Sustainability in PEBs
By Staff Report | December 27, 2024 6:49 pm SHARE
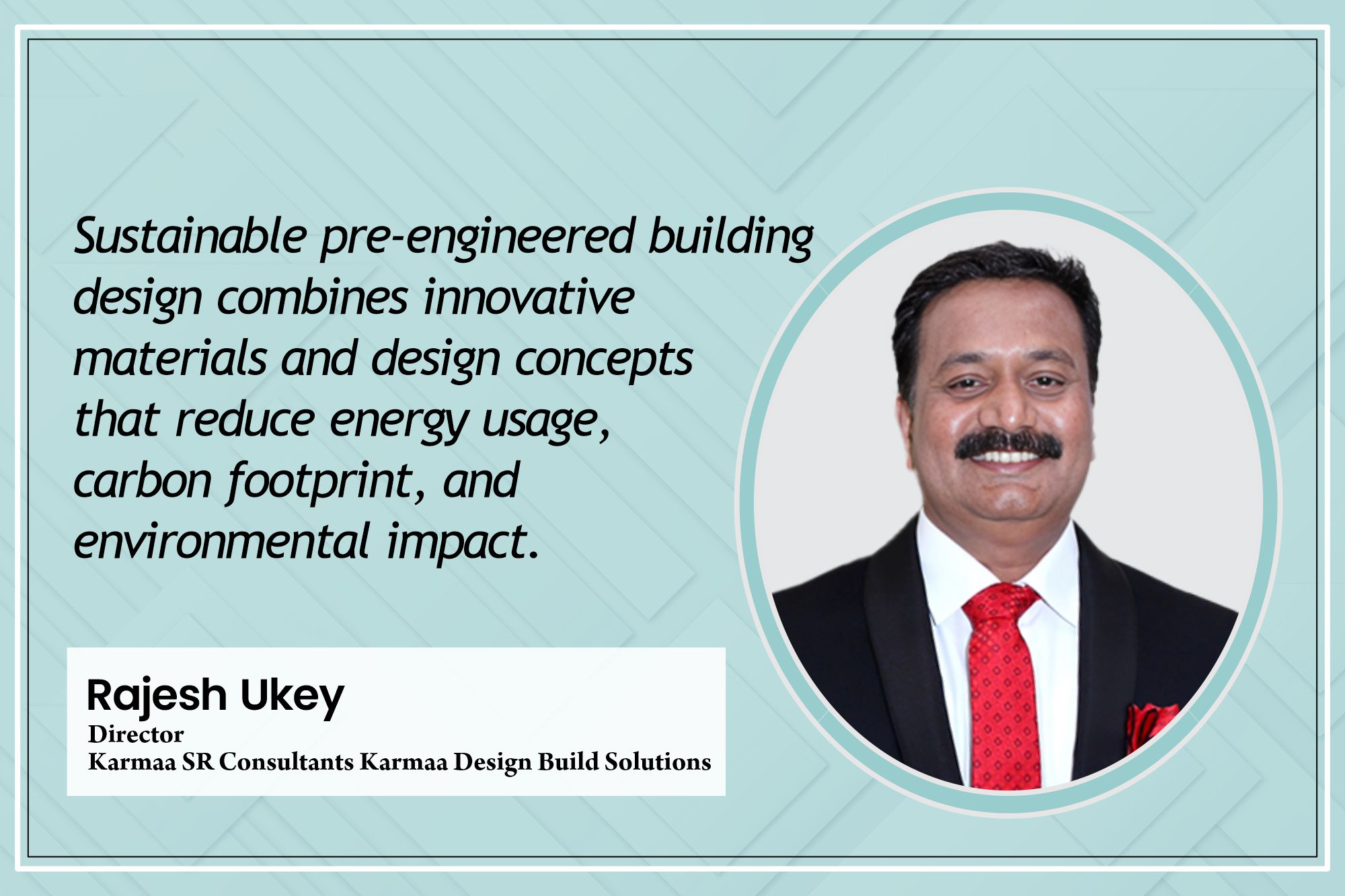
This article looks at creative ways to improve PEB systems, such as finite element analysis, insulated metal panels, and life cycle cost evaluations, to ensure efficiency, sustainability, and reduced material and energy use.
How can advanced structural analysis and design techniques optimise pre-engineered building systems?
Advanced structural analysis and design approaches are critical to optimising pre-engineered building systems. Finite element analysis, topology optimisation, and sophisticated load-bearing calculations can reduce material consumption while increasing load-bearing capacity and performance. The result is a more cost-effective, efficient, and sustainable building that operates well throughout its existence. These strategies enable engineers to achieve a compromise between safety, functionality, and material efficiency, guaranteeing that PEBs can fulfil modern standards while minimising cost and environmental effects.
What can improve energy efficiency, reduce carbon footprints, and achieve sustainability in pre-engineered building designs?
High-performance thermal insulation materials installed in walls and roofs can greatly limit heat transfer. Insulated Metal Panels (IMPs) combine structural strength and thermal insulation, improve thermal performance, and eliminate the need for extra heating and cooling systems. Efficient roof solutions with a high Solar Reflectance Index (SRI) can reduce heat absorption. Furthermore, building orientation and natural ventilation are important; incorporating skylight or daylight panels and louvres on wall sheets promotes cross-ventilation, while passive design solutions decrease direct exposure to peak sunlight on the structure’s principal axis.
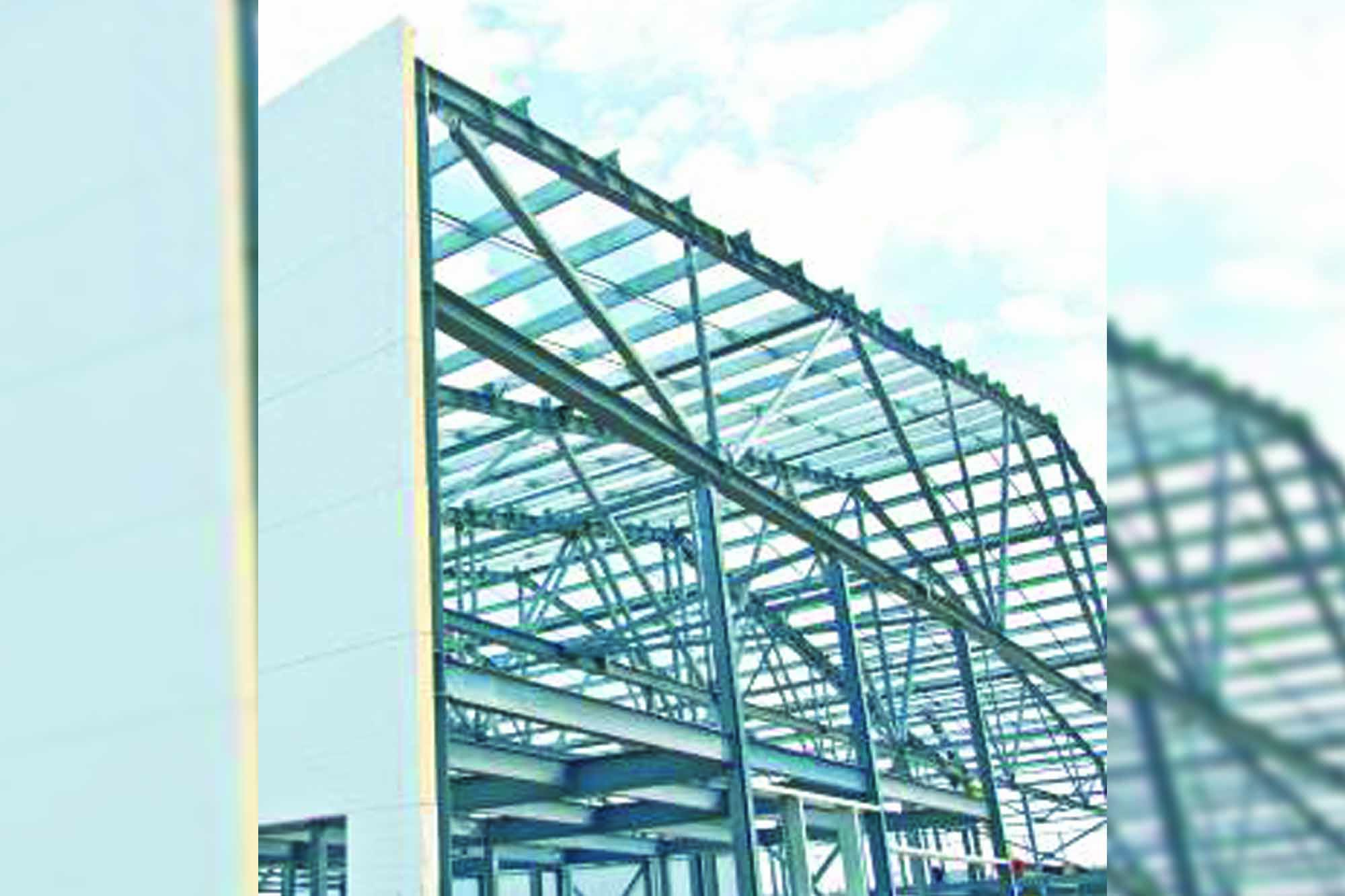
How can we perform a comprehensive life cycle cost analysis to evaluate the economic viability of pre-engineered buildings?
This comprises original construction, maintenance, operational, and end-of-life expenses. The important parameters that must be addressed are the building’s performance across its life cycle, initial cost, operating and maintenance costs, and comparative analysis. By considering all of these elements, you can acquire a thorough picture of a pre-engineered building’s overall life cycle cost, which will aid in determining its long-term economic viability.
What is the ideal balance between customisation for specific project needs and standardisation to streamline manufacturing and construction?
The ideal balance between customisation and standardisation in PEB systems is achieved by standardising key elements such as structural components, materials, and basic modules to reduce costs and construction time while allowing for strategic customisation in areas affecting functionality, aesthetics, or site-specific conditions. Flexibility in design is critical for accommodating future needs or modifications while maintaining overall process efficiency. This approach ensures that PEB structures can be adapted to unique project requirements while maintaining cost-effectiveness, efficiency, and mass production speed.
How can we improve the seismic resilience of pre-engineered buildings?
Improving the seismic resistance of pre-engineered buildings in earthquake-prone areas entails combining new design principles, advanced materials, and cutting-edge construction methods. Key solutions include increasing flexibility through base isolation, dampening, and structural redundancy and adopting materials with high strength and energy dissipation. With careful planning, prefabrication, and deliberate retrofitting, PEBs can be much more resistant to seismic occurrences, potentially saving lives, reducing damage, and enabling faster recovery in post-earthquake circumstances.
For more information, visit: https://www.karmaasrconsultants.com/
Cookie Consent
We use cookies to personalize your experience. By continuing to visit this website you agree to our Terms & Conditions, Privacy Policy and Cookie Policy.