Surface preparation is the most important requirement for coating
By Edit Team | July 10, 2020 10:29 am SHARE
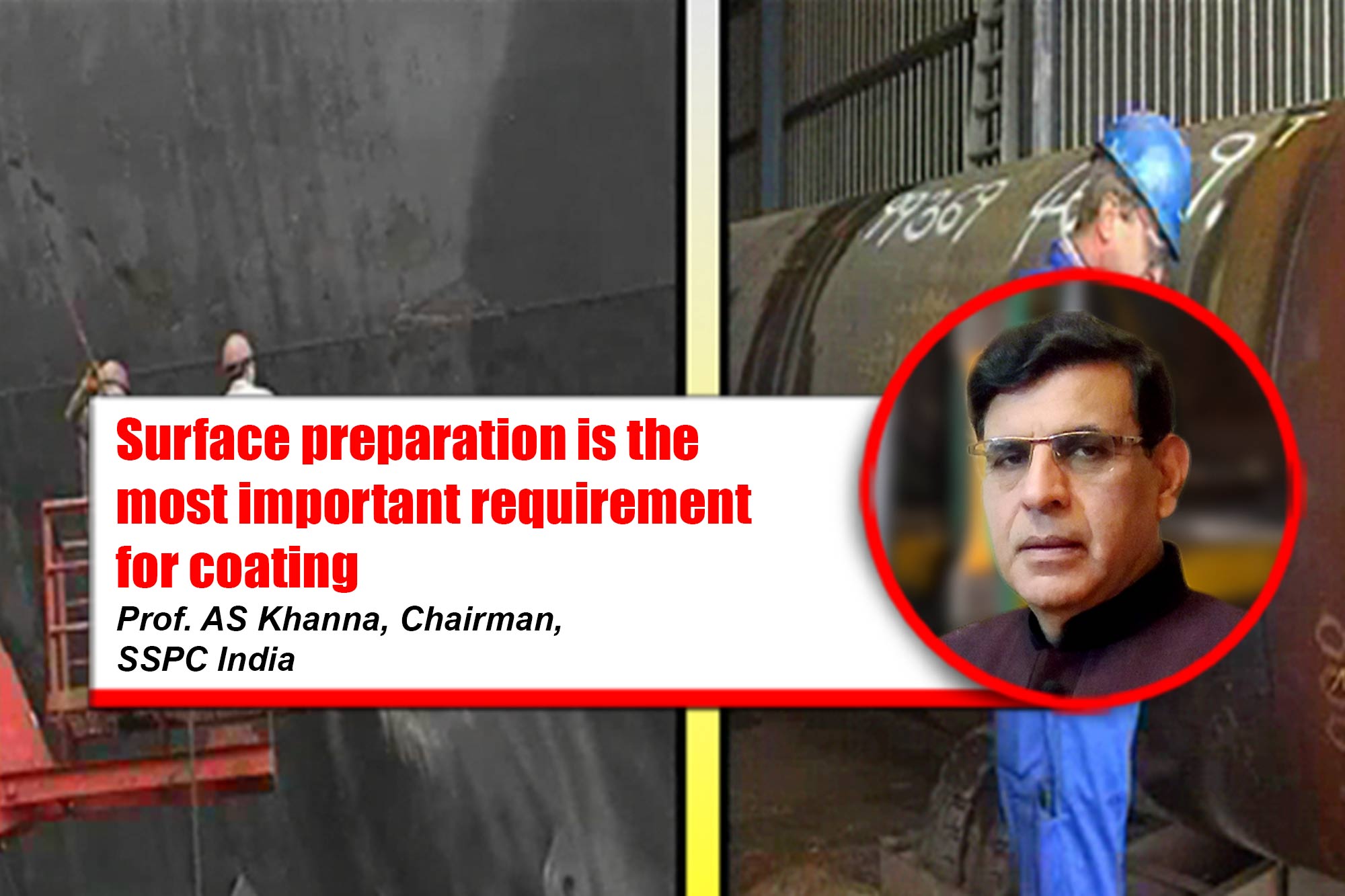
Surface preparation not only removes dust, grease and other impurities on the surface but it also gives a good roughness which anchors the paint and gives longevity says Prof. AS Khanna, Chairman, SSPC India.
The use of metals in industries as also infrastructure is well known, with the onset of monsoon what are some steps one can take to ensure they remain free of corrosion?
Corrosion of metals usually happens in monsoon due to a high degree of wetness. It is one of the prime factors responsible for the corrosion to initiate. The humidity level of 60 per cent is enough to initiate the corrosion process and pollutants such as chlorides, carbon dioxide and/or sulphur dioxide further aggravate this situation. Thus, pure steel parts and poorly coated steel parts generally undergo corrosion in monsoon. This is the reason; many bicycle parts such as chain, mudguards, steel window panes get corroded very quickly.
The best method to protect these parts is to coat with suitable paint before the monsoon, but if it was not done then there are other possibilities to prevent corrosion. The simplest one is to apply normal grease to all steel parts throughout the monsoon and oils such as linseed oil which if applied on steel parts, corrosion can be prevented. On parts that have been corroded already, there are a few rust preventers or rust primers, which are easily available in the market.
When it comes to the application of protective coatings, what are some of the important points to be noted to choose the right fix?
The application of coating does not mean buying paint and brush from the market and start applying on the object. The paint application has four parts which are as follows:
- Selection of paint for a particular application based upon the environment
- Surface preparation
- Application procedure: Primer, intermediate and top coat
- Quality assurance
Various locations in the universe are divided into five categories in terms of the severity of corrosion. As per the ISO standard, these categories are C1, C2, C3, C4 and C5 based upon, very mild environment such as rural (C1), a small town with limited industry (C2), big-city environment with several industries and vehicular transportation with high humidity (C3), onshore (C4) and offshore (C5). For each category, a proper paint system is selected. A wrong selection may give poor life to the coated object.
Surface preparation is the most important requirement. About 90 per cent of paints fail because of poor surface preparation. Surface preparation not only removes dust, grease and other impurities on the surface but it also gives you a good roughness that anchors the paint and gives longevity.
Various paint systems are divided into the main paint system which gives corrosion resistance and long durability called the intermediate paint. To add support to main paint, a suitable primer, based upon some corrosion protection principle such as zinc-based primers, help to save the metal from corrosion in case the main paint is damaged due to abrasion. Top paints are sometimes required to save the intermediate paints from the environment such as sunlight, rain or snowing.
While doing all this it is important to measure the coating drying time before application of the new paint and keep a record of all and the thickness of each coat and total thickness.
Can these be applied by anyone or do you have trained applicators to do the job?
Usually, if a person reads basic instructions and follows it, he can apply to small areas at home and offices. But when we talk of industrial painting and big building painting, where guarantee and warranty class are the requirements; paint application is usually done by trained paint contractors and paint applicators (technicians), paint supervisors, who do online monitoring and supervise every action right from surface preparation, drying time, coating intervals etc. And quality assurance team, which sets the procedure of coating and checks the quality of work daily, helps in overcoming coating queries during application and maintains the complete record. For big structures, the safety of people and the use of scaffolding and temporary structure knowledge is also an important responsibility.
How long does this protection last? What should be the frequency of re-application to ensure all-round protection throughout the year?
As indicated above, the selection of the coating for a particular environmental category decides the durability of the coating. And application procedure including surface preparation is another important criterion and based upon this, the recoating period is decided. However, due to changes in environmental factors, this may change. Thus periodic monitoring of the coated surface is usually carried out, either by visual methods or by online monitoring gadgets, which provides the information about the coating deterioration if any and may indicate whether deterioration is faster than predicted. Further, the location and extent of damage also decide whether the whole surface should be repainted or only touch down or partial coating is enough.
How are you managing manufacturing and after-sales support in the post lockdown?
People are still observing the situation on the ground as it has been just 15 days since the lockdown has (partially) lifted. The manufacturing will depend upon the demand as well as on existing stock in the godown and another factor will be to maintain social distancing within plants and administrative processes.
Cookie Consent
We use cookies to personalize your experience. By continuing to visit this website you agree to our Terms & Conditions, Privacy Policy and Cookie Policy.