SAFETY FIELDBOX, ASI-SAW, SD-INTERFACE AND OPC UA
By Edit Team | June 20, 2022 12:25 pm SHARE
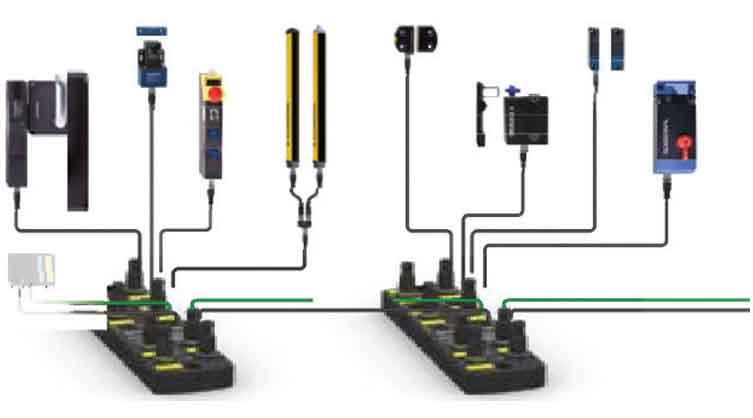
Benefits of AS Interface Safety at Work system include the capability to transmit operational and safety signals via the special-purpose ASi flat-ribbon cable.
Networking is a trend, in machine safety too. Electrical designers have various options at their disposal to allow safety switchgear devices to be connected together – options that offer considerable benefit over traditional series connection. The solution that is most suitable depends on the individual requirements.
Machine Safety – Best When Networked
A rather crude formula that applies to the current trend in the communication of safety switchgear devices in mechanical engineering and automation technology. Development has taken somewhat longer than in non safety communication, partly on account of the complex regulations in place for machine safety (in the EU, this is the Machinery Directive).
Tried and tested and good
Here too, though, there are systems that are tried and tested and that have been operational for quite some time, such as safety bus systems. The AS-Interface Safety at Work (ASi SaW) is widely used in safety technology. Many device series from Schmersal are available with an integrated connection for this bus system; the others can be connected via separate interface modules. Benefits of this system include the capability to transmit operational and safety signals via the special-purpose ASi flat-ribbon cable. For system manufacturers, this means rapid installation and more flexible configuration, while for operating companies, it means more comprehensive evaluation of the operating states of safety switchgear devices.
The AS-i-Safety standard not only facilitates rapid installation with minimal wiring effort but also maximum flexibility, e.g., in the event of system modifications or new requirements and safety requirements. Another advantage is the comprehensive range of diagnostic functions. These make for more rapid identification of the source of error in the event of irregularities or faults. This is particularly beneficial in the case of extensive and complex systems, and can help to reduce downtime significantly.
Continuous communication from switchgear to higher levels of Schmersal’s SD bus for the gathering of operational data, such as switching cycles, limit value warnings, and distance warnings, has been proven to be reliable. These data are recorded via an SD interface and sent to an SD gateway or, in its most recent form, SD 4.0, the modular Protect PSC. 1 safety controller on a cyclical basis. This creates the prerequisite for clearly simplified networking with higher levels – via OPC UA as a standardised protocol for M2M communication.
Networking has the advantage of better visualisation of diagnostic information collected in the field, and better access via mobile devices such as tablets and smartphones. This enables location-independent control of manufacturing processes, which can be clearly visualised, such as part of predictive maintenance concepts.
Alternative – the Safety Fieldbox
An alternative to the AS-i SaW safety bus is the Safety Fieldbox system developed by Schmersal. Each field box enables field connection of up to eight safety switchgear devices of different types. Electromechanical and electronic terminal devices occupy just one device connection each. Both the safety and operational signals are captured and connected to higher-level integrated process and safety controllers via Europe’s most commonly used bus system – PROFINET/PROFIsafe.
Users will soon have even more choice in this area, including versions with connection to EtherNET/IP CIP Safety and EtherCAT FSoE to serve additional and popular protocols used internationally.
Three solutions, common objectives
The three wiring concepts are economical solutions that can be installed and commissioned quickly and easily. Additionally, these solutions offer extreme flexibility when it comes to adapting the individual safety requirements of complex systems and machinery. Moreover, additional transmission of all diagnostics signals from connected devices ensures optimum process transparency.
The three wiring concepts are economical solutions that can be installed and commissioned quickly and easily. Additionally, these solutions offer extreme flexibility when it comes to adapting the individual safety requirements of complex systems and machinery. Moreover, additional transmission of all diagnostics signals from connected devices ensures optimum process transparency.
Cookie Consent
We use cookies to personalize your experience. By continuing to visit this website you agree to our Terms & Conditions, Privacy Policy and Cookie Policy.