Save Concrete
By Edit Team | February 29, 2016 12:48 pm SHARE
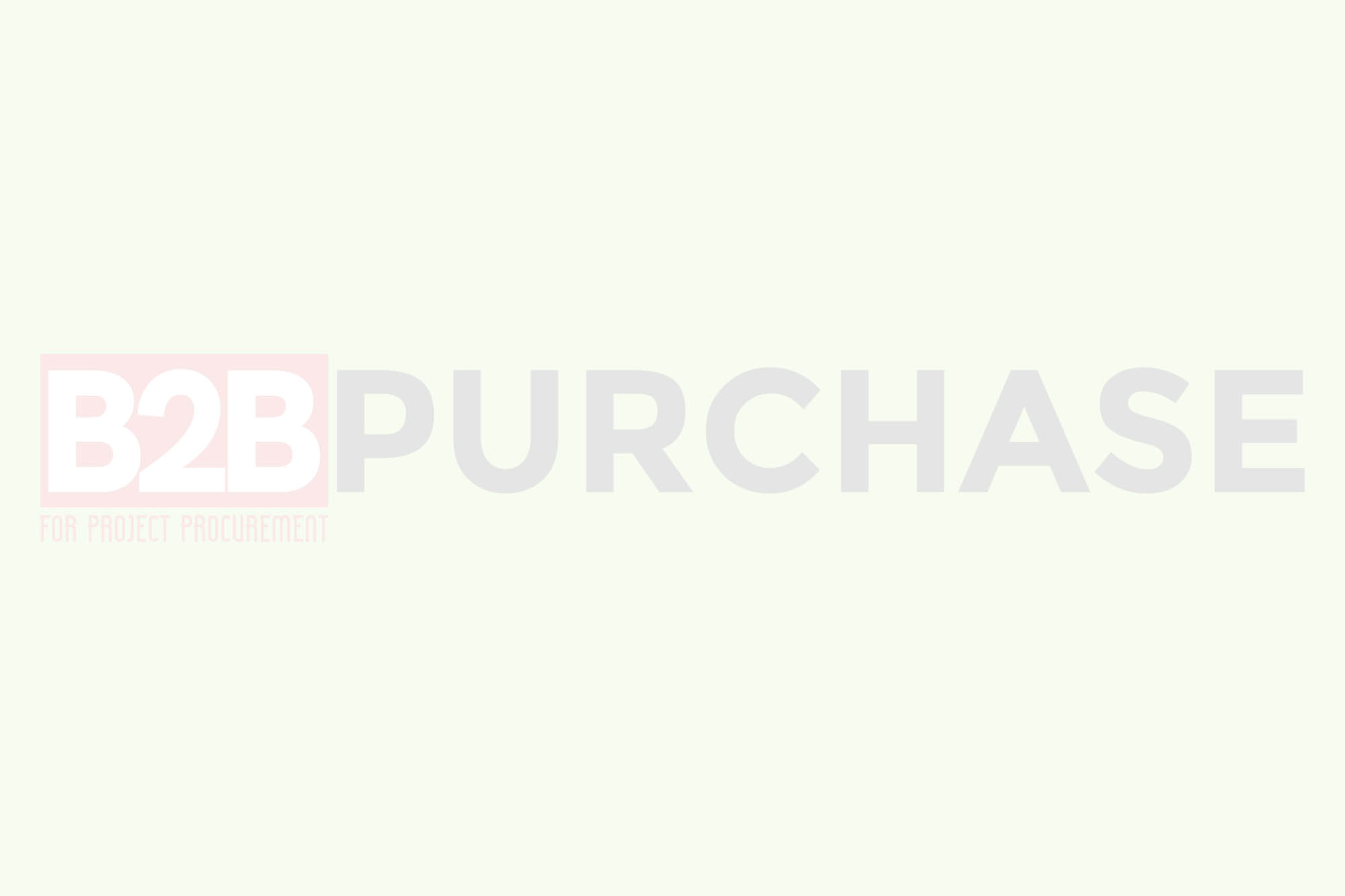
11 ways concrete can fail, and how to avoid them
Industry experts discussed on different ways concrete can fail and how can one avoid the failures
Concrete properties are measured in fresh and hardened state. The specifications of concrete have been now evolved based on recent findings in concrete and structural requirements and past experiences of failure in concrete. “In fresh state concrete is specified for workability, heat evolution, shrinkage, air content, density, temperature; whereas in hardened state concrete is specified for its compressive, tensile, Flexural strengths, modulus of elasticity, creep, durability,” says, Avijit Chaubey, Head R&D, ACC Concrete, ACC Ltd.
Reinforced concrete can fail due to many reasons. These could be inadequate strength, which leads to mechanical failure, or it could be due to a reduction in its durability. Corrosion and freeze or thaw cycles also cause concrete failure, as they may damage the poorly designed or constructed reinforced concrete. “Reinforced concrete can be made by casting the concrete around ridged steel bars or forming the concrete inside a metal or timber framework and is called rebar. When rebar corrodes, the oxidation products expand and tend to flake, thus cracking the concrete and un-bonding the rebar from the concrete,” explains Andrea Fernandes, Marketing Executive, Choksey Chemicals Pvt Ltd.
Mentioned below are few ways how concrete can fail:
1. Impermeability
Impermeability to water and other deteriorative factors is a key requirement in Indian construction. Despite technological advances in material systems, the deterioration rate for concrete remains quite high and is evident by the extent of leaking or dilapidated structures. With the extreme requirements put on concrete, along with paucity of high quality raw materials, makes the production of impermeable concrete structures quite difficult.
“We have developed the Dynamic SynCrystallisation Technology, which finds application not only in concrete improvement and permeability reduction, but also in mineral based protective coatings, plasters, waterproofing systems and many similar cement-based applications requiring a very dense, impermeable, mineral system,” says Sunny Surlaker, Head Admixtures Division, MC Bauchemie (India) Pvt Ltd.
2. Water cement ratio
There are certain parameters of concrete mixture which have a direct correlation to its properties. The most important parameter among all is the water cement ratio. It is the water cement ratio which has its direct effect on strength and durability. Water cement ratio is inversely proportional to both strength and durability.
3. Shrinkage
Shrinkage is an expected phenomenon in a concrete structure. It can often be controlled with stress-relieving joints and properly placed reinforcing steel. Concrete shrinkage may occur throughout a structure’s life cycle. Shrinkages are of 5 types majorly:
• Plastic shrinkage – Plastic shrinkage occurs in fresh state due to rapid drying of concrete. This can be avoided by keeping the concrete moist and not allowing it to dry till it starts gaining strength.
• Chemical shrinkage – Chemical shrinkage happens due to reduction in volume of products formed after hydration of cement. After hydration cement forms CSH gel and calcium hydroxide. The volume of CSH and calcium hydroxide is less than the volume of cement and water before reaction, this phenomenon is called chemical shrinkage.
• Drying shrinkage – Drying shrinkage occurs when water present in hardened concrete evaporates, and this water before evaporation exerts pressure inside capillary pores and maintains gaps. But after evaporation, the particles move closer to each other resulting in shrinkage again. This is called drying shrinkage. These shrinkages can be reduced by admixtures in concrete, the most widely used being Polyoxy Alkyl Alkylene Ether. In addition to this, concrete mixture proportioning should be such that the aggregates should be as maximum as possible, while the cementitious paste should be the least. As shrinkage happens in the cementitious paste and aggregates are stable in volume.
• Autogenous shrinkage – Autogenous shrinkage happens when water cement ratio is below 0.35 resulting in self dessication leading to volume reduction of hydration products.
• Carbonation shrinkage – Carbonation shrinkage occurs due to reaction of calcium hydroxide with carbonic acid formed by carbon dioxide and water reaction. The calcium carbonate so formed leaches out of concrete and results in volume reduction.
4. Heat evolution
Heat evolution or heat of hydration has also been a reason for failure of many structures, mainly mass concrete structures. The target to avoid such failures should be to choose concrete mix and materials in such a way, that the heat evolution is the least possible for the required hardened properties. This is achieved by replacing heat evolving materials like OPC with other cementitious materials like Fly Ash, GGBFS etc. Some admixtures come to rescue namely retarders which delay the reaction rate of cement with water. In proportioning again keeping cementitious content to the least possible extent and keeping aggregate content higher also solves this issue.
5. Chemical attack
Concrete is susceptible to cracking on account of chemical attacks like sulphate attack, alkali aggregate reaction, carbonation. sulphate attack happens when sulphate from internal or external sources reacts with calcium aluminate hydrates in concrete and produces a mineral called ettringite. The ettringite so formed is very high in volume as compared to the volume of reactants. This leads to severe cracking of concrete and thus failure. This can be avoided by keeping the C3A content in concrete low, thus some cements have been specified by the codes which should not have C3A content above 5 per cent which are called “sulphate resisting cement”. In cases when sulphate concentrations are expected to go high and sulphate resisting cement is not expected to perform, cement called super sulphated cement which has upto 90 per cent of ground granulated blast furnace slag is required to be used.
When concrete is manufactured by using some aggregates which contain reactive silica, the concrete again undergoes chemical reactions which produce severe map like cracking on concrete, thereby leading concrete towards failure. “In the chemical reaction, reactive silica reacts with water in presence of alkalis and forms expansive agents namely silanol gel which leads to severe cracking of concrete. This can be avoided by choosing aggregates carefully, or using cement with low alkali content which is specified by Na2O or by replacing OPC with other cementitious materials like fly ash, preferably Class F Fly Ash (with less CaO content), GGBFS, micro silica,” says Chaubey.
“In order to minimise the risk of sulphate attack; test the sulphate content of soil or water that will be in contact with the concrete. Also, employ the use of published guidelines to specify a resistant concrete mixture, informs Fernandes.
6. Mechanical Failure
Cracking can occur due to an inadequate quantity of rebar, or rebar spaced at a great distance. The concrete then cracks either under excess loading, or due to internal effects such as early thermal shrinkage while it cures.
Failures leading to collapse can be caused by:
• Crushing the concrete, which occurs when compressive stresses exceed its strength
• By failure or yielding of the rebar when bending or shear stresses exceed the strength of the reinforcement
• By bond failure between the concrete and the rebar
7. Corrosion
Failure due to corrosion may occur if the reinforcement is too close to the surface. However, only when there is sufficient moisture and oxygen to cause electro potential corrosion of the reinforcing steel, carbonated concrete incurs a durability problem.
Internal protection measures for corrosion includes using epoxy-coated reinforcing steel and adding corrosion inhibitors to the fresh concrete. External protection methods such as penetrating sealers or waterproof coatings applied to the exposed concrete can also inhibit access of chlorides and moisture.
8. Chloride
Chloride anions induce both generalised and localised corrosion of steel reinforcements. For this reason, one should ensure using only fresh raw water or potable water for mixing concrete. Also the coarse and fine aggregates should not contain chlorides, rather than admixtures which might contain chlorides. This is commonly found in wet areas or areas repeatedly exposed to moisture.
9. Freezing
Freezing and thawing cycles can be very detrimental to concrete over a period of time. Each cycle allows more moisture to penetrate into the concrete, unless a protective coating is applied to the concrete. The stress of the moisture freezing inside the concrete causes larger defects with each passing cycle. Air-entrained concrete can be used to help ease some of the expansive stresses of harsh temperature changes on the concrete.
To resist freeze-thaw deterioration, the hardened concrete must contain an air-void system that consists of tiny, closely spaced air bubbles, called entrained air. These voids provide space to relieve the pressure of the freezing water, thereby minimizing stress on the concrete. This process involves adding air-entraining admixtures to a fairly strong concrete mix.
10. Alkali- Aggregate Reaction (AAR)
AAR refers to chemical reactions taking place within the concrete mix. Certain aggregates inside the concrete may react with alkalis, hence causing concrete expansion. The alkalis may be also be from within the concrete mix, or may be from external sources like deicing salts or sea or ground water. When these types of reactions occur, they create a gel-like substance that swells when moisture reaches it. The stresses from the swelling create internal tensile forces, which further may crack the concrete from within.
11. Poor Workmanship
Concrete itself is so variable that properly constructing a concrete structure can be difficult. Some concerns related to workmanship are improper location of rebar, over or under consolidated aggregates, finishing surface before bleeding occurs, over watering for workability. Each of these may end up not be of importance overall, but may contribute to a structural failure.
————————-
In fresh state concrete is specified for workability, heat evolution, shrinkage, air content, density, temperature.
Avijit Chaubey,
Head R&D,
ACC Concrete, ACC Ltd.
————-
We have developed the Dynamic SynCrystallization Technology, which finds application beyond concrete improvement and permeability reduction.
Sunny Surlaker, Head – Admixture Division, MC-Bauchemie
Cookie Consent
We use cookies to personalize your experience. By continuing to visit this website you agree to our Terms & Conditions, Privacy Policy and Cookie Policy.