Tailoring coating formulations to meet infrastructure needs
By Edit Team | April 6, 2024 1:00 pm SHARE
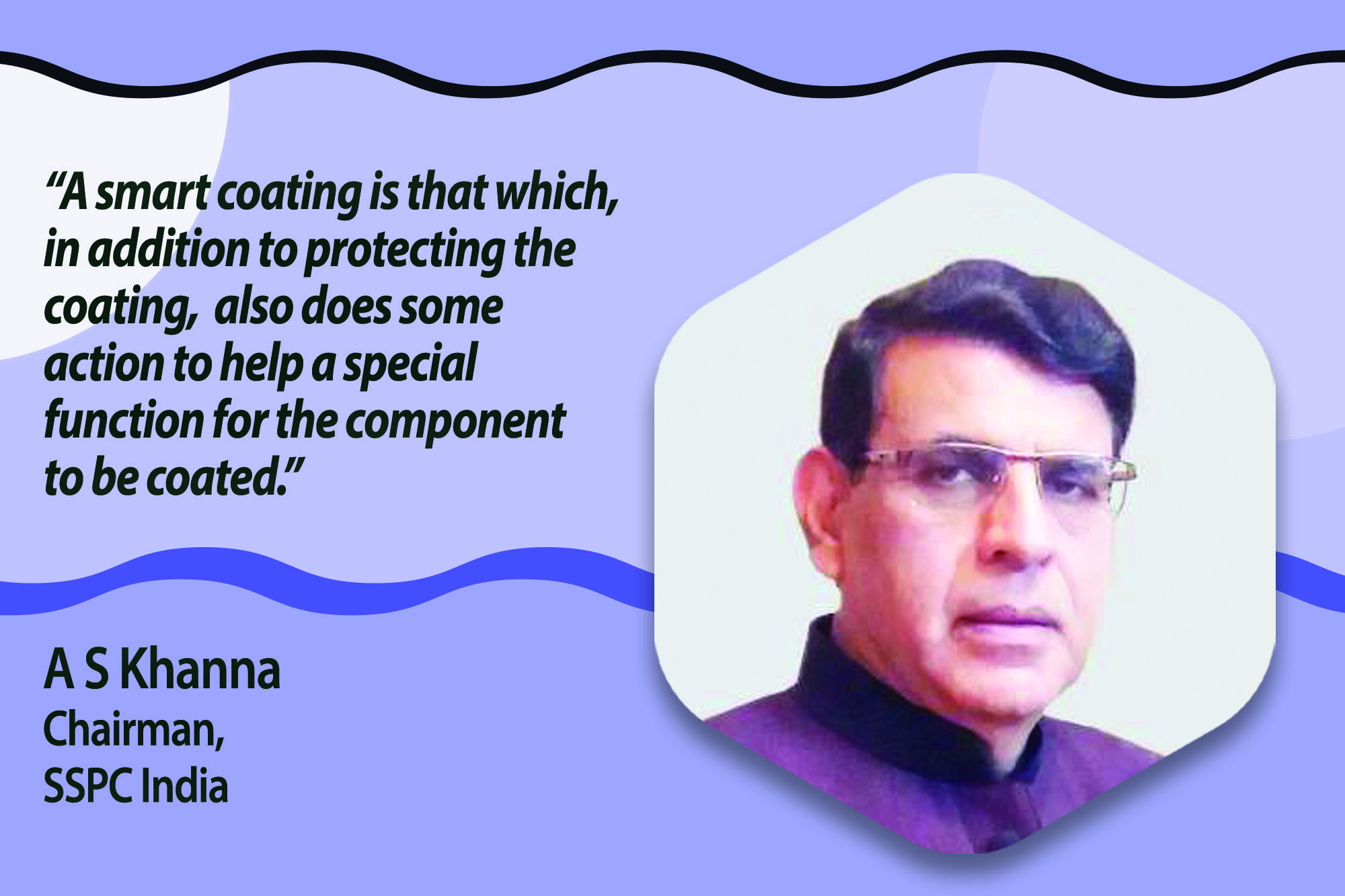
The formulation optimisation process for coatings in construction and infrastructure projects is crucial for meeting specific requirements. Here, Prof. A S Khanna explains how coatings are tailored to extend the longevity of infrastructure assets and enhance their performance.
What are some of the most common challenges faced in the construction and infrastructure industries regarding corrosion protection and surface coatings?
Infrastructure is the base of any civilisation, country, or city. Its durability and functionality are perhaps of utmost importance. A few infrastructure projects include roads, flyovers, bridges, public buildings, sports complexes, hospitals, Railway stations, and Bus Stations. These structures must be free from any structural damage, leak, or look shabby due to corrosion. Structural strength and other vital parameters are considered in the design. However, the problem of proper functioning, leakages, and corrosion requires special attention. Corrosion, for example, requires an appropriate selection of paints with durability and freedom from fading. Waterproofing strategy is essential. To select paint coatings, the first step is to categorise the area in terms of corrosion categories, C1, C2, C3, C4, and C5, and then decide the paint coatings suitable for that category of corrosion level. These categories are made per ISO 2223 and 2224 standards, taking care of humidity, salinity in the air, and SO2 level. The second necessary precaution is proper paint application, starting from the correct surface preparation and application of different layers of paint in terms of appropriate drying and re-coating intervals. Simple paint systems such as alkyds and acrylics suit C1 and C2. However, epoxy-based paints with higher thicknesses are used in C3 and higher corrosive environments such as C4 and C5. Flyovers in populated cities such as Mumbai, Chennai, Kandla, and Chennai need anti-carbonation coatings to save the structure from CO2 emitted regularly from vehicles. Fire retardant coatings are usually applied on all steel structures in many public buildings such as Malls, Railway stations, bus stations, etc. Periodic monitoring and maintenance is an essential part of post-construction activities.
Could you elaborate on the process of formulation optimisation for coatings tailored to meet specific requirements in construction and infrastructure projects?
There are various kinds of coatings used in infrastructure development. The first requirement is to protect the steel rebars used in the infrastructure. It is now estimated that in a city or town near the coastal area, a standard black steel bar gives a life of not more than 7-10 years. Hence, coated bars are used, which enhance the life of these bars to 30 years, 60 years, and 120 years. Coatings such as galvanisation and fusion bond epoxy help extend their life by 75 and 60 years, respectively. Using stainless steel can extend the life further to 120 to 150 years. Both galvanised bars and FBE-coated bars are readily available in India.
In the same way, the use of anti-carbonation coatings on the concrete cover of the reinforced bar helps prevent or delay the diffusion of pollutants through the concrete cover and thus enhances the life of the RCC structure.
The use of a three-layer coating system with a zinc-based primer, 150-300 microns intermediate layer, and top aliphatic polyurethane can give a life of 6-8 years in a C4 environment. Longer life (8-10 years) can be achieved if an Inorganic Zinc Silicate (IOZ) primer is used in place of a zinc-rich primer, and using Zinga primer or ZRC primer can give a life longer than 12 years.
In what ways do specialised applications of coatings play a crucial role in enhancing the performance and longevity of infrastructure assets, such as bridges, pipelines, and industrial structures?
The following figure gives a list of various coatings where just a change in primer, with no change in the intermediate or top coat or their thickness, changes coating life from 2-3 years to 25 years. Thus, using different kinds of primers with varying Zn concentrations can help enhance the life of the coating.
One of the best examples from this table is the coating on windmills, where the expected life is 40 years. Two technologies are used: IOZ with an epoxy intermediate coat and aliphatic PU, which gives a life of 10-12 years, or thermal sprayed zinc layer (150 microns) followed by an epoxy sealer coat and top aliphatic PU, which gives a life of 25 years.
How can emerging technologies, such as nanotechnology and intelligent coatings, be integrated into coating solutions to improve performance and efficiency in construction and infrastructure projects?
Nanotechnology is the most powerful technique for enhancing the properties of coatings, and it also helps reduce the consumption of raw materials in paint formulations. Using nanotechnology, it is possible to make several smart coatings. In addition to protecting the coating, a smart coating is one that does some action to help a unique function for the component to be coated. For example, self-cleaning coatings, self-healing coatings, anti-dust, and anti-fouling, to mention a few.
The use of nanomaterial, such as nano-pigments and nano-additives, helps in enhancing the properties of coating by a uniform distribution of the particles, which, as a result of their large surface area and optimum distribution, help in enhancing corrosion protection, enhance mechanical properties, and introduce unique properties such as anti UV. Nanotechnology in paint works in three steps: a) to identify a suitable nanoparticle that can enhance a particular property you are looking for, b) measure its correct size and shape using SEM/EDAX, TEM, etc., and c) find the optimum loading of this nanoparticle which gives the best property enhancement. An epoxy base coating was made by adding a special nanoparticle that enhanced the corrosion property of an epoxy coating to resist corrosion from pH 0-14 and enhance its temperature resistance from 110oC to 250oC.
Can you discuss the role of coatings in waterproofing applications, such as in constructing tunnels, underground structures, and water-retaining structures?
Waterproofing protects a concrete wall, floor, or roof from leaking. Concrete, by definition, is porous. However, in a typical environment, there is a good balance between the moisture retained in the concrete and that surrounding the structure. In case there is additional wetness, either due to extra water retained on the floor or roof or due to high humidity, the concrete continuously absorbs water, and its balance is disturbed, releasing extra water, leading to leaking. So, waterproofing stops extra moisture from entering the concrete wall, floor, or roof. How is it done? This can be done for a brand-new concrete structure by applying an epoxy-based coating that tends to stop the grace of moisture into the concrete. However, on roofs or walls coming out from wetlands, you must stop the water in grace using additional methods. Simply adding a few percent, 15-30 percent of a resin in concrete reduces the porosity, which helps control initial leakage. However, to protect a leaking structure, special treatment is required.
We have a product called WP51. It is an acrylic-based coating modified by nanoparticles. It protects the leaking wall with a 3-layer or 5-layer protection: the first layer is the absorbed layer, where this product, mixed with water, is applied loosely to the surface. This helps in blunting the micro-pores. The next step is to seal the cracks or big holes by widening these cracks and filling them with this compound mixed with 50% cement. After it fully dries, it is sealed with a uniform layer of this compound mixed with 50 % cement. Made in an easily spreadable layer with water twice. In 5 layers, an additional reinforcing layer is added. Such a coating has helped seal the leakages on roofs. It can stop seepage from wet earth and be a good coating for tunnels and underground rail applications.
How important is collaboration between academia, industry, and regulatory bodies in driving innovation and advancement in coating solutions for construction and infrastructure projects?
Collaborations and advice from academics and R&D labs are the only way to update the knowledge of real problems due to corrosion. Corrosion is a little-understood subject. More than theoretical knowledge, one has to understand this subject on a practical level. This can happen if people in the steel industry, real estate, refineries and chemical plants, shipping, and offshore structures engage in regular refresher courses and practical training. In addition, they can discuss corrosion-related problems with experts in IITs and Good R & D labs and find a suitable solution to understand and the application procedure.
Cookie Consent
We use cookies to personalize your experience. By continuing to visit this website you agree to our Terms & Conditions, Privacy Policy and Cookie Policy.