Terex MPS plant to execute Laos Dam project
By Edit Team | April 22, 2021 12:55 pm SHARE
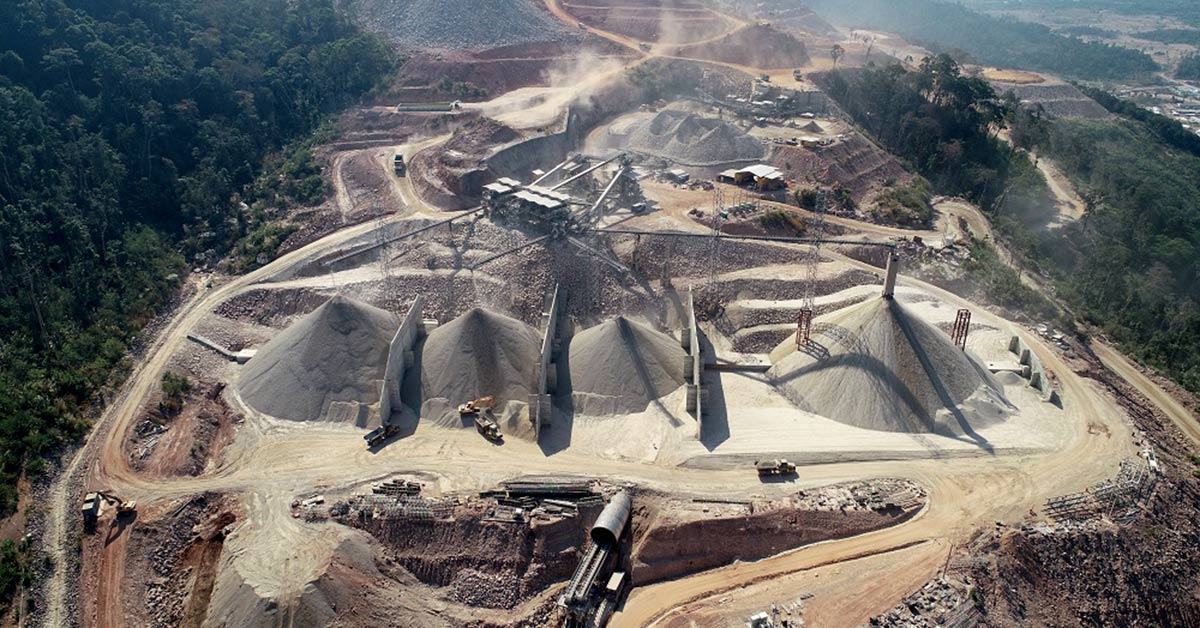
The dam, which is 105 m high and 700 m long at the top, will produce electricity in three groups: two units of 250 MW to be distributed in Thailand, and one group of 150 MW to be distributed for local use in Laos.
A joint venture of Italy’s Cooperativa Muratorie Cementisti (CMC) di Ravenna, Thai company Ital Thai and Vietnam’s Song Da Corporation is using a 1,500 mtph ICM – Terex MPS plant to produce aggregates for a 4 million m3 RCC (rolled compacted concrete) and 5 hundred thousand m3 CVC (conventional concrete) dam at the Nam Theun River, Bolikhamsay Province, Laos.
The dam, which is 105 m high and 700 m long at the top, will produce electricity in three groups: two units of 250 MW to be distributed in Thailand, and one group of 150 MW to be distributed for local use in Laos.
The solution consisted of a complete crushing plant to produce 1,500mtph of concrete aggregates. The plant is made up of two Simplicity Vibrating Grizzly Feeder 5220, two Cedarapids Jaw Crushers JS4552, four cone crushers, of which two are CedarapidsMVP550X and the other two are CedarapidsMVP450X, three ICM Vertical Shaft Impactor T-MAV 21, two CedarapidsHorizontal Screens TSV6202, and six Cedarapids Horizontal Screens TSV8203. Additionally, the set up includes an impressive 45 conveyors (total length of 1,400m), and the installation of 5,000kW of power.
The plant is being fed by blasted sandstone rock with a high abrasion index to produce 0/5, 5/12, 12/25 and 25/50 mm, as dictated by the mix design of the RCC, with any excess being recycled. A reclaiming plant transports aggregates from stock to a cooling plant via two downhill conveyors (one for coarse aggregates with a capacity of 1,800mtph and one for sand with a capacity of 700mtph). The supply is completed by a set of conveyors with a capacity of 1,000cmh to pour RCC into the dam.
Due to the abrasiveness of the sandstone, distributor ICM srl, Italy, designed the plant to use jaw crushers and cone crushers in the first instance to get the rock to the required size for the RCC—at this stage not worrying about the shape of the aggregate. Once sized, the shape is improved using the Vertical Shaft Impactors. Icilio Guicciardi, ICM explains, “This is a philosophy that always gives good results in terms of the quality of the aggregates and the reduction of wear costs. Having a solution that satisfies our customer’s strict requirements was of utmost importance to us and we knew that this plant set up would produce the output required.”
Commissioned in 2018, the plant was supplied by distributor ICM srl, Italy, who also completed all the engineering required (except civil works), equipment, electrical system (power and controls), steel work (hot galvanized), delivery, assistance to assembly and erection up to commissioning (with customer crew). The plant is now being operated by Sinohydro, with works expected to be completed in 2023.
Icilio Guicciardi, ICM continues, “This type of project is significant for ICM because it gives us prominence in the market and at the same enables us to supply an interesting line up of equipment in one shot. This is the third plant, in less than ten years, that ICM has supplied for the production of aggregates for the construction of a major project (dam, canal, etc.)—having supplied Panama with a plant to produce 3,300mtph of basalt and Ethiopia with a plant to produce 2,000mtph of granite. Through these projects, ICM has shown the added value that we provide to ensure the performance of our Terex MPS equipment, in particular our cones and screens, and in the speed of delivery and assembly of the plant—Panama was delivered in four months and started production in 10 months, while Ethiopia and Laos were delivered in three months and started production in 6 months.”
Paul Lilley, Sales Director, Terex MPS for the ERA said, “The plant installation at Laos Dam demonstrates how our equipment can be seamlessly combined to provide a tailored solution that consistently delivers aggregates that meet customer requirements—even in complex, extensive projects such as this. We have no doubt this plant designed by ICM will continue achieving ultimate efficiency and production output through to project completion.”
Cookie Consent
We use cookies to personalize your experience. By continuing to visit this website you agree to our Terms & Conditions, Privacy Policy and Cookie Policy.