we are expanding. India will act as a base for the entire South Asia and Australia for our company. We see economic prospects for our plant in India considering the huge road potential.
Most of the manufacturing in Europe is automated and we plan on following the same here. There are certain cost advantages in terms of import duties, but we will have to see the inherent costing in the long term. While I do not expect huge differences, mats will reach much faster in terms of transportation and delivery.
If costing is presented straight off, customers won’t be willing to explore further.
Siddharth Modi, Managing Director, Isotrack Innovative Infrastructure Solutions Pvt Ltd
Cookie Consent
We use cookies to personalize your experience. By continuing to visit this website you agree to our Terms & Conditions, Privacy Policy and Cookie Policy.