The Indian welding industry is gearing up for the prevailing and the future market dynamics
By Edit Team | October 17, 2020 2:57 pm SHARE
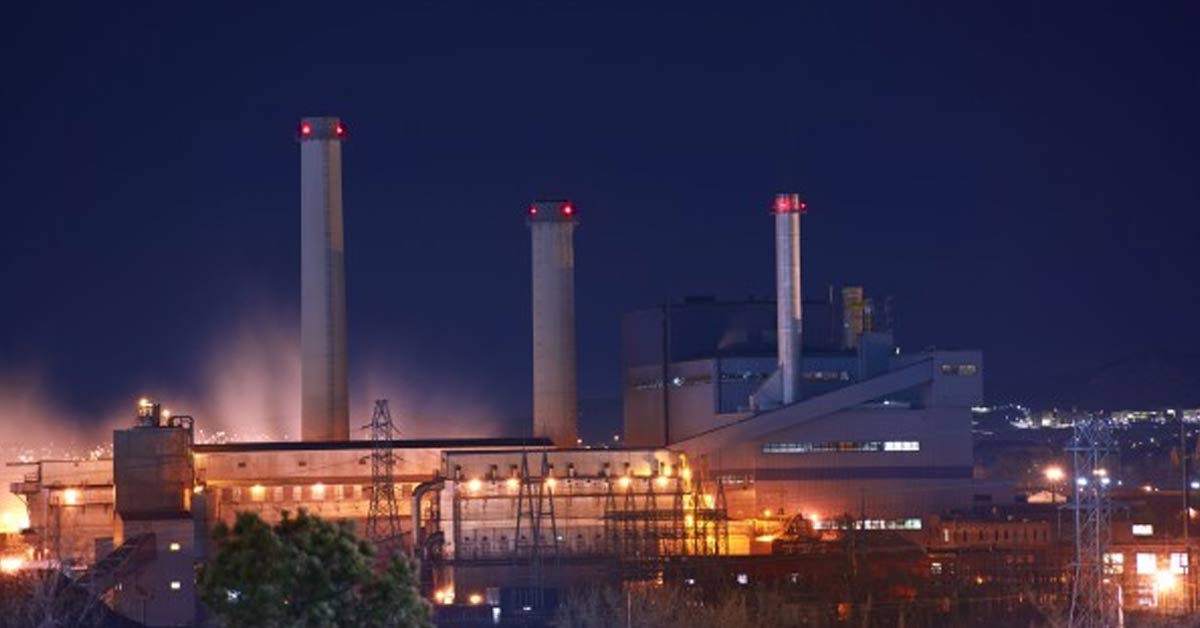
From safety of manual welders in the shopfloor to digitizing welding operations and workflows, Indian welding industry is readying itself to embrace the uncertain future.
In a timeline when most of the construction and infrastructure projects are either delayed or in a restart mode the welding industry is investing its time wisely. The protection of manual welders and the intense digitization and mechanization of welding processes are the two factors which are gaining traction across the shop floor.
“Our suppliers and customers are slowly reopening for business but it will not be business as usual. Safeguarding workplace health has become the top priority,” says Amrityoga, Sr. Manager – Marketing, Panasonic Smart Factory Solutions India “We are now using internet-based communications, wearable devices and sensors, device cleaning systems, maintain social distancing and safety. We have started to adopt mobile computers and scanners enabled warehouse and production floor to maintain social distancing without compromising on productivity. We are also trying to upgrade our suppliers to enable them to become more digitalized to enable remote communication on a realtime basis.”
“It is recommended, he continues further “that welding operators should wash their hands with soap and water and make sure that their hands are dry before starting the welding work. Welding operators should avoid using sanitizers as they contain a certain amount of alcohol and there are chances of flammability. However, in case they still have to use sanitizers, it is needed to ensure that their hands are completely dry before resuming welding work.”
The Indian welding industry was as such dominated by low technology and very rare technological innovation. Though the demand for automatic and semi-automatic welding production systems were there, budget constraints continue to ensure the popularity of manual, economical techniques. Increased FDI equity inflow in India has contributed to the rise in industries impacting the welding sector in a big way, thereafter many foreign automobile companies also set up their manufacturing units in India. This has positively affected the rise of consumables and welding equipment.
However, Covid -19 crisis has impacted the flow of FDI in India which can result in decline in demand of welding equipment over the short period, however, what it has started is intense digitization and mechanization of welding processes which otherwise would have remained a distant dream. Considering that the government is keen to become Atmanirbhar, many players see it as a right time for Indian manufacturers to compete with welding equipment made in India which has a considerable share in the local as also the global markets.
“The cost of manpower and resources will go up further in the coming days. There is going to be a spike in demand over the next couple of months and automation and robotics will lead the way to cater to this demand,” says Nimesh Chinoy, Marketing Director, SigmaWeld, Electronics Devices Worldwide Pvt Ltd. “The way to be competitive and serve the global market the acceptability of mechanized solutions and AI will go up. It was always a question of cost, now the question will be of opportunity cost. Are you willing to let go of the opportunity due to lack of resources? Or are you willing to set up and be ready to cater to the demand in unexplored markets? ‘Made in India’ will be an alternative for people, businesses and organizations across the world who are willing to consider it, compared to ‘Made in China’. The opportunity is there, we need to make the most of it.”
Cookie Consent
We use cookies to personalize your experience. By continuing to visit this website you agree to our Terms & Conditions, Privacy Policy and Cookie Policy.