Technology Disruption is Revolutionising Welding & Cutting Business
By Edit Team | March 8, 2022 10:11 pm SHARE
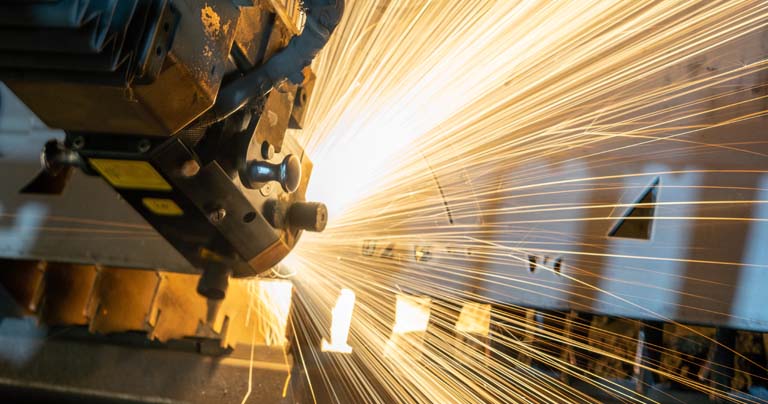
Experts across the welding and PEB segment will brief us on the significant impacts of latest trends, machineries and advanced technologies of welding and cutting on PEB construction.
The Indian market for pre-engineered buildings is expected to be worth USD 48.4 billion by 2030, with a CAGR of 11.66 percent. The market was valued at $18.1 billion in 2021.
Structural welding is majorly used in high-rise and huge buildings, and not much for small buildings, as it is in high-rise buildings that require thousands of metal joints. Over the course of the year, technological advancements have greatly assisted in the increasing quality of life through a variety of new products and services. Pre-engineered buildings were one such revolution.
Technologies are reshaping the welding industry.
Within the field of welding technology, requirements are constantly increasing with regard to quality, speed, precision, and efficiency, and that applies across all sectors. A customised welding system that is perfectly tailored to the respective requirements, is the key to high productivity and reproducible welding results.This not only call for innovative technologies, but also for high-quality, durable components that work together in perfect synchronisation.
V.V. Kamath, Managing Director, Fronius India Limited, says, “Wire Arc Additive Manufacturing (WAAM) is arousing a great deal of interest in several industries. Arc-based manufacturing by building up layers allows for a high degree of flexibility in component geometry. For prototypes and small-batch production runs in particular, WAAM is a more cost-effective solution than other additive processes for metal. “ The key factor in determining the quality of components produced is the welding process. Cold metal transfer from Fronius effectively fulfils all the conditions for wire arc additive manufacturing.
Technology advancements in welding
The Institute of Welding & Testing Technology, with 3D and WAAM technology, developed a few components and put them to the test. “We built certain components and tested them, but the material properties were uncovered afterwards. The obtained results further reduced the space being produced among the materials during metallurgy. Hence, standard metallurgical components are a vital aspect for welding processes, and with WAAM, we can be assured of metallurgy. However, lack of education and awareness towards WAAM technology and its benefits, “says Satish P. Sawant, Inspector & Surveyor, Institute of Welding & Testing Technology.
Adding more to the aspect, Amrityoga Mishra, Sr. Manager – Marketing, Panasonic Smart Factory Division, Panasonic India Pvt. Ltd., says, “We at Panasonic are constantly working to improve the precision and speed of our robots. We offer a series dubbed “towers” that are a distinction from other welding robots. Other welding robots are aware that they require a separate power supply. The robot provider will not be the power source supplier. Then there will be a demand for yet another robot supplier. Both of these elements needed to be integrated by the third person. The power source and the robot also have a communication link known as “serial communication.”
Welding for PEB design and engineering, as well as casting
India is aiming at becoming a 1 million, 5 trillion dollar economy by 2025. With the increasing number of pre-engineered buildings in India, the construction infrastructure sector in India is gaining prominence. Pre-engineered buildings are expected to revolutionise construction patterns due to an increase in PEB buildings and related activities across the construction sector.This transformational trend further creates avenues for industrial welding and welding practices across the country.
The design engineers create the demo structures in a way that enables the welding engineers and welding experts to create light-weight metal structures by adding precision in welding to create minute curves and add perfection during the welding processes. This reduces the weight of PEB structures by nearly 30% compared to conventional buildings.
Moreover, as per the views of R. Srinivasan Iyer, Past President, Indian Institute of Welding, “The tailormade building based on the requirements, along with the design calculation, adds perfection to a pre engineered building. Another thing is that there is an opportunity for us to do the design calculations using the different dimensional aspects of the building or of the infrastructure projects.“
Managing safety and security
The safety examination of the welding system must have been carried out by a properly trained person in order to protect the operating companies from legal liability. When the welding system is turned on, it is exposed to a variety of harsh ambient and environmental circumstances. Dust or metal contamination, wide fluctuations in temperature, mechanical loads (e.g. when transported) or humidity/rain are some of the types of conditions a welding system may experience.
Here, Kamath highlights some critical points that need to be looked at and must be avoided as far as possible. It includes personal injury, damage to equipment or property, production downtime, and avoids the legal consequences of an accident.
Even without malfunction, the welding process exposes those who are around welding to heat, radiation, foreign objects (slag), gases, and high electrical current. The use of personal protective equipment (PPE) and learning how to use it is critical in welding..
The operating company also has a duty to submit the welding machine for testing by a qualified technician to certify that it is safe for use following repairs or modifications, or as Fronius recommends, at a minimum, every twelve months for calibration of welding equipment.
Future prospects
This year’s budget had a blueprint for developing a vibrant ecosystem through research, design, and development in manufacturing within our country. Welding is already playing a major role in this manufacturing sector. Moving forward, welding automation and robotics will play a vital role in improving productivity and maintaining world-class quality. Skilling for welding can also be a focus area. As such, there is a real shortage in the availability of welding professionals.
Cookie Consent
We use cookies to personalize your experience. By continuing to visit this website you agree to our Terms & Conditions, Privacy Policy and Cookie Policy.