The application of green materials assures high performance for concrete structures
By Edit Team | February 10, 2023 12:47 pm SHARE
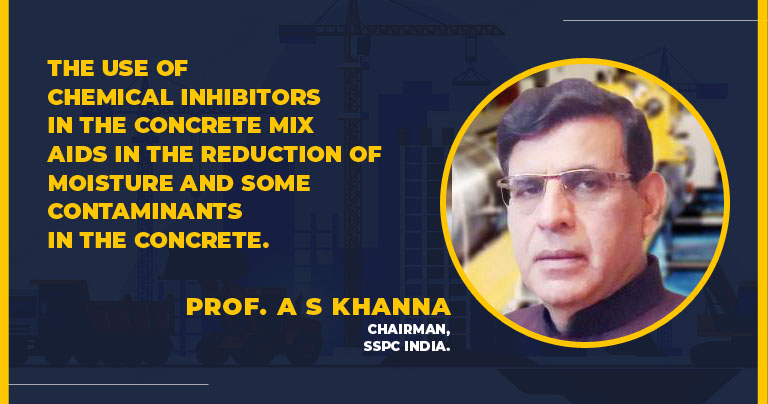
According to Prof. A. S. Khanna, President of SSPC India, “designing for sustainability” means protecting the environment both during creation and during the product’s existence.
What is the present market for construction chemicals and admixtures in Indian industries?
No concrete construction is rugged and long-lasting unless a proper and selective choice of construction chemicals is added to the concrete mix. Concrete per se gives basic strength to a structure; however, for further improvement in several micro and macro properties of the structure, the addition of construction chemicals is necessary. For example, several construction chemicals are added to enhance corrosion resistance to slow the diffusion of moisture and pollutants. Strengtheners such as silica fumes are added to concrete to create a nice bond and protect it from localised cracking. Likewise, there are other chemicals added for other property enhancements. According to a research report published by Persistence Market Research, this can be seen in the massive Indian construction chemical market, which is expected to be worth US $ 1539 million in 2022 with a CAGR of 13.4 percent, compared to a global market of US $ 44 billion in 2022.
Which technologies and the latest solutions are leading to sustainable needs at construction projects?
The basic requirement of a sustainable concrete structure is to ensure minimal environmental impact during its life cycle. For example, such construction should have a low energy requirement, minimal waste generation, use of enormous resources on earth that ensure no shortage, a durable long-term structure, and preferably be made from recycled materials. Using “green” materials, which have low energy costs, high durability, and a substantial proportion of recycled materials ensures little maintenance. Green materials use less energy and resources and can lead to high-performance cement and concrete. Designing for sustainability means protecting the environment during construction and ensuring the same during its life.
How do you look at the cost-effectiveness of concrete admixtures in the present market scenario?
Although some construction chemicals are expensive, their use in very small quantities, ranging from 0.5 percent to a maximum of 2-3 percent, significantly raises the cost.
What are the anti-corrosive and protective features of concrete admixtures, epoxy coatings, and grouts?
There are various methods of protecting concrete structures from corrosion. They can be divided into three categories:
- Use of anti-corrosive coatings on coated surfaces
- Use of chemical inhibitors
- Use of corrosion-resistant admixtures
The use of anti-corrosive coatings is prevalent. A simple protective epoxy coating on the concrete cover helps to keep moisture and pollutants out of the concrete cover, such as carbon dioxide, chlorides, and sulphur dioxide. A better coating is MIO epoxy, which is even more effective than pure epoxy as MIO helps form a solid barrier to these pollutants. Several anti-carbonation coatings are available on the market that resists the ingress of CO2 into the concrete. Epoxy coatings coat steel rebar to avoid rebar corrosion at the steel-concrete interface.
The second most common technique is chemical inhibitors in the concrete mix, which helps reduce the diffusion of moisture and certain pollutants within the concrete, especially in reinforced concrete structures where faster diffusion can initiate corrosion of rebar very quickly. Several inorganic and organic chemicals are available for use as inhibitors and are added at a concentration of not more than 0.5 to 1 percent. Calcium nitrate is a common inhibitor found in many concrete structures. There are also “vapour phase inhibitors” that work in two ways: they slow the diffusion of pollutants and diffuse onto a steel bar to protect it from further corrosion. This is called MCI technology. The waterproof coating is another requirement to seal the concrete surface.
What are the latest technologies and materials being added to the materials and solutions you provide for construction and infrastructure projects?
Today, we recommend using anti-carbonation coatings on all concrete structures, especially bridges, flyovers, and pedestrian crossing bridges, made in all big cities, to save the concrete structure from vehicular corrosion.
We recommend using MIO-modified epoxy coating on the concrete surface in all major cities near the coast or coastal towns such as Mumbai, Chennai, Kandla, and others to stop moisture and chlorides at the concrete cover.
To prevent corrosion of reinforced concrete structures, we recommend using galvanised rebars or Fusion Bond epoxy-coated rebars for structures in the C3 and C4 environments and stainless steel for the C5 and C5M environments. These must be additionally coated on the cover with an epoxy coating and use calcium nitrite as the chemical inhibitor in the concrete admixture and silica fume for strength, as shown in a well-accepted model of corrosion prevention for RCC structures (Fig. 1).
For more details visit: https://www.sspcindia.org/
Cookie Consent
We use cookies to personalize your experience. By continuing to visit this website you agree to our Terms & Conditions, Privacy Policy and Cookie Policy.