Sai Ansh presents multipurpose foamed concrete
By Edit Team | November 5, 2014 11:14 am SHARE
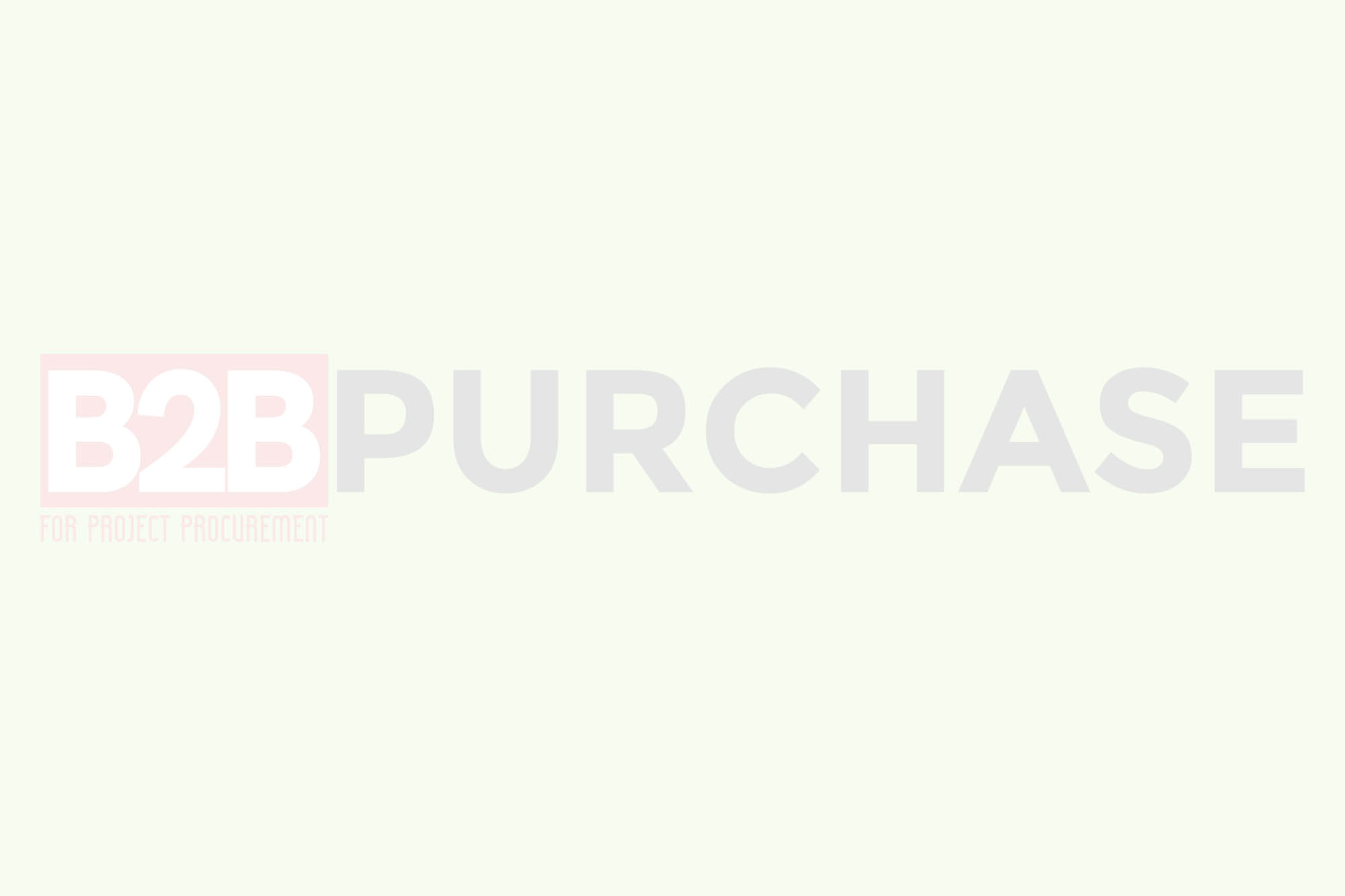
Sai Ansh has always been coming up with innovative products to meet the ever-changing demands of industry. It now offers versatile foamed concrete which has number of applications as described below.
Lightweight foam concrete blocksFoamed concrete is used for making lightweight blocks. The lightweight foamed concrete blocks are mainly used to build partition walls. The lightweight nature of the blocks means that they impose a minimum loading on the building. Foamed concrete blocks also provide good thermal insulation and sound insulation.
Void fillingIt is also very useful for void filling. As it is very fluid it will pour into even the most inaccessible places. It can be used for planned work, but also in emergencies to provide stability and support very quickly.
It has been used to fill old sewers, basements, storage tanks and voids under roadways caused by heavy rain. It can be applied even through small openings making the work much easier and cheaper than other methods. If necessary, it can also be pumped into position over considerable distance.
Roofing insulationIt has been supplied for roofing insulating. A low density mix is chosen and the resulting air content gives the material excellent thermal insulation properties. The low density also has the advantage that it does not significantly add to the overall weight of the roof.
Roofing is probably the most widespread application of foamed concrete. Foamed concrete has two benefits when it is used for roofing. The first benefit is that it provides a high degree of thermal insulation. The second benefit is that it can be used to lay a flat roof to falls, i.e. to provide a slope for drainage. In countries where roofs are flat and where roof surfaces are used as part of everyday life, foamed concrete is strong enough to support foot or even vehicular traffic on the roof. Foamed concrete is also much lighter than slopes made from mortar screeds. This means that a roof with a slope made of foamed concrete imposes a lower loading on the structure of the building.
Bridge abutmentFoamed concrete is particularly suitable for bridge abutments because it does not impose the large lateral loads, which can be a problem when using traditional granular materials. With traditional abutments, there is a lot of sideways pressure against the bridge walls caused by the materials used and their compaction.
Using foamed concrete, the lateral load is practically eliminated, so the bridge walls do not have to be as thick. This in turn means that the wall foundations can be made less massive. Huge cost savings can be achieved by reducing the thickness of the walls, and the size of the foundations.
Trench reinstatementFoamed concrete is suitable material for trench reinstatement (the filling of trenches dug in roads when pipes are laid or repairs are carried out). The traditional methods of filling trenches in the roads, i.e. the use of granular fill materials, result in settlement and damage to the road and potentially, to the pipes. With foamed concrete there is no settlement; and because the foamed concrete is very fluid, it will fill any voids and cavities in the trench sides.
Also, the load spreading characteristics of foamed concrete means that axle loads are not transmitted directly to the services in the trench, so the pipes are not damaged by the weight of traffic.
Traditional granular backfill materials require compaction. Foamed concrete does not require compaction, so there is no need to use any compactors. This is important since the use of such tools can cause vibration related illnesses among the workers.
Road sub-baseIt can be used to make road structures less heavy. This helps solve the problem where the traditionally heavy road structures cause severe settlement of the road, particularly in areas of soft ground. By constructing the road sub-base from a lightweight material, the overall weight of the structure can be greatly reduced. As foamed concrete is very versatile, with a wide range of densities, it has proved to be an suitable, cost-effective material for solving this problem.
Wall constructionFoamed concrete can be used for cast in situ walls. These can be made either by using traditional shuttering or hollow polystyrene moulds. This provides a quick and cheap method of building, with the added advantage of excellent thermal insulation. A wall made from 1,200kg/cu.m density foamed concrete provides the same level of thermal insulation as would a wall made from dense concrete that was 5 times as thick and made from 10 times the quantity of materials as the foamed concrete wall.
TunnellingFoamed concrete also suits for tunnel construction and repair. It is used both for the filling of voids created and exposed during tunnelling, and for grouting the finished work, including gaps behind the tunnel lining.
Floor constructionFoamed concrete provides good material for floor construction. It suits for building sub-floors quickly and cheaply and can be used for levelling terrain and raising floor levels as well as for insulation purposes.
Ground worksIt can be used in various types of ground projects, including stabilising embankments after landslides, highway widening schemes, land reclamation and filling in of harbours. As it does not sink into soft subsoil, redevelopment can begin much sooner after application than can using traditional methods. For similar reasons, it is also ideal for road foundations.
Fire breaksThe fire resistant properties of foamed concrete make it an suitable material for fire breaks in buildings where there are large undivided spaces. It is used to prevent flame penetration through the services void between floor and ceiling in modern construction, and also to protect timber floors in old houses.
Sound insulationFoamed concrete reduces the passage of sound, both from background noise and due to impact. It is, therefore, an ideal material for internal walls and suspended floors in multi-storey buildings, especially ones with communal use.
Sai Ansh’s mobile plant Sai Ansh introduces its ‘plug & ready to use’ type foam concrete plant, with integrated system of mixer, foam generator and pump, working in tandem. According to company, it saves at least ` 4,00,000 for making a arrangement to pump the foam concrete from the plant to the site.
Its foam concrete plant (smallest capacity) is within-built capacity to pour foam concrete up to 20 mtrs vertically and 200 mtrs horizontally. The speciality of plant is that the density of the foam concrete can be adjusted easily by just turning a knob. The plant requires just 40 sq. ft. of area and requires just 06 HP (SA-40) of power, thereby considerably reducing the running cost. The plant can be very easily operated with just one operator by pressing buttons in the control panel, and unskilled labour to load the raw material.
In the plant it takes just 1 to 8 minutes to discharge one batch (batch size depends on the capacity of the plant) of foam concrete after the material is loaded in the mixer, that too at 200 mtrs away from the plant.
Cookie Consent
We use cookies to personalize your experience. By continuing to visit this website you agree to our Terms & Conditions, Privacy Policy and Cookie Policy.