Surfin’s high TACT CED production line: An idea tool for seamless coating
By Edit Team | October 31, 2019 9:15 am SHARE
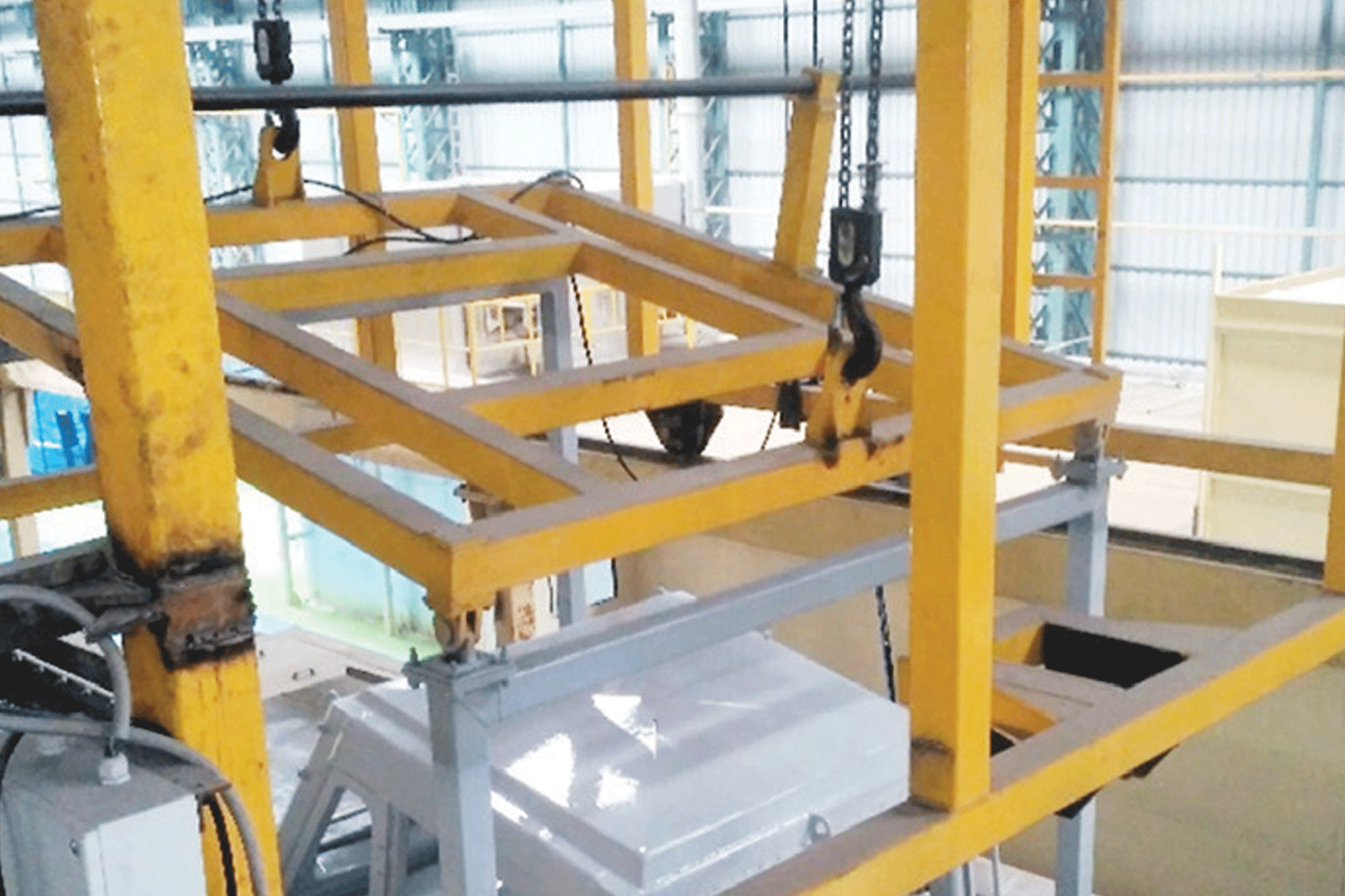
Concept
Designing High TACT Cathodic Electro- Deposition (CED) Production Line (60 Min. Tact) With Optimised Connected Load.
The Component-
‘Off-road Truck Rollover Cabin’
PAINT FILM THICKNESS : 30-40 Microns
PARAMETER VALUE
AREA TO BE COATED 40 Sq mtr
FILM THICKNESS 35 Microns minimum
PAINT SHADE GREY
TACT 60 Minutes
COATING TIME 8 Minutes
BATH Nv 16%
The Process:
In case of CED coating, standard process followed is 3 minutes coating time and fixed voltage varying from 150V to 300V. In a typical dunk type CED coating the system DC voltage is ramped up to set value within 10-15 seconds based on the plant design. Due to application of voltage initially current increases and then due to film resistance it starts dropping down at the end of the coating cycle. Standard cycle time for coating is @ 3 minutes.
With above standard process the rectifier capacity for this application would have been in the range of 600Amps-300V. This increases connected load and power consumption for customer and same results in up paying higher expenses due to higher connected load. However, the actual usage of @ 13% as the cycle time is 60 minutes and the voltage application time is 8 minutes. This means rectifier remains idle for most of the time.
The system designed by SURFIN is different than a conventional method followed by most of the designers who usually follow constant voltage. Instead SURFIN has chosen system for constant current and variable voltage.
After detailed calculations we reach to conclusion that the average application current required to coat 40 Sq mtr area of cabin in 8 minutes is between 80 to 100 Amperes only as against 600Amps of initial spike in current with constant voltage method. SURFIN has also installed current feedback system on the rectifier. The system designed works in a manner that it starts applying voltage from zero and increases gradually. Once system receives feedback from the field that current has reached the set value (in this case it was 100 Amp) it holds the voltage.
Due to film build up and the resistance offered the system current starts dropping down to @ 85 Amperes along with feed back to the control unit. Post this feedback rectifier increases the voltage from the previous hold value till current reaches to set value of 100 Amp. This is maintained for 8 minutes application time. After completion of 8 minutes cycle rectifier is switched off automatically.
Using constant current method SURFIN has achieved following results
in favor of customer:
- Instead of constant voltage, this constant current system has reduced rectifier capacity from @ 600 Amp-300V to 250 Amp -300V. This has reduced the connected load drastically and bringing down fixed power cost.
The constant current method achieved film thickness variation of @ ±2.5 microns on entire area of 40 sq. meters, thus saving in paint cost. - Smooth finish of coating as the current density maintained is almost constant right from starting of the process till
completion of coating. - Allowing flexibility of higher TACT through increased coating time.
- Six-timeramp-up in future production capacity using same rectifier.
- Optimization in power consumption through reduced rectifier losses through reduction in winding loss.
- Further the same equipment was successfully tried out, under SURFIN’S supervision, for larger cabin having 85 Sq mtr area in 8 minutes. Application current band was increased from 80 – 100 Amps to 160 – 180 Amps.Authored by:
Mr. Umesh Phadke (Director)
Surfin Coating Systems Pvt. Ltd.
www.surfin-india.com
Cookie Consent
We use cookies to personalize your experience. By continuing to visit this website you agree to our Terms & Conditions, Privacy Policy and Cookie Policy.