The metal fabrication industry is witnessing a manpower shortage
By Edit Team | October 20, 2020 6:29 pm SHARE
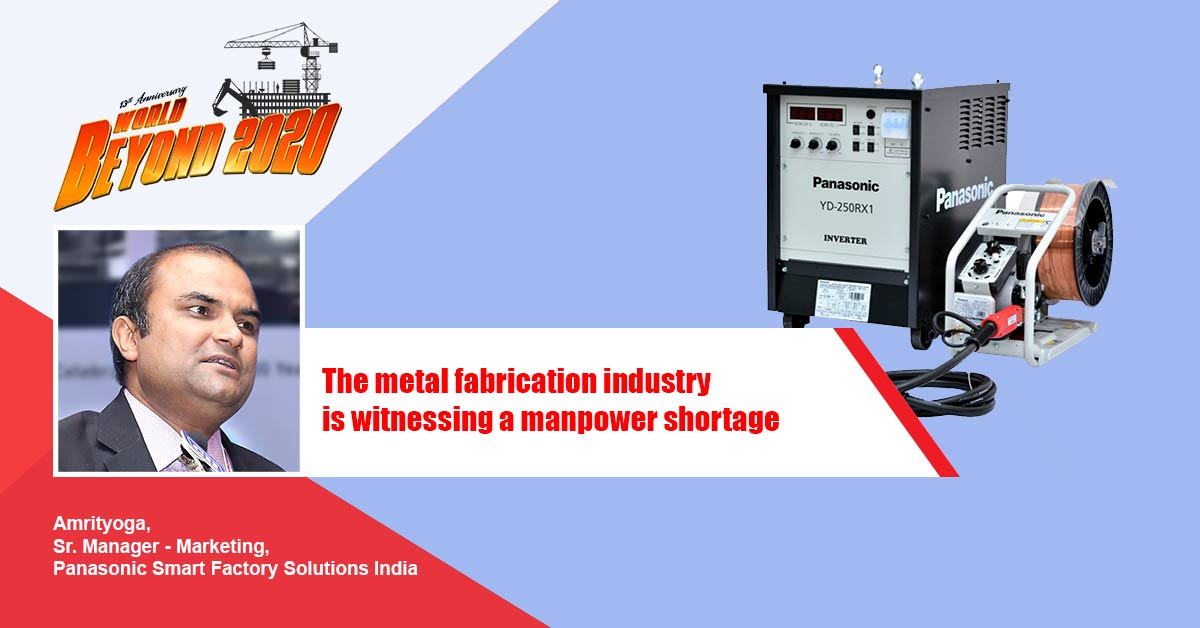
Companies now are trying to use automated welding processes, digital welding machines and enable remote monitoring of welding activity with the help of IoT enabled software says Amrityoga, Sr. Manager – Marketing, Panasonic Smart Factory Solutions India.
How do you see Atmanirbhar Bharat to impact your sector?
Many steps have been taken by the Government of India under ‘Atmanirbhar Bharat Abhiyan’.
Mining sector: The government increased the private sector role in mining while removing many hurdles for private company mining in the coal sector. This is expected to increase mining activity transparently. Many coal-based power plants are in a half-completed situation and they are expected to be completed now giving rise to demand for welding power plant equipment and on-site welding of these plants. The demand for Earthmovers and Tipper trailers are expected to increase to augment the need for welding activity. Relaxation of Foreign Direct Investment (FDI) limit in defence is expected to increase in house fabrication and thus increase in welding activity demand.
Privatization of six airports in India: The govt has privatized Lucknow, Ahmedabad, Jaipur, Mangaluru, Thiruvananthapuram and Guwahati airports. It is expected that beautification of these airports will involve more stainless steel and aluminium welding. Also, better and efficient handling of passengers is expected to increase passenger traffic and expansion of airport sooner rather than later will involve huge welding activity.
The Indian AC industry with sales of around six million units is largely dependent on imported compressors now after antiChina feeling in India, there is expected to be more and more manufacturing of compressors in India and this means a huge rise in welding activity.
What are the changes you foresee in the welding industry supply chain in the post-pandemic world? Our suppliers and customers are slowly reopening for business but it will not be business as usual. Safeguarding workplace health has become the top priority. We are now using internet-based communications, wearable devices and sensors, device cleaning systems, maintain social distancing and safety.
We have started to adopt mobile computers and scanners enabled warehouse and production floor to maintain social distancing without compromising on productivity. We are also trying to upgrade our suppliers to enable them to become more digitalized to enable remote communication on a real-time basis.
In terms of current market dynamics, what will be the new normal for the welding industry in 2020? Many migrant welding workforces have returned home and metal fabrication industry is feeling the pain. Companies have started to work on three fronts now. One automates the welding process, second is go for digital welding machines which support the less mature operator to create fast and quality welding output and third is remote monitoring of welding activity with the help of IoT enabled software.
This Covid crisis is pushing companies to adopt the latest welding technology to reduce dependency on manual intervention, which process would have otherwise been a slower adoption process.
For manual welders, what additional safety measures will become a new norm owing to the pandemic?
Protective clothing is critical for welding safety. The heat and radiation during welding can cause serious burns, can cause blindness and can cause respiratory damage in some cases. Therefore welder’s standard PPE kit should include leather shoes with a steel toe, sturdy pants such as jeans, a heavy overcoat made of leather, gloves, glasses and a welding helmet.
It is recommended that welding operators should wash their hands with soap and water and make sure that their hands are dry before starting the welding work. Welding operators should avoid using sanitizers as they contain a certain amount of alcohol and there are chances of flammability. However, in case they still have to use sanitizers, it is needed to ensure that their hands are completely dry before resuming welding work.
What products from your stable are driving growth for your business in the current economic cycle? There are three industry trends which are helping our business to grow in automotive industry – (1) High tensile steel welding (2) Multi material welding and (3) Digital manufacturing solutions.
(1) High tensile steel welding: There is a demand for light weight, higher body strength, high energy efficiency and more safety and thus high tensile steel is coming in higher use. Our Super Active Tawers robot with Heat Balance Control (HBC) is catching up in the automotive industry.
(2) Multi material welding: This is getting popular in the automotive industry. And thus our laser welding solutions are catching up for multi-material welding like Mild Steel, Stainless Steel, Aluminium, CFRP (Carbon fibre reinforced plastic). Laser welding is fast replacing conventional spot welding as laser welding is 5-6 times faster.
(3) Digital manufacturing solutions:
• IWNB (Integrated Welding Network Box) – collects records and analyses data of welding robots automatically to provide a solution to improve – productivity, quality and traceability.
• LINKWIZ- Automatic Bead Inspection system in the welding process – Inspection is carried out from human to robot. It judges by 3D high accuracy images. No dedicated jigs for inspection required.
Cookie Consent
We use cookies to personalize your experience. By continuing to visit this website you agree to our Terms & Conditions, Privacy Policy and Cookie Policy.