The green sparks driving industry change
By Staff Report | March 18, 2025 2:18 pm SHARE
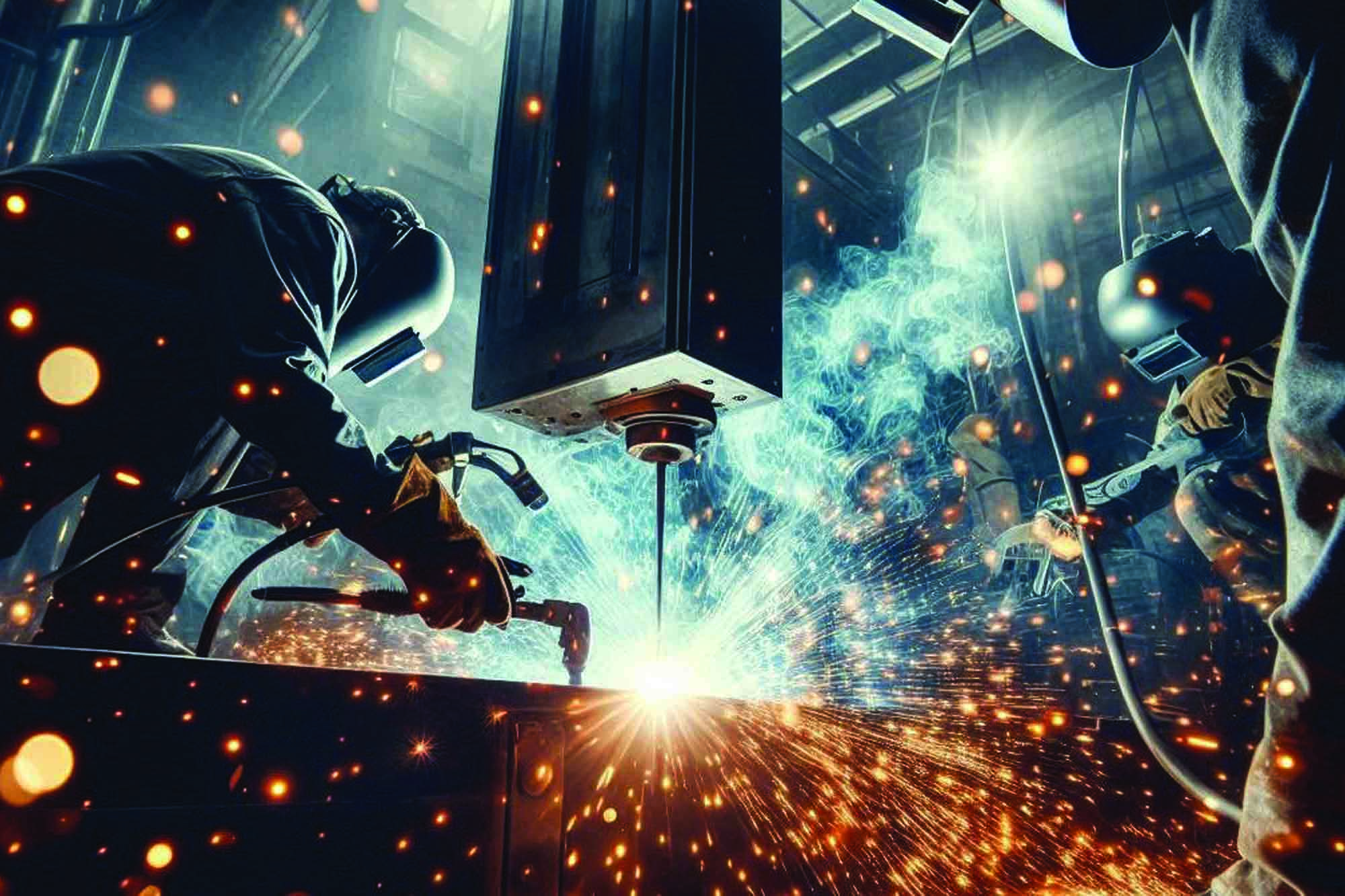
The welding and cutting industries are entering a new era of innovation and sustainability. With mounting pressure to boost productivity and lower carbon footprints, these sectors are embracing automation and smart technologies at an unprecedented pace.
The conventionally conservative cutting and welding industries have started to embrace automation, smart technologies, and eco-friendly solutions to meet the world’s evolving demands. These sectors are playing a critical role in establishing a sustainable and technologically advanced future as enterprises face mounting pressure to enhance operational efficiency and lower their carbon footprint.
The global welding market is projected to grow from $26.7 billion in 2023 to $35.1 billion by 2028 at a 5.7 percent CAGR, driven by automation and smart manufacturing. In India, rapid infrastructure development toward a $5 trillion valuation by 2047 fuels demand for advanced welding and cutting solutions. Sustainability is driving innovation in welding and cutting, with a focus on reducing energy use and promoting eco-friendly materials. The shift to renewable energy, EVs, and green buildings opens new opportunities, pushing industry leaders in India and globally to invest in R&D for efficient, environmentally responsible welding solutions.
The role of automation and IoT
One of the most significant transformations within welding and cutting today is the move towards automation, robotics, and Internet of Things (IoT)-driven technologies. Industry leaders agree that automation is essential, particularly in high-volume sectors such as automotive manufacturing. According to Lajpat Yadav, Chief Operating Officer at Ador Welding, robotic welding plays a crucial role in automotive manufacturing, where it has become indispensable to maintaining competitiveness. “If you don’t shift to robotics, you are not very competitive,” he explained. “For automotive manufacturers, it’s no longer optional—it’s necessary.”
In contrast, for industries like construction, automation is a more mechanised process rather than robotic, but it still significantly improves productivity and quality. Automation also helps reduce dependence on highly skilled labour, enabling companies to scale operations while ensuring consistent results. Yadav emphasised that the Internet of Things (IoT) has also become a critical element in the transformation of welding and cutting operations. “We have to adopt smart factories. Today, even in the automotive industry, people like Mahindra control everything on the shop floor,” he said. “The welding industry must do the same. Data must be captured across all stations, analysed, and used to improve productivity and quality.”
Mohit Bhalla, Managing Director of Bhavin Tech Consultants Pvt Ltd, echoed these sentiments, drawing a parallel between welding technology and the IoT advancements in other sectors. “Today, welding machines come with IoT technology. You can monitor gas consumption, arcing frequency, and even the performance of the machine based on different operators,” he explained. “This data is essential for improving performance, reducing costs, and enhancing overall efficiency.”
Sustainability and green solutions in welding
As India works toward its green infrastructure goals, integrating sustainability into the welding process has become more crucial than ever. Yadav shared insights into how Ador Welding is contributing to these efforts, particularly through the development of high-productivity solutions and IoT-integrated technologies. “We are very much aligned with India’s green infrastructure goals,” he stated. “Technologies that were once perceived as available only from global leaders are now being developed right here in India, and we are proving that these solutions are competitive on a global scale.”
Yadav’s remarks underline the potential for domestic manufacturers to not only meet India’s green infrastructure needs but also to compete internationally. This shift toward homegrown innovation helps reduce reliance on foreign technologies and supports the “Make in India” initiative.
Preparing the workforce for the future
The biggest challenge the welding industry faces today is the skill gap. Despite the availability of advanced technologies, there is a shortage of skilled workers capable of operating these sophisticated systems. Both Yadav and Bhalla emphasise the importance of workforce readiness in ensuring the success of these technologies. “A lot of people in the welding industry, even after years of experience, don’t know basic things like which electrode they’re using,” Bhalla said. “The challenge lies in upgrading the workforce, especially when it comes to adopting automation and robotic technologies.”
The issue, according to Bhalla, is not just about technological adoption but also a mindset shift. “The biggest difficulty we face is changing people’s mindset. They don’t want to embrace change,” he observed. “We need to coach people and provide them with the foundational skills in basic logic and mathematics so that they can handle automation and robotic systems effectively.”
Dilip Chavan, Head of Training & Testing at the Institute of Welding and Testing Technology highlighted the importance of hands-on training in overcoming these challenges. He stressed that many workers do not understand the basic principles of welding, such as the relationship between current, voltage, and travel speed. “Practical training is essential,” he said. “Without understanding the basics, workers cannot improve their performance or adapt to new technologies.”
Addressing the aging infrastructure challenge
As infrastructure in India and around the world ages, there is an increasing demand for advanced welding techniques that can extend the lifespan of existing structures. One area where welding is making a significant impact is in the repair and maintenance of aging infrastructure, such as railway tracks and industrial machinery. Yadav provided an example from the Indian railway system, where welding technologies are being used to enhance the durability of railway tracks. “In the past, the tracks would need to be repaired after a certain weight load, but with the new welding technologies, we are able to double the lifespan of these repairs,” he explained. “This is a game-changer for infrastructure maintenance, saving time and costs while improving efficiency.” This approach is not limited to the railways. Yadav mentioned that similar innovations are being applied in the steel industry and cement plants, where welding techniques are extending the life of critical equipment. “Indian companies are proving that we can provide solutions that meet global standards, reducing the need to rely on imports,” he noted.
Bridging the gap between training institutions and industry needs
As technology continues to advance, collaboration between industries and training institutions is becoming increasingly important to ensure that workers are equipped with the latest skills. Bhalla emphasised the importance of partnerships between industry players and educational institutions to bridge this gap. “We are collaborating with polytechnic institutes and industry partners to provide vocational training,” he explained. “The goal is to raise awareness about the opportunities in the welding industry and equip the workforce with the skills required for the modern demands of the sector.”
Chavan echoed this sentiment, stating that global training standards play a vital role in enhancing India’s welding workforce. “Standardisation ensures consistency in training and certification, which is crucial for increasing the employability of welders,” he said. “It’s important that welders see themselves as professionals, just like doctors or engineers. This shift in mindset is essential for the future of welding in India.”
Embracing change for a competitive future
The future of welding and cutting lies in continued innovation, sustainability, and collaboration across industries. As the sector embraces automation, IoT, and green technologies, it will play an increasingly important role in shaping the future of infrastructure, manufacturing, and construction. “To stay ahead, we need to adopt high-productivity solutions and IoT technologies. These are no longer optional; they are the future of the industry,” according to Chavan.
The future of welding and cutting is undoubtedly exciting, with the potential for automation, sustainability, and skill development to reshape industries across the globe. As these technologies continue to advance, the welding industry in India is poised to play a pivotal role in the growth of infrastructure, repair, and sustainable development.
Quotes
Lajpat Yadav, Chief Operating Officer, Ador Welding:
“We’ve proven that world-class high-productivity solutions and smart welding technologies can be made in India. With the government’s ‘Make in India’ initiative, we’re raising the bar, manufacturing advanced products with local components that match and surpass global standards.”
Mohit Bhalla, Managing Director, Bhavin Tech Consultants:
“The biggest challenge is resistance to change. We need to coach people on the logic behind automation and robotics. COVID-19 taught us the importance of virtual tools—now we must apply the same adaptability to technical training and upskilling.”
Dilip Chavan, Head of Training & Testing, Institute of Welding and Testing Technology:
“Even experienced workers often don’t know the basic specifications of the electrodes they use. Proper hands-on training is crucial. Welding depends on current, voltage, and travel speed—and understanding these basics can dramatically improve output quality.”
Cookie Consent
We use cookies to personalize your experience. By continuing to visit this website you agree to our Terms & Conditions, Privacy Policy and Cookie Policy.