Standard full powershift transmission to a CVT can save fuel
By Edit Team | May 15, 2022 8:37 pm SHARE
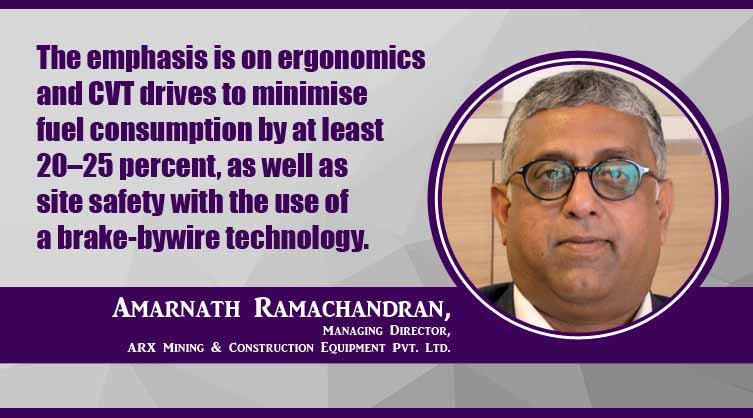
Amarnath Ramachandran Managing Director, ARX Mining & Construction Equipment Pvt. Ltd. In an Interview with B2B Purchase.
What are the products and technologies you are planning to display at Excon? ARX Mining and Construction Equipment Private Limited is a greenfield start-up venture. We have four new product launches along with other machines on display:
A massive grader with a 310-horsepower engine and an 18-foot mouldboard. This grader is ideal for hauling road maintenance in mines with large dump trucks and also for construction and canal sites with very heavy earthwork.
ARX G1000 Motor Grader (120 hp, 11 tonne): This is the smallest Arx grader in the range with a BS IV 120 HP engine and a 10-foot mouldboard. This machine is excellent for small roads, plantations, and also for shoulder work on highways where contractors today lock up large graders after finishing paving for shoulder work.
ARX G3300 Blasthole Drill: (6–8”): Self Propelled heavy duty 6–8” crawler mounted blast hole drilling rig which is capable of drilling 6–8” direct rotary/DTH. This machine is fitted with a Volvo D5/Cummins QSB 6.7 engine, 173 BHP, and has a heavy-duty box type derrick. It combines the best features of a piling rig (with a slew arrangement) and is capable o f drilling three holes in a single location.
ARX S1200-Dust Suppression Sprayer: this is a truck-mounted unit with a slave engine and a pump drive system which sprays atomised water (mist) to a distance of 120 m. This machine can be used to suppress dust without creating a slushy mess, as is often the case with sprinkler trucks. This machine can be used in mines, cities, ports, etc. The main feature of this machine is that dust suppression is achieved with optimum use of water.
What are the latest technologies and solutions you have adopted recently?
ARX Mining was incorporated three years ago, in the year 2019. We have designed and made prototypes for four machines, with another two coming out later this year. We have also been working on updating the Indital Reach Stackers to closed centre hydraulics and also switching from a conventional full powershift transmission to a CVT to save fuel.
We have telematics as a standard on the graders, and it is optional on the stackers. Apart from this, we are also working on a brake by wire system to interface the brakes electronically with a radar detector to automatically slow down or stop the equipment in the event of a collision. The next step for the third graders will be to also steer by wire and then have a fully autonomous solution. The focus is on ergonomics and CVT drives to reduce fuel consumption by at least 20–25 percent and site safety by using a brake by wire system, where the hydraulic brake actuation is assisted by electronic proportional signals from a radar sensor, which will automatically slow down the machine if an obstacle is detected.
Cookie Consent
We use cookies to personalize your experience. By continuing to visit this website you agree to our Terms & Conditions, Privacy Policy and Cookie Policy.