The cost-effective revolution in metal 3D printing
By Edit Team | August 18, 2023 2:34 pm SHARE
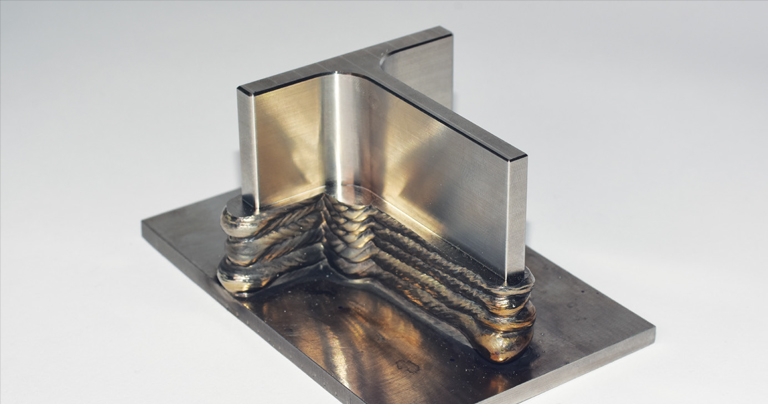
There are several advantages to 3D printing, not least its high deposition, and multi-wire solutions could even increase deposition rates in the future.
Wire-arc additive manufacturing, or Direct Energy Deposition (DED), is arousing a great deal of interest in the industry. Manufacturing using arc-based layer deposition enables a high degree of flexibility in component geometry. The process is particularly cost-effective and resource-efficient for prototype construction, repairs, restoring damaged components, and small-batch production. The welding process is the key factor that determines the quality of the components produced. Cold Metal Transfer from Fronius effectively fulfils all the conditions for Wire Arc Additive Manufacturing.
Additive production methods generate components by building up materials layer by layer. The best-known example of an additive method is 3D printing. Direct Energy Deposition or Wire Arc Additive Manufacturing, which are based on the arc welding process, also produce metal parts layer by layer, with the layers formed by the consumable wire electrode. Generative methods like this are particularly advantageous when complex component geometries have to be produced, as the design options are virtually limitless. What’s more, parts can be manufactured at low cost and extremely quickly, which makes Wire Arc Additive Manufacturing a very attractive option for prototype construction and small production batches. Processing time, tool wear, and material loss during machining—especially with the conventional approach of milling out the workpiece from a solid block—all generate significant additional costs.
What Is Direct Energy Deposition (Arc-DED)?
There are a number of generative production methods for metal. Essentially, these can be divided into two fundamental types: powder-based processes and wire-based processes. In powder-based processes, the layers are built up using molten metal powder. The most common method, the powder bed process, produces extremely precise results but is somewhat slow in production. Wire-based processes, on the other hand, build up the component by melting a filler metal in the form of a wire. These processes require the use of a laser, electron beam, or arc. They also have a high deposition rate and therefore help cut production times.
Direct Energy Deposition is a wire-based process that uses the gas metal arc welding process (GMAW). There are a number of advantages to 3D printing, not least its high deposition rate (up to four kilogrammes per hour with steel materials), and multi-wire solutions could even increase deposition rates in the future. Equipment and material costs are also important criteria, which is another strength of Arc-DED. All that is required is a suitable welding system, and there is no need for costly special equipment, such as the vacuum chambers needed for the faster electron beam process.
In comparison to powder-based processes, Wire Arc Additive Manufacturing also benefits from the immediate availability of a range of certified wire types. There are relatively few powder-based materials to choose from, as it can take years to acquire the necessary certification and to produce data sheets since the use of metal powder is still a relatively new technology.
Challenges with Wire-Based 3D Metal Printing Systems
“With Arc-DED, you have a semi-automatic process at your disposal that already uses the benefits of computer-assisted manufacturing (CAM). However, the manufacturing process has not yet reached the highest level of autonomy,” explains Philip Roithinger, New Business Employee, at Perfect Welding, Fronius International GmbH, adding that “The welding specialist’s welding expertise is still required for path planning.” In order to ensure a stable production process, optical and thermal sensors are used. For a good 3D printing result, it is crucial to first identify the right weld path and appropriate welding parameters. In addition to this, an automated welding system is required to ensure the necessary geometric precision. Maximum welding process stability, good heat management, and exact predictability are also essential for this. Construction strategies are also required for series manufacturing, where results are repeated and can be transferred to multiple welding systems via “copy and paste.”
“Cold” Welding Process for Strong Layers
A stable welding process and effective heat dissipation are essential for component production using large-scale 3D metal printing. The welding process needs to be sufficiently low-energy so that when a new layer is applied, the existing layers do not melt again. In other words, the process needs to be as “cold” as possible. Furthermore, the weld layers need to be continuous, spatter-free, and consistent; this is because any flaws would be replicated in each subsequent layer.
The CMT GMAW process from Fronius and its process control variants meet these requirements. They produce a stable arc and a controlled short circuit with long short-circuit times. Two process control variants of CMT are particularly well suited to wire-arc additive manufacturing. One is the CMT additive process characteristic, which has been optimised for large-scale 3D metal printing. It achieves high deposition rates while transferring very little heat into the component. With the CMT Cycle Step variant, each droplet detachment can be individually controlled, enabling high-precision work and increasing reproducibility. The CMT Cycle Step variant reduces the arc power even further through the controlled deactivation of the arc during the process phase. However, this particularly “cold” process does take longer to build up the layers as the deposition rate is lower.
The key factors determining the quality of a component produced using Wire Arc Additive Manufacturing are the stability of the welding process and low heat input—the Cold Metal Transfer GMAW process from Fronius fulfils these requirements.
The reversible wire electrode used in the CMT welding process mechanically supports droplet detachment. This means that less energy is needed and long short-circuit times are achieved—for a “cold” welding process.
Focus on Precision with Real-time monitoring
During 3D printing, deviations are replicated from one weld layer to the next, thereby affecting the geometry of the resulting product. This means it is all the more important not only to avoid deviations as much as possible but also to correct them immediately, should any still occur. The Fronius ArcView camera system provides a direct view of the arc and the layer structure. The welding process can be visualised in exceptional detail using impulse-controlled image generation in the dark phase of the arc. This provides real-time monitoring of the ongoing welding process. If necessary, the welding technician can take corrective action immediately and directly, allowing them to achieve the desired result.
Fronius Arc View offers a continuous, real-time view of the welding process and layer structure.
Real-World Wire Arc Additive Manufacturing Applications
Countless large-scale components have already been produced using Fronius welding technology and 3D metal printing in a variety of sectors. These include fan impellers for energy generation, which are made from high-grade materials. Milling the workpiece is very expensive due to the high material consumption rate, while casting is not always able to meet the critical metallurgical properties required for walls that are only 1.5 mm thick, for example. Using 3D printing and Wire Arc Additive Manufacturing based on the CMT Cycle Step, these fan impeller blades can be produced from a nickel-based alloy using an additive approach. It is even possible to repair components using wire-arc additive manufacturing.
Fronius has also implemented another application with a partner in the aviation sector. Titanium is a frequently used material in aircraft construction thanks to its tensile strength, resilience, corrosion resistance, and low weight. The majority of the components are manufactured using subtractive methods, whereby up to 90 percent of the material is milled away. This causes high costs, long machining times, and costly tool wear. By contrast, components produced using 3D metal printing only need to be reworked to produce a smooth surface. The titanium components produced using the CMT additive process do not exhibit any problems with lack of fusion and have impressive metallurgical properties. As a result, tool costs, machining times, and wear can be reduced, meaning that overall machining costs can be brought down.
With Wire Arc Additive Manufacturing, components are “welded up” layer by layer before being mechanically reworked. In the example here, a component is being produced from titanium.
3D Metal Printing: Cost-Effective and Flexible
This makes arc-based additive manufacturing a cost-effective and flexible alternative for component production. The additive process can be adopted with relative ease using welding technology from Fronius and the CMT solution.
For more details, visit: www.fronius.com
Cookie Consent
We use cookies to personalize your experience. By continuing to visit this website you agree to our Terms & Conditions, Privacy Policy and Cookie Policy.