Shot peening made easy at Mitsubishi Steel
By Edit Team | July 28, 2015 11:51 am SHARE
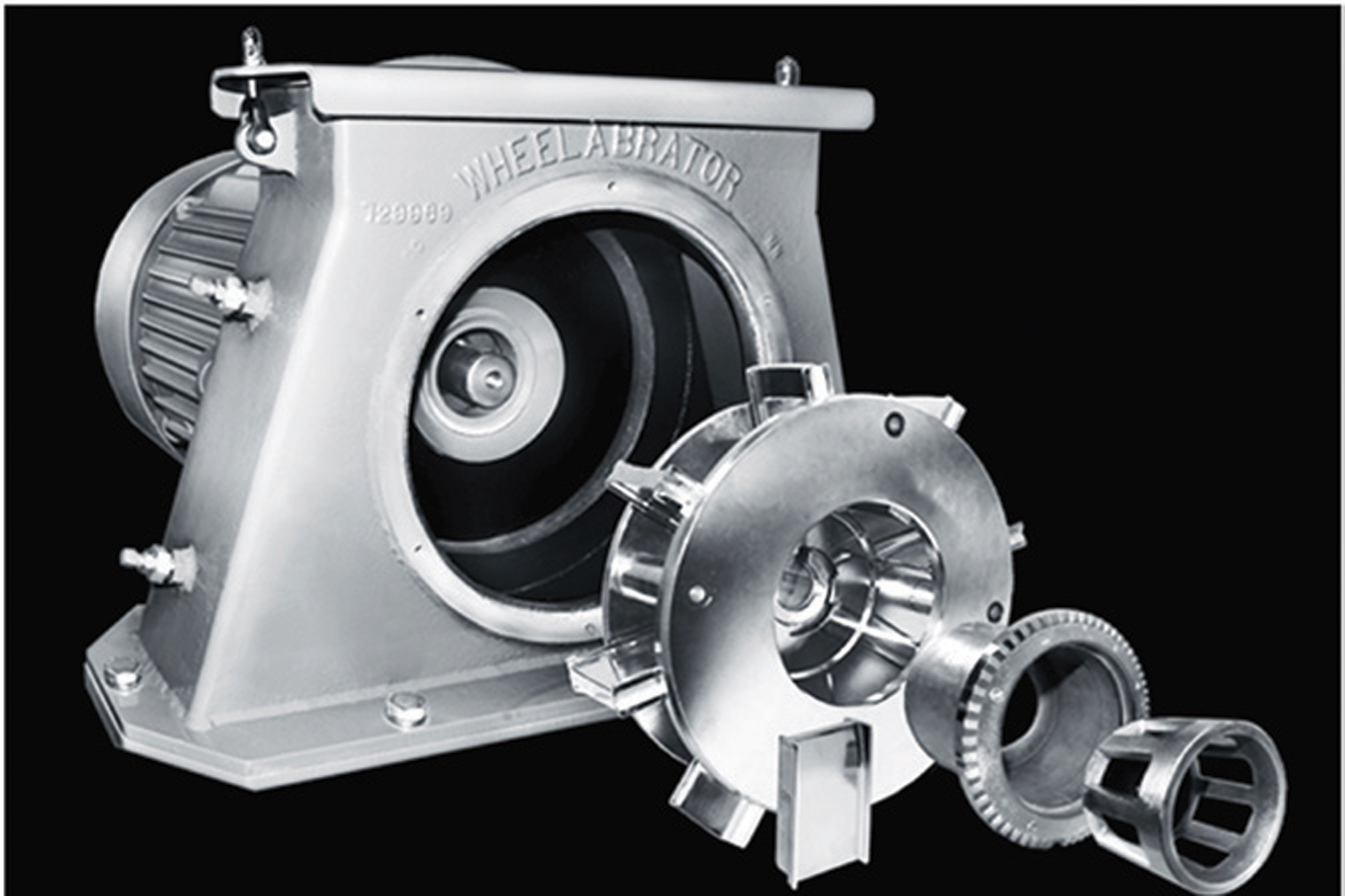
Non-stop production was taking its toll on the shot peening equipment at MSSC, a Mitsubishi Steel division, in Chatham, Ontario. Used exclusively to shot peen stabiliser bars for the automotive industry, the machine was experiencing a number of issues including high levels of vibration, wear on the housing and major wear and tear to the impellers inside the blast wheels. Working at full capacity – in three-shift operation, seven days a week – also resulted in the need to replace blast wheel motors at a rate of 20 per year.
The MSSC maintenance team called in experts from Wheelabrator Plus to analyse the machine set-up, identify the root causes of the problems with the machine, and find a solution.
Joe Decarvalho, Wheelabrator Plus, Technical Sales Representative said, “A myriad of factors can cause operational issues of shot blast equipment and with today’s production pressures there often is little time to fix things. In the case of MSSC, however, finding the source of the problem was easy. Their operations had simply outgrown the equipment installed, in particular the blast wheels. The solution, therefore, was equally simple. Blast wheels were needed that wouldn’t be stretched by everyday requirements and tough enough to perform happily in a busy and pressured production environment at MSSC.”
Collectively working with Kevin Daly, maintenance supervisor at MSSC, to find the best longevity solution, the decision was made to upgrade to 40 HP EZEFIT blast wheels to improve longevity and permit flexibility to allow for wheel amp adjustments based on customer needs, while still meeting the demands of a high paced operation.
The result
Motors on the four new EZEFIT wheels no longer have to run at full capacity, ensuring the blast wheels operate reliably and efficiently – and for longer. All four wheels were fitted with hardened impellers to withstand the pressure of the special abrasive used by MSSC for the application, drastically reducing wear and downtime.
Kevin Daly said, “The wheels are now running smoothly without being forced, because we are running the 40 HP motors. The problems we were experiencing with vibration and wear and tear to the impeller were eliminated immediately with the EZEFIT wheels, and we have only had to replace one motor in the last 12 months.”
Cookie Consent
We use cookies to personalize your experience. By continuing to visit this website you agree to our Terms & Conditions, Privacy Policy and Cookie Policy.