Say Goodbye to Slow and Costly Welding with Sigma Weld Accelerated TIG (S.W.A.T)
By Edit Team | March 16, 2023 11:48 am SHARE
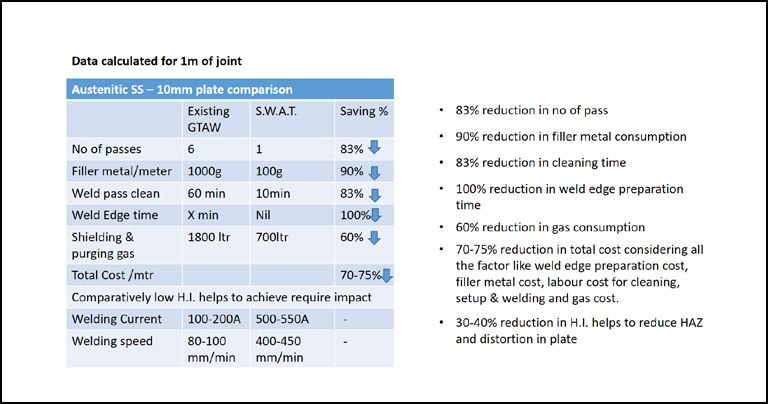
Tig welding or GTAW is a popular welding process due to its cleanliness and ability to be applied in all positions. However, it is considered slow and costly. In this context, manufacturers in the Defense and Aerospace, Tube mills, Cryogenic Vessels, Tank and Vessel, Food, Pharma, and Dairy Equipment segments can now take advantage of a new welding process called Sigma Weld Accelerated Tig or SWAT.
India has a significant advantage in manufacturing excellence and workforce, making it one of the top countries for manufacturing. With the manufacturing segment projected to grow at a YoY rate of 7 percent–12 percent, India has a prime opportunity to meet the rising international demand.
Tig welding, known as GTAW, is a highly favoured welding process due to its cleanliness. It can be applied in all positions and is easily automated. However, it is generally considered to be a slow and costly method.
Is it possible to increase the speed of GTAW/TIG welding for welding exotic materials, thereby reducing the overall project cost?
As you are aware, manual Tig welding involves using filler wires cut to 1-meter lengths. Approximately 4 inches of the stub end is unusable as the welder cannot safely reach it to the arc. This translates to about 10 percent of the total filler wire consumption, making the process expensive.
In the case of an 8mm-thick single V joint, the manual welding speed for GTAW is around 55mm to 60mm per minute, requiring four passes to weld. A long seam of 1.5 meters would require six long meters of welding, taking at least 100 minutes, including waiting time for filler wire start stops and interpass temperature, which can take up to 180 to 240 minutes.
However, the good news for manufacturers, especially in segments such as Defence and Aerospace, Tube mills, Cryogenic Vessels, Tank and Vessel, Food, Pharma, and Dairy Equipment, is that TIG welding now has a new, accelerated, and highly efficient process called SWAT (Sigma Weld Accelerated Tig).
SWAT is an automated keyhole welding process that can increase welding speed by up to 100 percent compared to the traditional GTAW process. It does not require edge preparation for materials up to 10 mm, making it a cost-effective and efficient solution for welding exotic materials.

How does SWAT work?
The SWAT process is highly efficient and easy to learn and adapt. It involves a highly concentrated arc that creates a keyhole and moves through the material at almost three times the speed of GTAW. One of the standout features of the SWAT process is its constricted arc, which requires almost three times the arc force compared to GTAW to melt the pool with the same energy parameters. This results in deeper penetration while minimizing the effects of heat. Additionally, SWAT requires low energy input, causes minimal distortion, and can be used with or without filler wires.
When comparing SWAT with the traditional GTAW process, it becomes clear that there is a significant difference between the two. SWAT reduces material consumption, gas usage, and preparation time, making it a more cost-effective and time-efficient solution for welding exotic materials.
What are the benefits of using SWAT in tube mill applications, and how does it compare to traditional welding processes regarding productivity and cost savings?
Tube mill applications can achieve nearly double the welding speed using SWAT compared to a single torch with plasma and TIG combinations without additional filler. Moreover, every weld subjected to SWAT in Tube Mill Applications underwent rigorous testing, including RTR, flaring, bend, and radiography. The SWAT process ran for multiple shifts without any stoppage time and achieved consistent results every time.
SWAT has delivered outstanding results to various industries, increasing productivity and cost savings. The process reduces welding time and energy input and enables welding up to 14mm in a single pass, resulting in labour costs, consumables, and post-weld cleaning time savings. The time has come for SWAT to become a go-to application in the manufacturing industry.
To know more or to book a Demo, contact:
Call @ 022-4541-0500 Email id: sigmaweld@edmail.in
Cookie Consent
We use cookies to personalize your experience. By continuing to visit this website you agree to our Terms & Conditions, Privacy Policy and Cookie Policy.