Sustainable scaffolding and formworks are reforming Indian construction
By Edit Team | October 7, 2023 2:46 pm SHARE
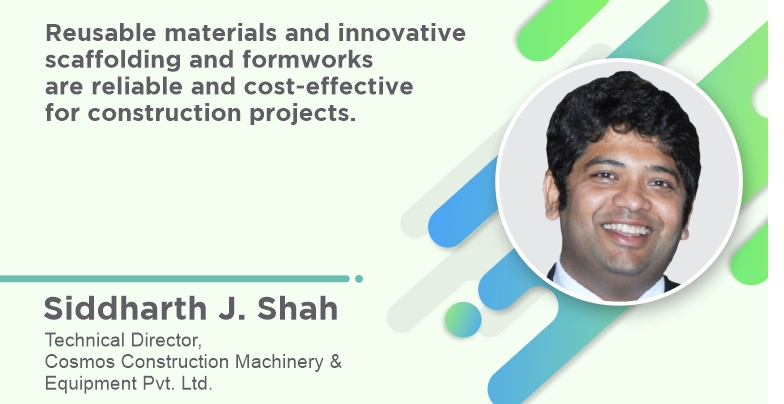
Reusable materials and innovative scaffolding and formworks are reliable and cost-effective for construction projects.
Siddharth J. Shah, Technical Director of Cosmos Construction Machinery & Equipment, suggests that by refurbishing the material after it has been used in the construction of, for instance, five 20-story buildings, it can be effectively reused up to 100 times for various construction projects, with only minor additions of new materials and modifications required.
How have innovations in scaffolding and formwork structures contributed to more sustainable and cost-effective projects?
The innovation of scaffolding and aluminium formwork using a monolithic formwork system in building construction ensures the casting of the entire floor, i.e., slab, walls, staircase, and passage, in a single time with a 10-day cycle, thereby completing the whole structure of a building floor. Using this, the Aluform panels for walls, beams, staircases, passages, slabs, etc., are erected, as they are lightweight compared to steel structures. This has helped achieve dimensional accuracy, resulting in fair-finished concrete, reduced the need for skilled labour, allowed for plumbing and electrical conduits during concreting, and eased the de-shuttering process using proper tools and tackles.
We can ensure precise alignment of the door frames and then continue with the interior finishing. This formwork can be employed for large and small projects to complete buildings with varying floors at different elevations.
The construction of high-rise buildings was inevitable and necessary to reduce the use of scaffolding for external support and to retain the concrete in place, which was used to increase the cost of scaffolding and formwork due to ply and steel. However, after using aluminium formwork for monolithic structures, the inbuilt wall ties and pin-wedge retain the mould, making external support cost-effective in projects by maintaining the reusability of wall ties and PVC sleeves.
How have recycling abilities in modern scaffolding and formwork systems reduced environmental impact?
There is no need to cut down trees and bamboo using aluminium and steel in the structure where no wooden support and wooden formwork are required. The existing aluminium and steel materials can be recycled to create new extrusions. Moreover, using aluminium as a mould for the entire building structure leads to green building certification. There is no use of mud blocks, wood, ply, or bamboo.
How do advancements in materials and design contribute to overall sustainability?
Aluminum formworks for monolithic structures employ reinforced concrete wall slabs and beams, reducing concrete design sections in buildings. It enhances carpet area, standardises material use through AutoCAD programmes, maintains consistent floor-to-floor heights, sills, balconies, and windows, while reusing staircase materials with uniform riser height, treads, and sunken depths for repetition.
How are recyclability and sustainability prioritised in scaffolding and formwork material production and lifecycle?
The material can be reused up to 100 times in construction, allowing for multiple buildings with 20 stories each. It can be refurbished and reused another 100 times with minor new material additions and modifications, making scaffolding and formwork user-friendly even for unskilled labor. The process involves removing concrete, treating it with chemicals to remove concrete particles, and refurbishing the panels to look like new without compromising their strength.
How do manufacturers balance affordability and sustainability in scaffolding and formwork for large construction projects?
Manufacturers offer comprehensive services for accurate material use as per drawings, including guarantees for repetitions, efficient AutoCAD designs, minimising support and material waste with cost-effective accessories, and ensuring reusability. They also provide guidance for plumbing, electrical work, and grooves; use non-removable stickers for panel identification; optimise pieces per square meter for handling; and maintain stock for timely delivery. These measures reduce labor costs, increase slab cycle time per floor, and improve labor efficiency. Proper management training for panel installation and removal extends the material’s life, affordability, and cost-effectiveness compared to traditional formwork materials, making them a more economical choice for quality, time, and usage considerations.
Cookie Consent
We use cookies to personalize your experience. By continuing to visit this website you agree to our Terms & Conditions, Privacy Policy and Cookie Policy.