Stay safe and competitive
By Edit Team | April 14, 2016 12:22 pm SHARE
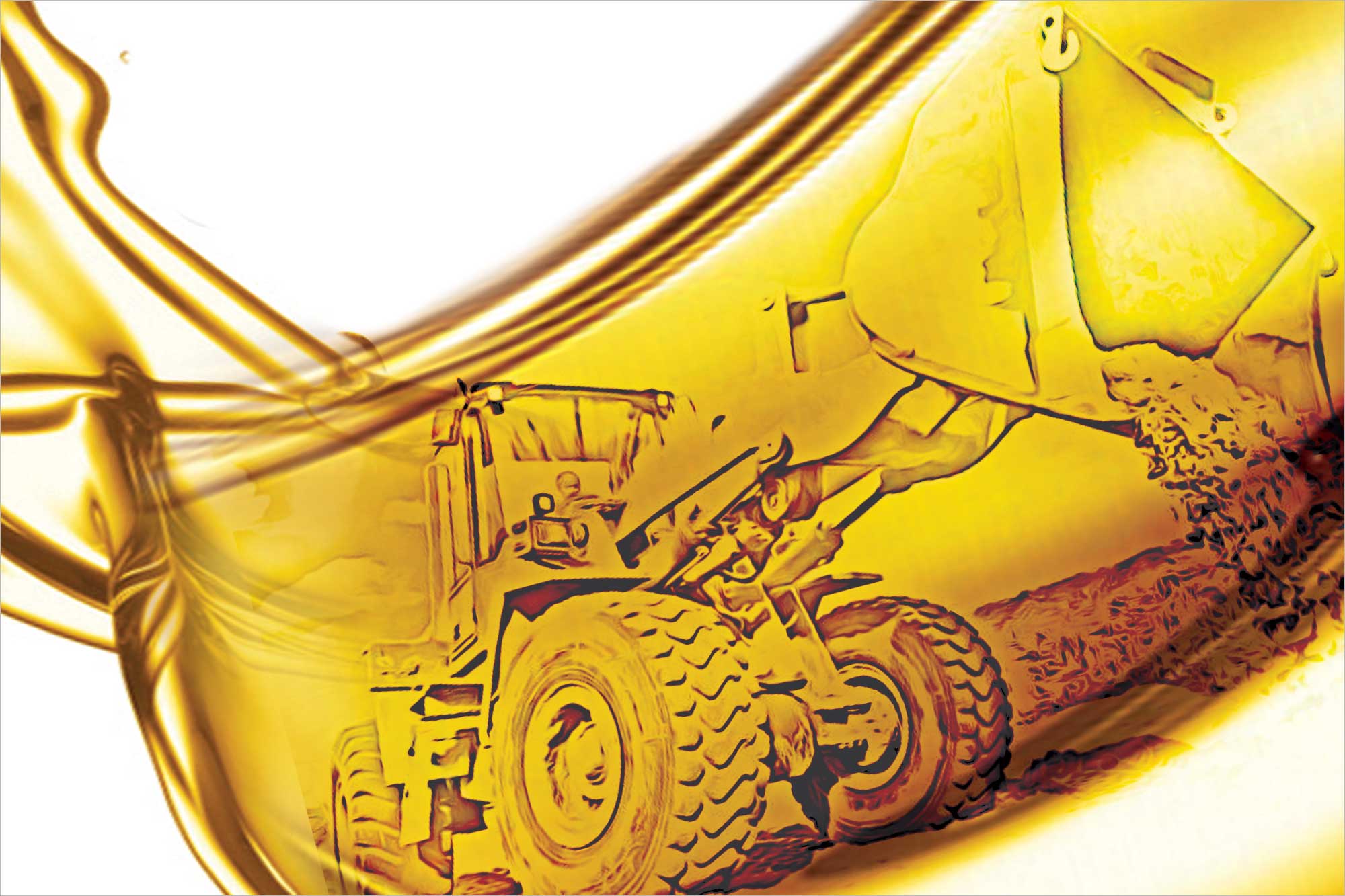
Maximise your stationary equipment performance with advanced technology lubrication
As the overall productivity and profitability of a mine site is directly linked to the reliability of equipment and as a result, it is vital that mining operators have equipment that functions at maximum efficiency. In the extreme conditions and rough terrain typical of mining sites, machine failure is a common problem, with the associated expense of equipment downtime impacting on operator profitability. For every day that unscheduled downtime occurs, operators stand to lose an average of USD 100,000.
Stationary equipment such as impact crushers, processing plants and conveyor belts play a key role at mining sites, with conveyor belts transporting raw materials such as coal or rocks outside of the facility or to processing areas and the crushers and plants reducing the materials to finer gradations.
High performance lubricants play a crucial role in ensuring consistent protection and performance of stationary mining equipment to minimise financial losses. However, with constant exposure to cement dust, mineral dust, coal dust, extreme temperature and heavy loads, lubrication of these expensive systems often present a unique challenge.
Enhanced performance
The good news is that advancements in lubricant technology, especially when it comes to fully-synthetic based products, has seen significant breakthroughs with regard to extending equipment life, oil drain intervals and improving the energy efficiency of equipment. Apart from improving productivity, these advanced, high-performance lubricants can also help to deliver associated safety benefits during any maintenance process.
Advanced high performance synthetic oils
Mobil SHC Gear, a high performance heavy duty gear oil, is an example of a synthetic lubricant that helps to increase productivity without compromising equipment protection or reliability.
Mobil SHC Gear oils are formulated to deliver a number of performance advantages when compared with conventional gear oil chemistries. For example, the high oxidation resistance enables extended oil life by up to six times compared with standard mineral gear and bearing lubricants, helping to reduced scheduled and unscheduled maintenance. As well as providing superior protection in challenging environments, in statistically validated laboratory tests and field trials, Mobil SHC Gear fluids exhibited energy savings of up to 3.6 per cent** compared with conventional oils. This further demonstrates the savings that can be made when in investing in an advanced, high performance lubricant.
Safely extending oil drain intervals
A case study on one of the leading cement manufacturing companies in India, exemplifies how ExxonMobil supported its customer in achieving significant energy efficiency benefits. At the plant, the company used Tata Hitachi Excavators for their mining, loading, digging, limestone handling operations in its premises. This excavator was being lubricated by conventional (OEM recommended) high viscosity index hydraulic oil (ISO VG 46) and a routine oil drain interval was in practice.
The cement manufacturer wanted to enhance the equipment productivity by extending oil drain interval and reduce fuel consumption, which would reduce the impact of its carbon footprint.
ExxonMobil recommended the use Mobil DTE 10 Excel 46, a high performance anti-wear hydraulic oil specifically developed to meet the needs of modern, high pressure, industrial and mobile equipment hydraulic systems.
The Tata Hitachi Excavator was identified with an aim to increase the oil drain interval (ODI), filter life and improved fuel efficiency. The excavator was registered on Mobil’s SIGNUM condition monitoring program to closely monitor oil and equipment health.
On observing the excavator and oil trend analysis through Mobil’s SIGNUM used oil program, it was witnessed that Mobil DTE 10 Excel 46 not only increased the oil drain interval from 1,500 to 3,000 hours, but also reduced the fuel consumption rate from 21.64 to 20.32 litres/hour.
The recommendation by ExxonMobil eventually increased the oil life by two times, filter life by two times and reduced fuel consumption by 6 per cent, without compromising on lubricant and equipment condition, saving Rs. 2,72,544 for each excavator per year.
Proactive maintenance strategies
In addition to using high quality synthetic lubricants to maximise the productivity of machinery and reduce costs, it is recommended that operators also incorporate an oil and equipment condition monitoring program. The oil analysis should include a measurement fluid viscosity, waste content, particle count and dissolved metals to determine how well the system is operating. Examining changes in the oil analysis data over time – known as trending – is necessary to assess the condition of the oil. By trending oil analysis data it is possible to proactively address the undesirable conditions before they become a problem.
For equipment maintenance professionals who want an effective oil analysis monitoring program, there is ExxonMobil’s proprietary online Signum oil analysis program. Signum oil analysis offers engineers immediate access and direct control of their lubricant sampling program. With a few keystrokes, users can manage their oil analysis needs enabling them to:• Update equipment registrations and select analysis options based on their equipment or maintenance needs• Track the status of samples at the lab• Direct actions based on analysis results and trends• Share critical results with colleagues in a secure, password protected environment.
Unearthing productivity and profitability
Technological innovation is driving the development of next-generation synthetic lubricants, which can offer significant performance enhancements for mining operators. These include improved efficiency, reliability and optimised equipment availability. By combining the use of high quality synthetic oils with an effective oil and equipment analysis program, mining operators can look to benefit from a quantifiable competitive advantage.
Energy efficiency relates solely to the fluid performance when compared with conventional reference oils of the same viscosity grade in gear applications. The technology used allows up to 3.6 per cent efficiency compared with the reference when tested in a worm gearbox under controlled conditions. Efficiency improvements will vary based on operating conditions and application.
Authored by__
Imtiaz Ahmed,
Asia Pacific Mobil SHC Brand Manager
Exxon Mobil Lubricants Pvt Ltd
Cookie Consent
We use cookies to personalize your experience. By continuing to visit this website you agree to our Terms & Conditions, Privacy Policy and Cookie Policy.