Strategies for success in multi-faceted construction projects
By Staff Report | February 13, 2025 11:20 am SHARE
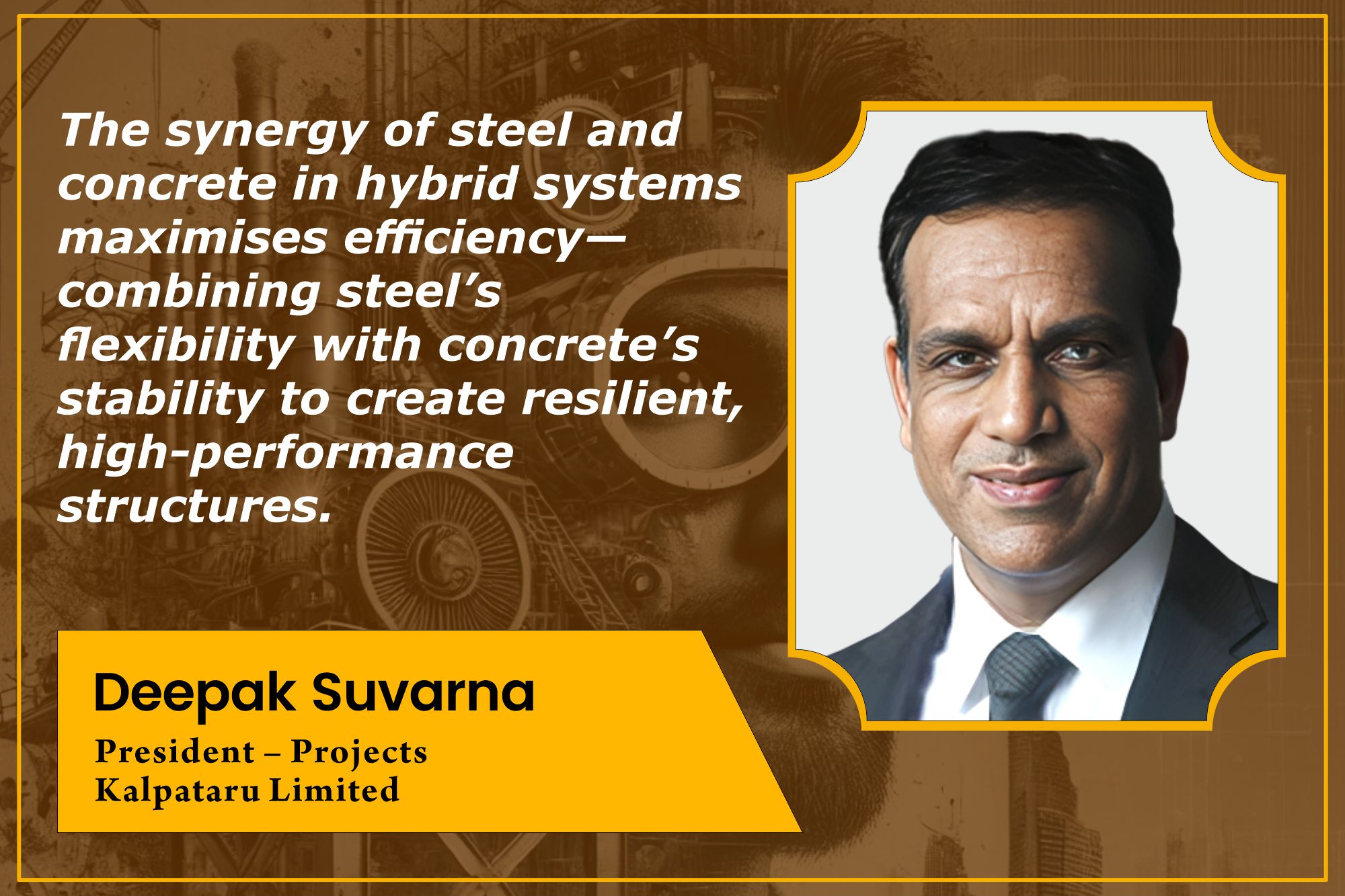
With extensive experience in handling a diverse range of projects, Deepak Suvarna of Kalpataru Limited explains how his approach to balancing project complexity, material selection, and innovative technologies ensures both high-quality and cost-effective construction solutions.
What challenges have you faced across different types of projects, and how do you approach overcoming them?
In my extensive experience across various types of projects across sectors, I’ve learned that each brings unique challenges. For multi-story residential buildings, the priority is ensuring structural integrity and seamlessly integrating services, particularly in dense urban environments. On the other hand, commercial developments require balancing flexible spaces with tight timelines and budgets.
When it comes to airport terminals, the sheer scale and complexity of construction make managing parallel systems a major challenge. Luxury hotels call for a delicate balance between design and functionality, while villas demand a high degree of customisation in both design and finishes.
Overcoming these challenges requires advanced project management strategies, continuous innovation, and leveraging the latest construction technologies. Ultimately, projects are delivered with a focus on quality, cost efficiency, and sustainability, ensuring that performance and aesthetics are never compromised.
How do you balance performance, cost, and sustainability when selecting materials for construction projects?
Material selection in construction is about finding the right balance between performance, cost effectiveness, and sustainability. Steel is a go-to for structural components due to its strength, while blended cement like PPC and fly ash-based cement offer durability and lower environmental impact. Concrete mix designs are customised to meet specific project needs for strength, durability, and workability, with long-term performance in mind.
Working closely with material suppliers allows for cost optimisation without sacrificing quality. Sustainable choices, such as recycled aggregates and alternative cement, help minimise the carbon footprint. High-performance concrete is used in critical areas, like commercial high-rises, to ensure buildings can handle environmental and load challenges. Reducing waste and optimising material use are key aspects of modern construction, contributing to the sustainability of the built environment.
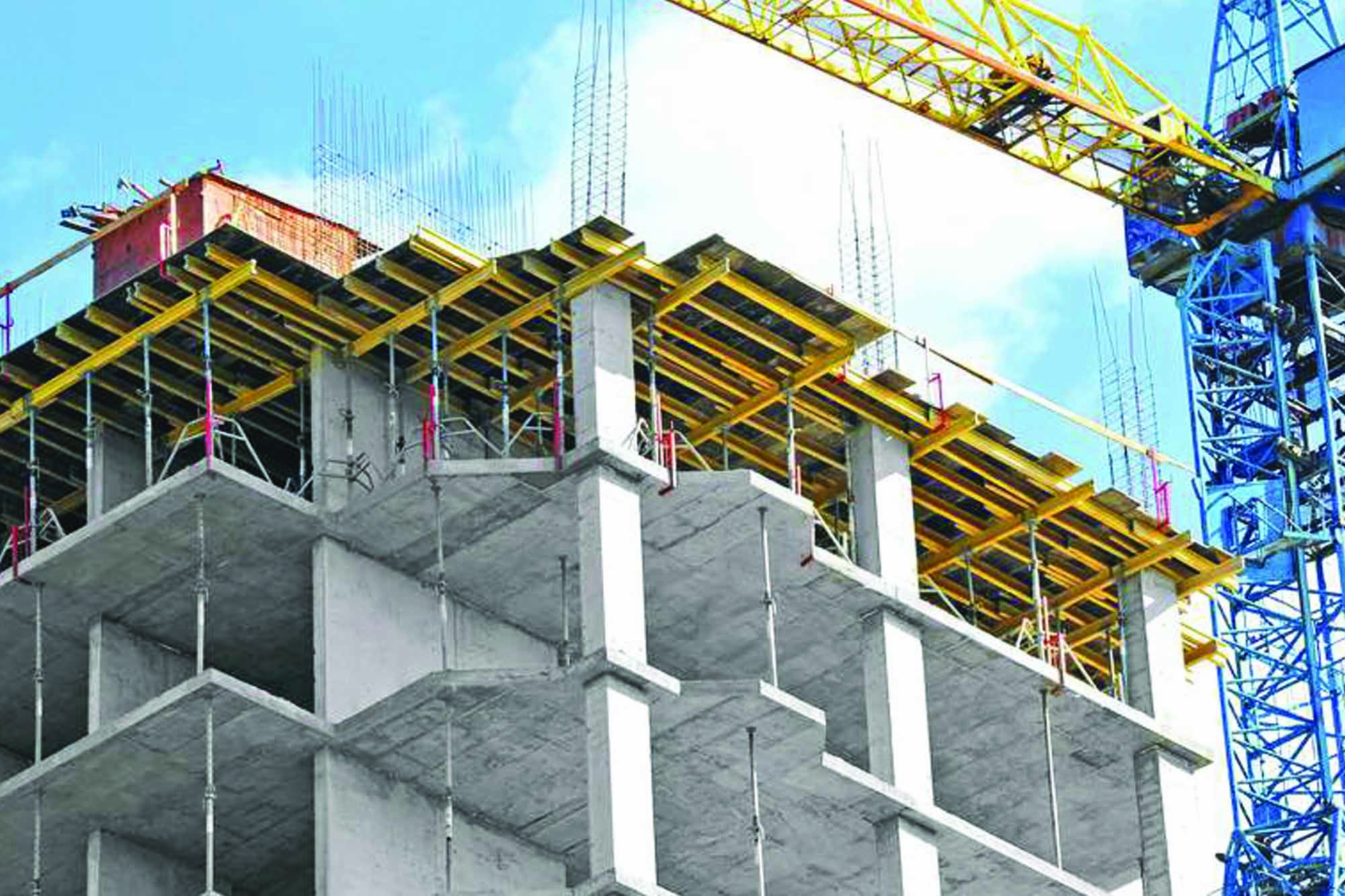
How has Pre-Engineered Buildings (PEB) technology impacted the efficiency and scalability of commercial and industrial projects?
Adopting pre-engineered buildings (PEB) technology has transformed commercial and industrial developments. PEBs provide speed and cost efficiency through modular, prefabricated components, significantly reducing construction timelines and labour costs.
This technology suits projects like warehouses and industrial parks, where scalability and flexibility are critical. Off-site fabrication ensures better quality control, reduced on-site labour, and faster installation. In industrial parks, PEBs have reduced project delivery times by up to 20% compared to traditional methods.
PEBs allow for future expansion with minimal disruption, making them a practical solution for businesses focused on long-term growth. PEB technology’s cost-effectiveness and quick execution continue to fuel its adoption in various commercial and industrial developments.
How does collaboration with material suppliers enhance the performance and sustainability of concrete mix designs?
Collaboration with material suppliers is essential for developing optimised concrete mixes that provide strength and workability. Tailored mix designs ensure the concrete meets specific project requirements, such as compressive strength and durability for high-rise buildings or infrastructure projects. The quality of materials, sourced carefully, plays a critical role in mixed design parameters.
Incorporating sustainable materials like fly ash and slag makes the concrete more environmentally friendly and cost-effective. Using recycled aggregates further enhances the mix’s sustainability. Supplier collaboration helps maintain consistent concrete quality, especially for projects with strict performance criteria.
This optimisation of concrete mix design has resulted in cost savings while upholding high structural safety and longevity standards. It has also contributed to minimising waste and improving overall construction efficiency, aligning with sustainability goals.
What benefits do hybrid systems of steel and concrete offer in large-scale developments?
Combining structural steel and concrete in hybrid systems enhances efficiency and performance in large-scale developments. Steel is ideal for long spans and flexible structures, while concrete provides compressive strength and stability. Composite structures reduce material weight while maintaining high load-bearing capacity in high-rise buildings. The integration of these two materials requires careful design to ensure optimal performance. Typically, steel is used in the core structure, while concrete is used for floors, foundations, and slabs.
This combination offers significant time and cost savings, improved structural efficiency, and design flexibility. Using high-strength steel and concrete ensures buildings meet aesthetic goals while being durable and resilient. Composite structures ensure long-term performance in demanding environments like commercial complexes and residential towers.
How do BIM and lean construction help optimise construction workflows?
Integrating Building Information Modelling (BIM) and lean construction principles has revolutionised the construction process. BIM enables real-time collaboration among project teams, improving coordination, minimising errors, and enhancing schedule management. With features like clash detection, BIM allows for earlier identification of design issues, saving time and reducing costs.
Lean construction principles further optimise the process by focusing on waste reduction, resource optimisation, and process efficiency. BIM and lean construction streamline workflows, reduce delays, and ensure projects are completed on time and within budget.
These technologies have significantly improved cost-effectiveness, enhanced overall project efficiency, reduced rework, and ensured higher-quality outcomes. The continued adoption of these technologies shapes modern construction practices and drives better results for developers, contractors, and clients.
How do you incorporate sustainability into your construction projects?
Sustainability is a priority in modern construction, and adopting eco-friendly materials plays a crucial role in reducing buildings’ environmental impact. We use recycled steel, fly ash-based cement, and slag cement to reduce carbon footprints while ensuring structure durability and strength.
The use of sustainable building materials not only supports environmental goals but also contributes to long-term cost savings. Additionally, we incorporate solar energy systems, rainwater harvesting, and energy-efficient building designs to reduce operational energy consumption and enhance sustainability.
Pursuing green building certifications like GRIHA and LEED reflects our commitment to environmentally responsible construction. These efforts align with broader goals of reducing energy consumption, minimising waste, and fostering eco-friendly communities. Sustainability practices continuously evolve to meet the growing demand for green buildings, ensuring long-term value for developers and occupants.
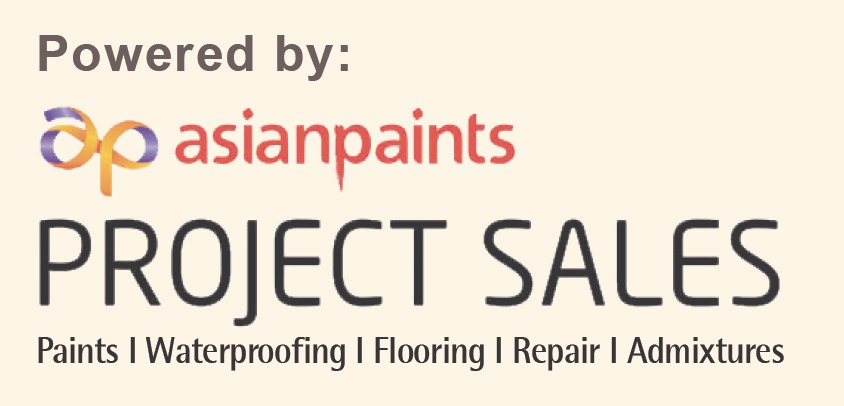
Cookie Consent
We use cookies to personalize your experience. By continuing to visit this website you agree to our Terms & Conditions, Privacy Policy and Cookie Policy.