Safety fieldbox and the evolution of plug-and-play integration
By Edit Team | January 24, 2024 3:31 pm SHARE
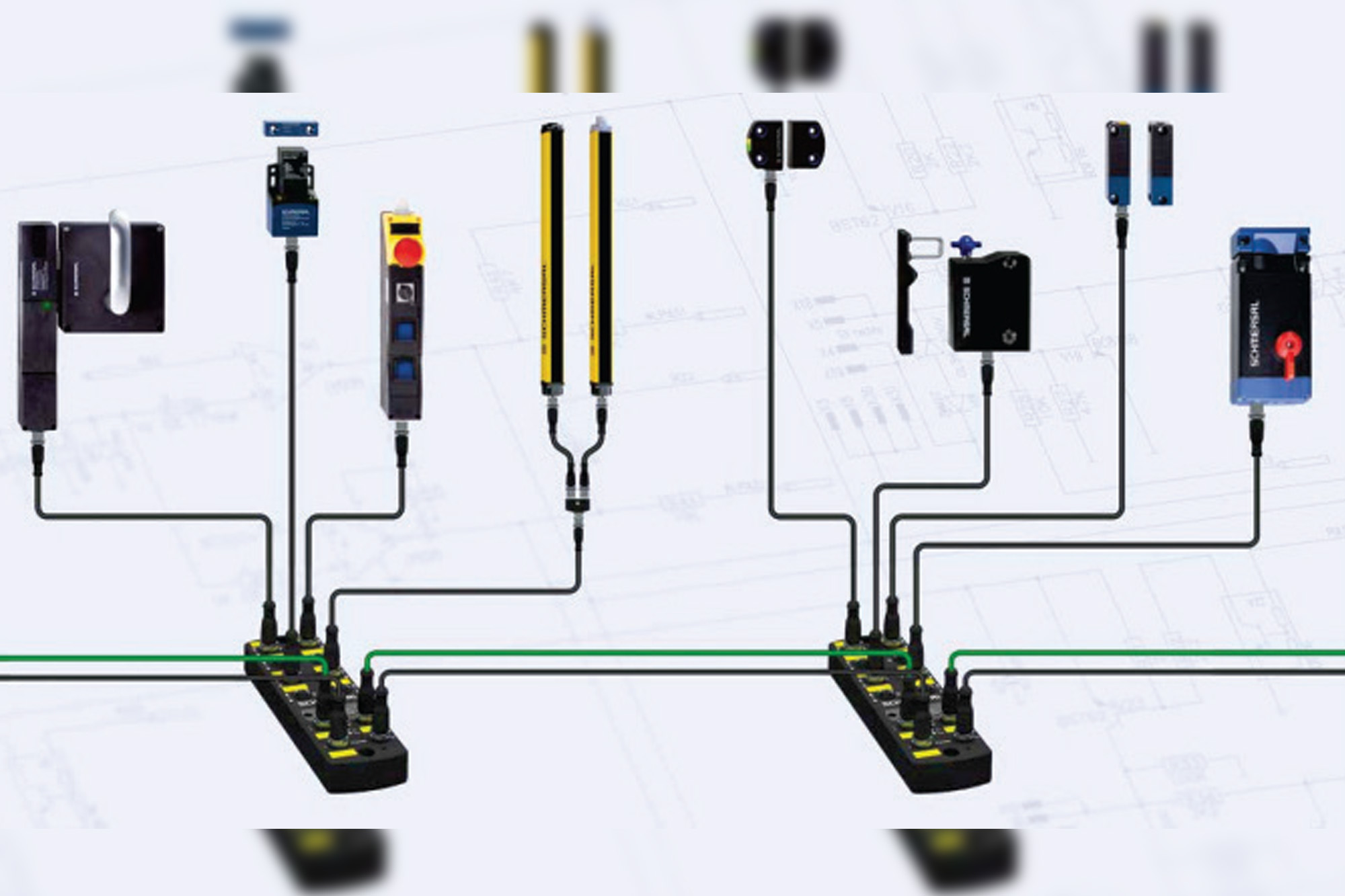
Breaking free from conventional constraints, Schmersal’s ‘safety fieldbox’ system redefines integration possibilities for safety switchgear devices. The ability to connect diverse devices in the field, from solenoid interlocks to control panels, not only reduces costs but also simplifies wiring through a plug-and-play approach. The recent introduction of the EtherCAT FSoE version further expands compatibility with different control systems globally.
Within the domain of automation technology, the transformative forces of integration, networking, and connectivity persist in molding the environment. The ever-evolving digitisation holds promise for significant advantages for both machinery manufacturers and users. This ongoing shift brings about heightened productivity, seamless alignment with individual needs, and enhanced error detection capabilities. While the historical choice between series and parallel wiring dominated the decision-making process for safety switchgear devices in a machine’s safety circuit for decades, the contemporary landscape unfolds a plethora of possibilities in terms of networking and integration. From fail-safe bus systems to safety field boxes and diagnostic field boxes, designers are now confronted with a diverse array of options. The expanded selection demands careful deliberation as they navigate through the complexities of modern choices.
Proven and reliable: The safety bus
Among the time-tested solutions, safety bus systems have demonstrated their reliability. A prominent example is the AS-Interface Safety at Work (ASiSaW). Numerous device series from Schmersal are equipped with an integrated connection for this bus system, while others can be linked through separate interface modules. The ASiSaW system facilitates the transmission of operational and safety signals through yellow ASi flat-ribbon cables, reducing installation efforts for system manufacturers and offering more flexibility in configuration. Operating companies, in turn, benefit from a more comprehensive evaluation of safety switchgear devices’ operational states. The AS-I-Safety standard not only ensures quick installation with minimal wiring but also allows for maximum flexibility, particularly in the face of system modifications or new safety requirements.
Continuous communication through SD bus
Schmersal’s SD bus, dedicated to capturing operational data, has proven itself over time. In its latest iteration, SD 4.0, data such as switching cycles, limit value warnings, and distance warnings are captured via a single-wire bus (SD bus for serial diagnosis) and transmitted cyclically to an SD gateway or the modular protect PSC 1 safety controller. This sets the stage for simplified networking with higher levels, utilising standardised protocols like OPC UA for M2M communication. The advantages include improved visualisation of diagnostic information and enhanced accessibility via mobile devices such as tablets and smartphones. SD gateways serve as the connection point between the Schmersal SD Bus and traditional field buses or M2M interfaces, contributing to clear visualisation, part of a predictive maintenance strategy.
Introduction of SD fieldbus gateway with web server
Capitalising on these advantages, Schmersal is diligently expanding its product range. The SDF Fieldbus Gateway, a new variant transmitting signals to the machine controller via fieldbus, was unveiled at SPS. This latest SD gateway comes equipped with a web server and a microSD card, enabling users to assess event logs in real-time through the web interface and retrieve diagnostic data of connected safety switchgear devices in plain text on the browser. Direct control of devices like solenoid interlocks and control panels via the web interface further enhances system availability and reduces downtime, supporting a ‘Lean,’ cost-saving wiring approach for up to 31 safety switchgear devices.
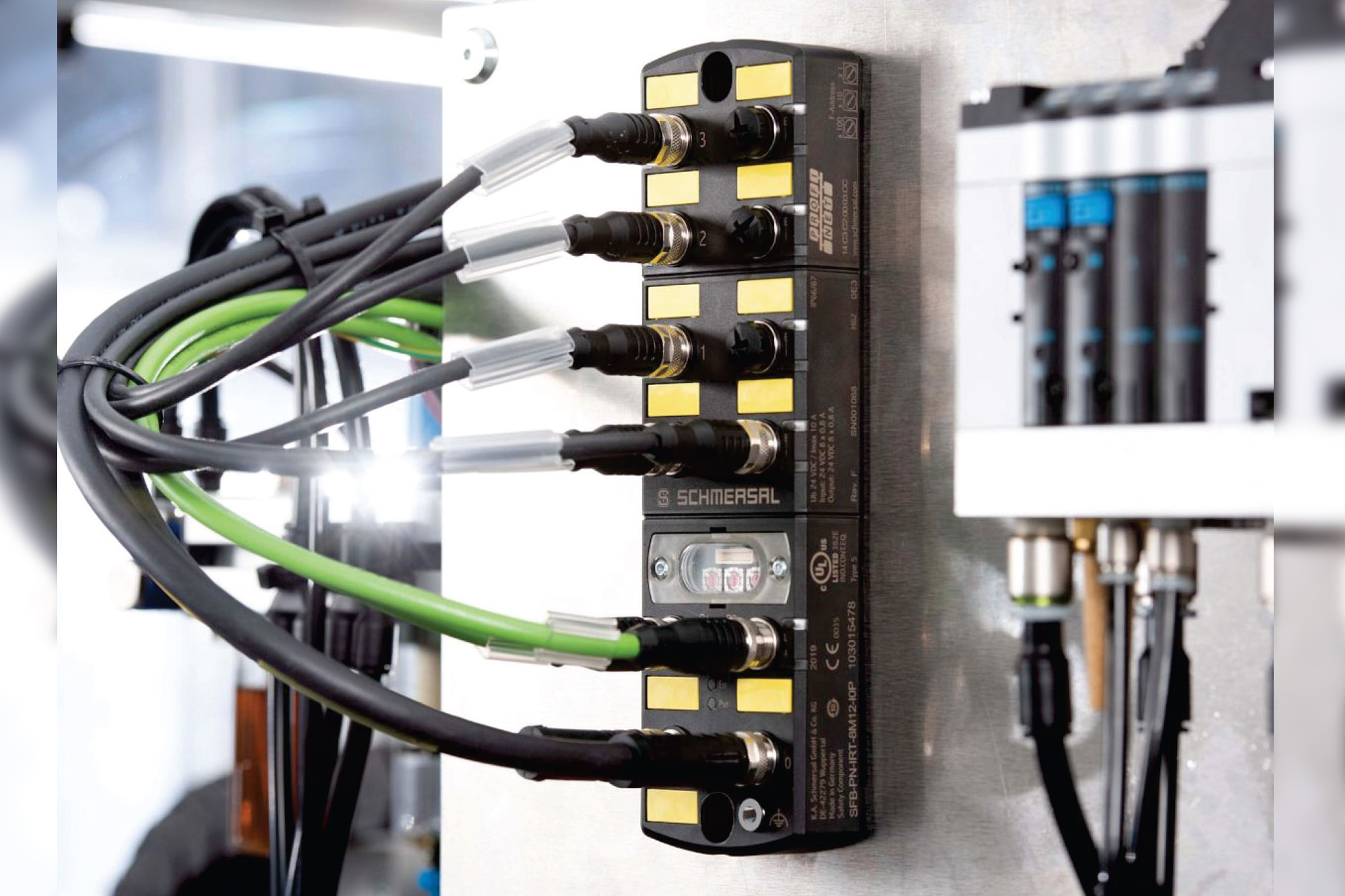
Open integration with safety fieldbox
In the context of fieldbus systems, Schmersal’s ‘safety fieldbox’ system allows connection for up to eight safety switchgear devices of different types in the field, reducing costs and simplifying wiring. Both safety and operational signals connect to a higher-level control module, such as a safety PLC, using plug-and-play. Previously achievable only with the PROFINET/PROFIsafe Protocol, a version with Ether-net/IP-CIP Safety interface has recently been introduced, broadening compatibility with various control systems globally.
Three solutions, shared objectives
The three wiring concepts presented here offer simple, cost-effective solutions based on the plug-and-play principle. These solutions provide remarkable flexibility in adapting to the safety requirements of complex systems and machinery, with additional transmission of diagnostic signals ensuring optimal process transparency. Notably, the reduced need for cables aligns with sustainability goals, contributing to resource conservation.
New networking concepts and reduced wiring
As mechanical engineers increasingly shift toward alternative wiring and networking concepts, continuous development is underway. More terminal devices are being equipped with corresponding interfaces. Schmersal’s future outlook includes new versions of the SD Gateway, incorporating additional functions and integration with safety switchgear devices.
The journey ahead
Networking and connectivity will continue advancing with new features at a heightened level. An emerging example is the ‘digital type plate’ of every product, stored not only in machine documentation as part of its digital twin but also retrievable via M2M interfaces. This development holds the promise of facilitating machine servicing and enhancing transparency, showcasing the transformative power of connectivity in automation technology.
Cookie Consent
We use cookies to personalize your experience. By continuing to visit this website you agree to our Terms & Conditions, Privacy Policy and Cookie Policy.